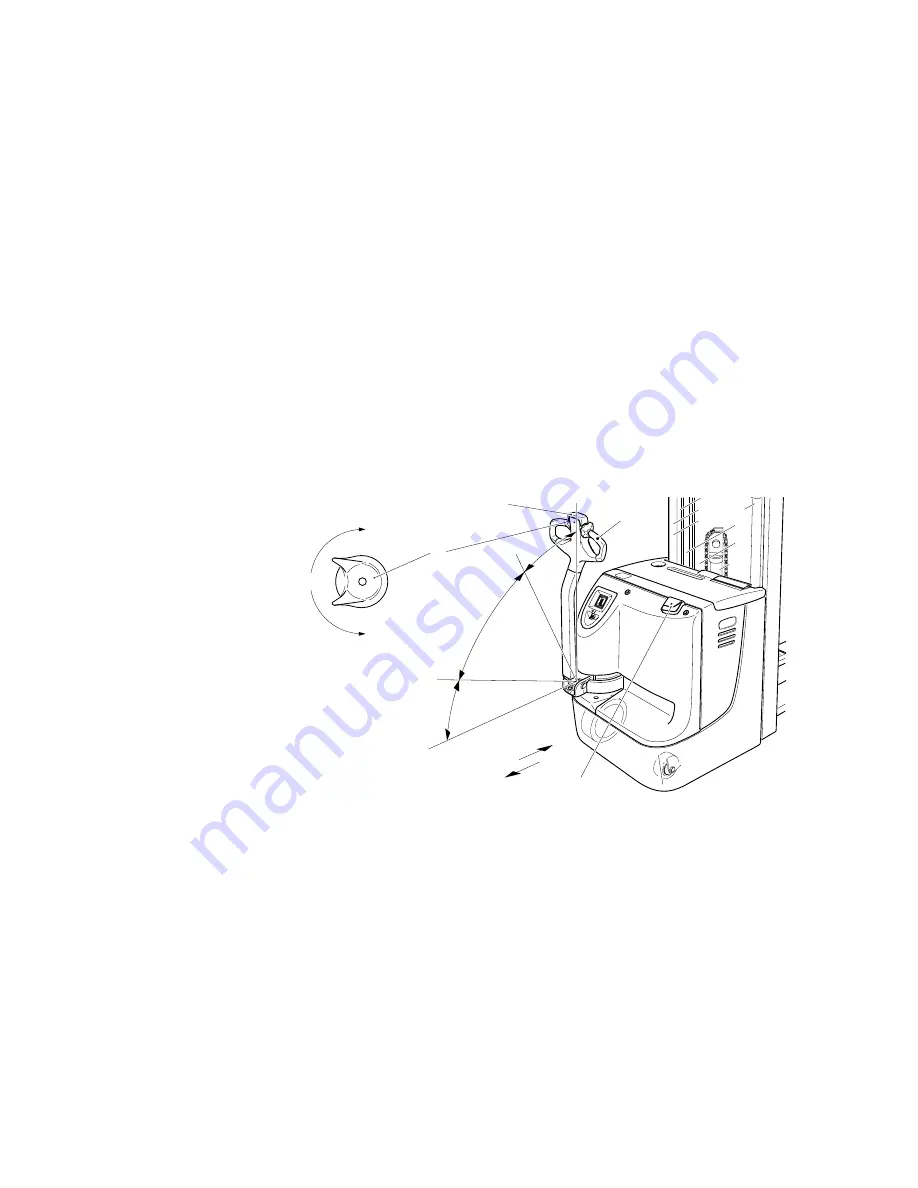
040
1.G
B
E 8
Braking
f
The braking effect of the truck is mainly depending on the road surface. This must be
taken into account by the driver for his driving behavior.
The truck may be braked in three ways:
– Using the service brake (control shaft (4)),
– Using dynamic braking (roll-off brake can be adjusted by the service),
– Control with regenerative brake via the drive control (8).
A
For standard driving operations, only the dynamic brake and that counterflow brake
are to be used, since these brake types are reduce wear and tear and help to save
energy (energy return supply).
Braking with the service brake:
f
In case of danger, the truck must be braked with the service brake (control shaft (4)).
– Swivel control shaft (4) upwards or downwards into one of the braking ranges (B).
The drive motor is mechanically braked.
A
When the control shaft (4) is released, it swivels into the upper braking range (B).If
the truck is parked, the service brake is used as parking brake
Dynamic braking (roll-off brake):
– After releasing the driving switch (8) - driving switch set to zero - the truck is braked
with the help of the dynamic brake (roll-off brake), depending on the selected set-
ting.
f
If the roll-off brake was deactivated by the service, only service brake and counterflow
brake are available.
Braking with the counterflow brake:
m
If the control system or driving mechanism breaks down, the counterflow brake beco-
mes ineffective.
– Do not turn the drive control (8) into opposite driving direction.
A
The braking effect depends on the position of the driving switch.
0
R
R
V
B
F
B
V
4
8
9
1
040
1.G
B
E 8
Braking
f
The braking effect of the truck is mainly depending on the road surface. This must be
taken into account by the driver for his driving behavior.
The truck may be braked in three ways:
– Using the service brake (control shaft (4)),
– Using dynamic braking (roll-off brake can be adjusted by the service),
– Control with regenerative brake via the drive control (8).
A
For standard driving operations, only the dynamic brake and that counterflow brake
are to be used, since these brake types are reduce wear and tear and help to save
energy (energy return supply).
Braking with the service brake:
f
In case of danger, the truck must be braked with the service brake (control shaft (4)).
– Swivel control shaft (4) upwards or downwards into one of the braking ranges (B).
The drive motor is mechanically braked.
A
When the control shaft (4) is released, it swivels into the upper braking range (B).If
the truck is parked, the service brake is used as parking brake
Dynamic braking (roll-off brake):
– After releasing the driving switch (8) - driving switch set to zero - the truck is braked
with the help of the dynamic brake (roll-off brake), depending on the selected set-
ting.
f
If the roll-off brake was deactivated by the service, only service brake and counterflow
brake are available.
Braking with the counterflow brake:
m
If the control system or driving mechanism breaks down, the counterflow brake beco-
mes ineffective.
– Do not turn the drive control (8) into opposite driving direction.
A
The braking effect depends on the position of the driving switch.
0
R
R
V
B
F
B
V
4
8
9
1
Summary of Contents for EJC 14
Page 1: ...Operating instructions 10004249 EJC EJC Z 14 16 G 06 98 01 06...
Page 3: ...0108 GB...
Page 7: ...0600 GB A 2...
Page 12: ...B 5 0401 GB h4 h3 h1 l2 l1 l c y Q h5 h2 h31 h13 b5 Ast W a B m2...
Page 17: ...0401 GB B 10...
Page 21: ...0401 GB C 4...
Page 34: ...E 3 0401 GB 2 1 3 4 5 8 8 10 11 12 9 13 14 15 16 7 6...
Page 43: ...0401 GB E 12...