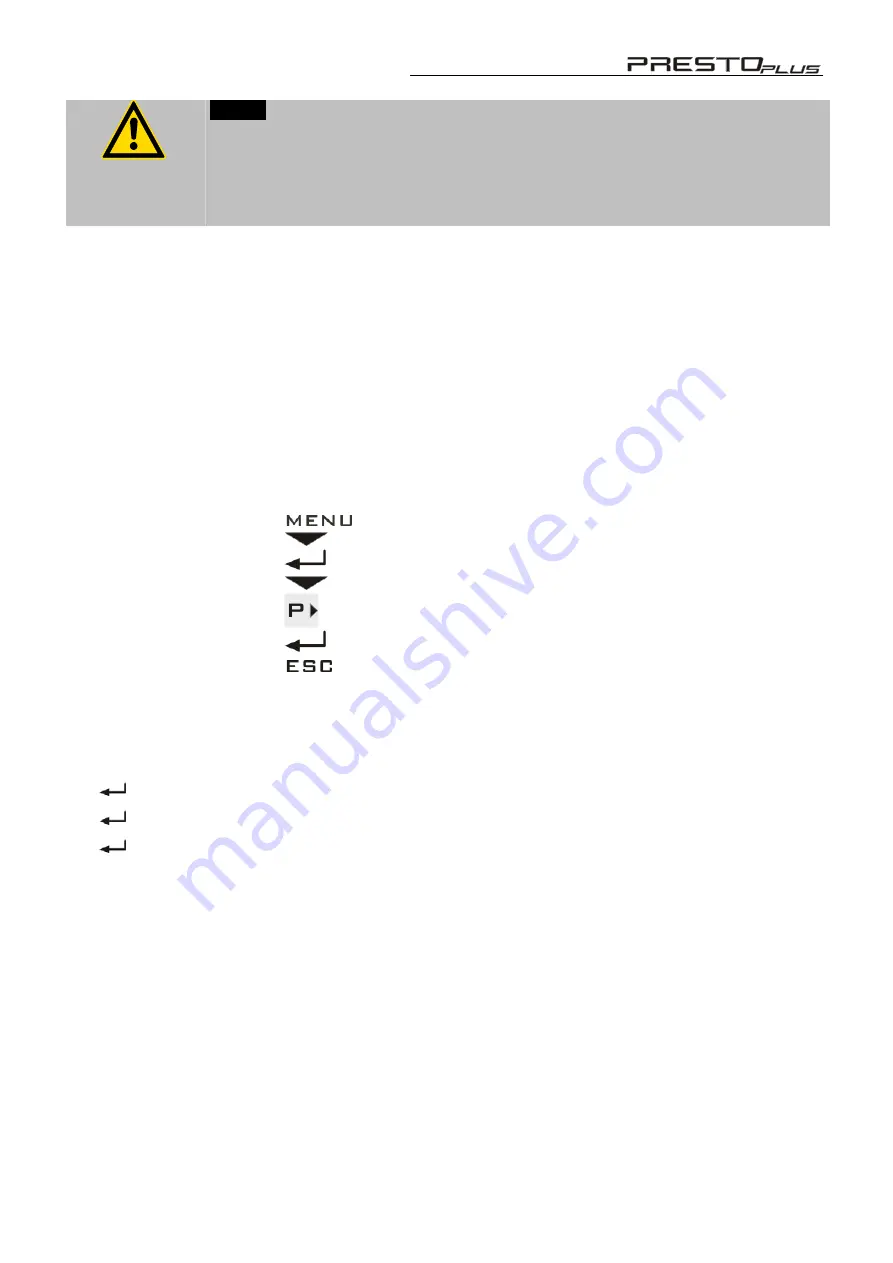
31
Notice:
In the >Mode< > fill < or. >drain<>SELECT SYSTEM< is shown when starting.
The message >SELECT SYSTEM<is a demand to make an adjustment in the menu
>Pump<.
The insertion is effected cyclicly until the adjustment has been made.
Adjusting Mode:
Notice concerning the filling
The temperature system was emptied last, therefore the menu option >Mode< now still
stands on >drain<. In the configuration of this unit the >Mode< >fill< means the same as
>drain< and therefore does not have to be adjusted.
Explanation of terms:
>Mode: sys close< stands for closed, external system (Presto principle page 22)
Press the respective keys in the following order:
1. MENUE
key
1x
2. Cursor
key
up to Submenu "Pump"
3. Enter
key
1x
4. Cursor
key
1x up to "Pump"
5. P-
key
sys close / fill / drain
6. Enter
key
1x
7. Escape
key
2x
The DIALOG-DISPLAY (LCD) helps to follow up the individual settings.
The VFD-Info Display shows the recently chosen operating status for approx. 3 seconds.
Switch over to > sys close <
CLOSED SYSTEM
Switch over to > fill <
FILL SYSTEM
Switch over to >drain<
DRAIN SYSTEM
Summary of Contents for Presto Plus LH 47
Page 20: ...Operating controls and functional elements 20 Rear...
Page 41: ...41...