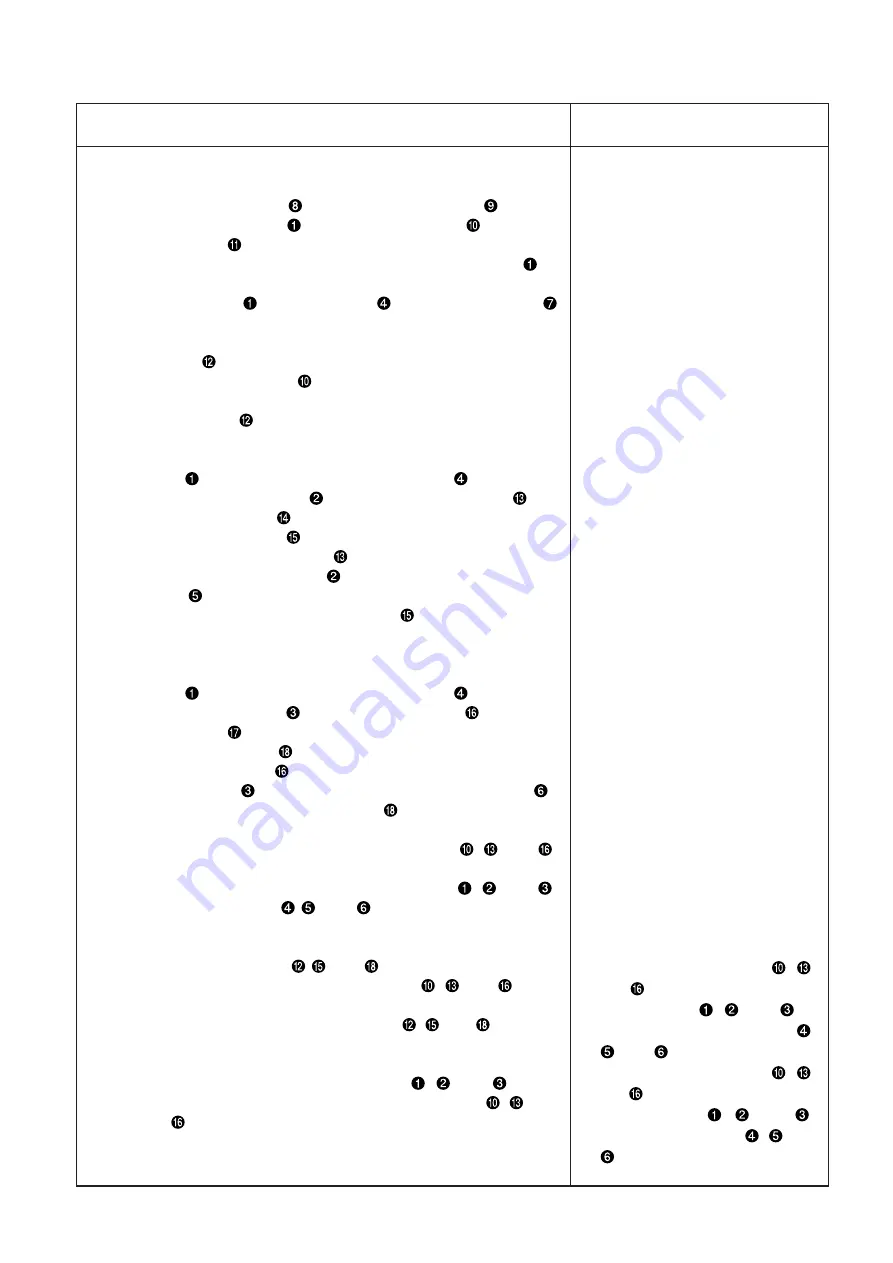
– 17 –
1) Looper return
(1) Front looper
1. Loosen the setscrews
to remove the throat plate
.
2. Mount the front looper
on the front looper base
and tighten
the setscrew
.
3. Rotate the pulley counterclockwise, move the front looper
to
the most left position, and measure the clearance from the tip of
the front looper
to the left needle
with the looper gauge
or a scale.
4. For adjusting the clearance to the standard distance, loosen the
setscrew
securing the front looper base to adjust the position
of the front looper base
in the right-left direction.
5. After adjustment, tighten the setscrew to secure the front looper
base setscrew
.
(2) Middle looper
1. Rotate the pulley counterclockwise and align the tip of the front
looper
with the left surface of the left needle
.
2. Mount the middle looper
on the middle looper base
and
tighten the setscrew
.
3. Loosen the setscrew
securing the middle looper base and
move the middle looper base
in the right-left direction to align
the tip of the middle looper
with the left surface of the right
needle
.
4. After adjustment, tighten the setscrew
to secure the middle
looper base.
(3) Rear looper
1. Rotate the pulley counterclockwise and align the tip of the front
looper
with the left surface of the left needle
.
2. Mount the rear looper
on the rear looper base
and tighten
the setscrew
.
3. Loosen the setscrew
securing the rear looper base and move
the rear looper base
in the right-left direction to align the tip of
the rear looper
with the left surface of the middle needle
.
4. After adjustment, tighten the setscrew
to secure the rear looper
base.
(Caution) When the positions of each looper base (
,
, and
)
are adjusted in the right-left direction, adjust the
clearances from the tips of the loopers (
,
, and
)
to the needles (
,
, and
) as well.
2) Adjustment of the clearance between the looper and needle
1. Loosen the setscrews (
,
, and
) securing the looper bases
to adjust the positions of the looper bases (
,
, and
) in the
front-rear direction.
2. After adjustments, tighten the setscrews (
,
, and
) to secure
the looper bases.
(Caution) When the clearances are adjusted, check the looper
return positions for each looper (
,
, and
) in the
right-left direction because the looper bases (
,
, and
) may move in the right-left direction.
o Insufficient or excessive looper
return may cause stitch skipping,
needle breakage, or thread
breakage.
o When each looper base (
,
,
and
) is moved leftward, each
tip of loopers (
,
, and
) is
detached from each needle (
,
, and
).
o When each looper base (
,
,
and
) is moved rightward, each
tip of loopers (
,
, and
)
touches each needle (
,
, and
).
Adjustment Procedures
Results of Improper Adjustment
Summary of Contents for 35800 Series
Page 8: ...MEMO 4...
Page 61: ......