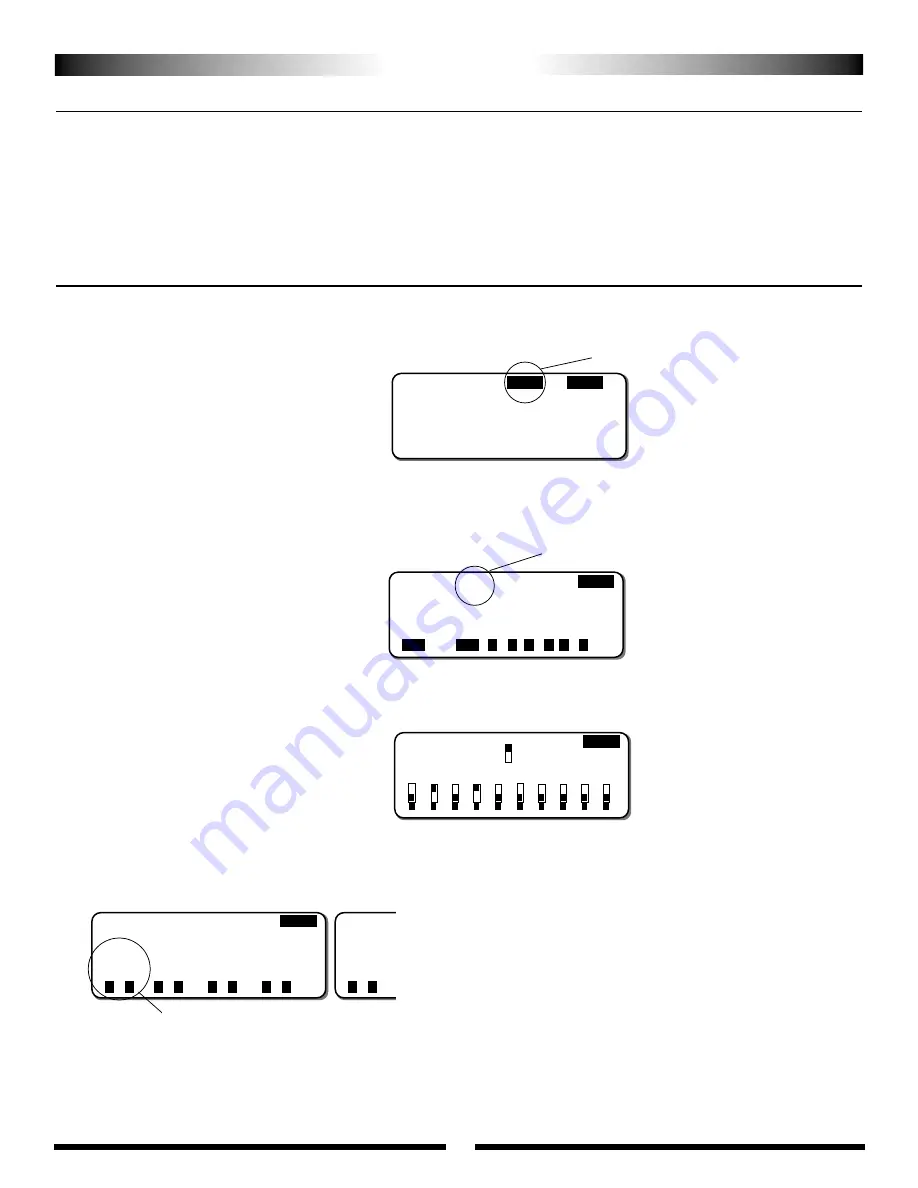
CCPM SOFTWARE ACTIVATION AND INITIAL ADJUSTMENT (CONTINUED)
22
The following activation and setup procedure should be used for all JR PCM10, 10S, 10SX, 10SXI, and 10X systems.
Prior to activating the CCPM function, it is first suggested that a Data Reset function be performed to reset the desired model number to
be used back to the factory default settings. If you are using a new radio system, proceed to Step B.
Caution:
prior to performing the Data Reset function, it will be necessary to select the desired model number to be used. Access the
Model Select function (Code 84) and select the desired model to be used.
A) Access the Data Reset function (Code 28) once the correct model number has been established. Next, press the
Clear
key to reset the
current model. Press the
Enter
key to exit the Data Reset function.
B) Access the Swash Type function (Code 65). Next, press the
Sel
key until “3 SERVOS” (120°) appear on the screen. Once this is
complete, it will be necessary to change the value of the functions from the factory default setting to the values as shown using the (+)
and (-) keys below. Press
Enter
to exit the Swash Type function.
C) Access the Servo Reversing function (Code 11). Next, reverse channels 2 and 4 by pressing the desired channel number. The screen
should appear as shown. Press
Enter
to exit the Servo Reversing function.
D) Access the Travel Adjust function (Code 12) and adjust the servo travel values as shown. Please note that the required travel values will
vary based on the type of servo selected. Press
Enter
to exit the Travel Adjust function.
Note:
The travel values shown for the rudder function are for use with Piezo type gyros, like the JR NEJ-900, NEJ-400, NEJ-450, or
NEJ-3000 type gyros. If a conventional mechanical type gyro is used (JR 120, 130, etc.), then the travel value of the rudder channel
will need to be reduced to approximately 100%.
3. JR 10 SERIES SYSTEMS
SET-UP PROCEDURE
[DATA RESET]
MODEL 1
SPCM
CLEAR
ENTER
[SWASH TYPE]
3SERVOS(120•)
FXP
AILE
ELEV
PITCH
[NH
+70%
+70%
-65%
ENTER
SEL
ACT
+
–
CL
+
–
CL
+
–
CL
[TRAVEL ADJUST]
THRO
AILE
ELEV
RUDD
H120%
L100%
D100%
L150%
L120%
R100%
U100%
R150%
PAGE
+
–
CL
+
–
CL
+
–
CL
+
–
CL
[TRAVEL ADJUST]
PITCH
+100%
-100%
+
–
CL
+
–
CL
+
–
CL
[CLEAR]
SELECT 3 SERVOS(120°)
Standard Servos
Throttle travel values may vary,
depending upon engine used.
Proceed to page 24.
[REVERSE SW]
REVERSE
NORMAL
ENTER
1
2
3
4
5
6
7
8
9
10