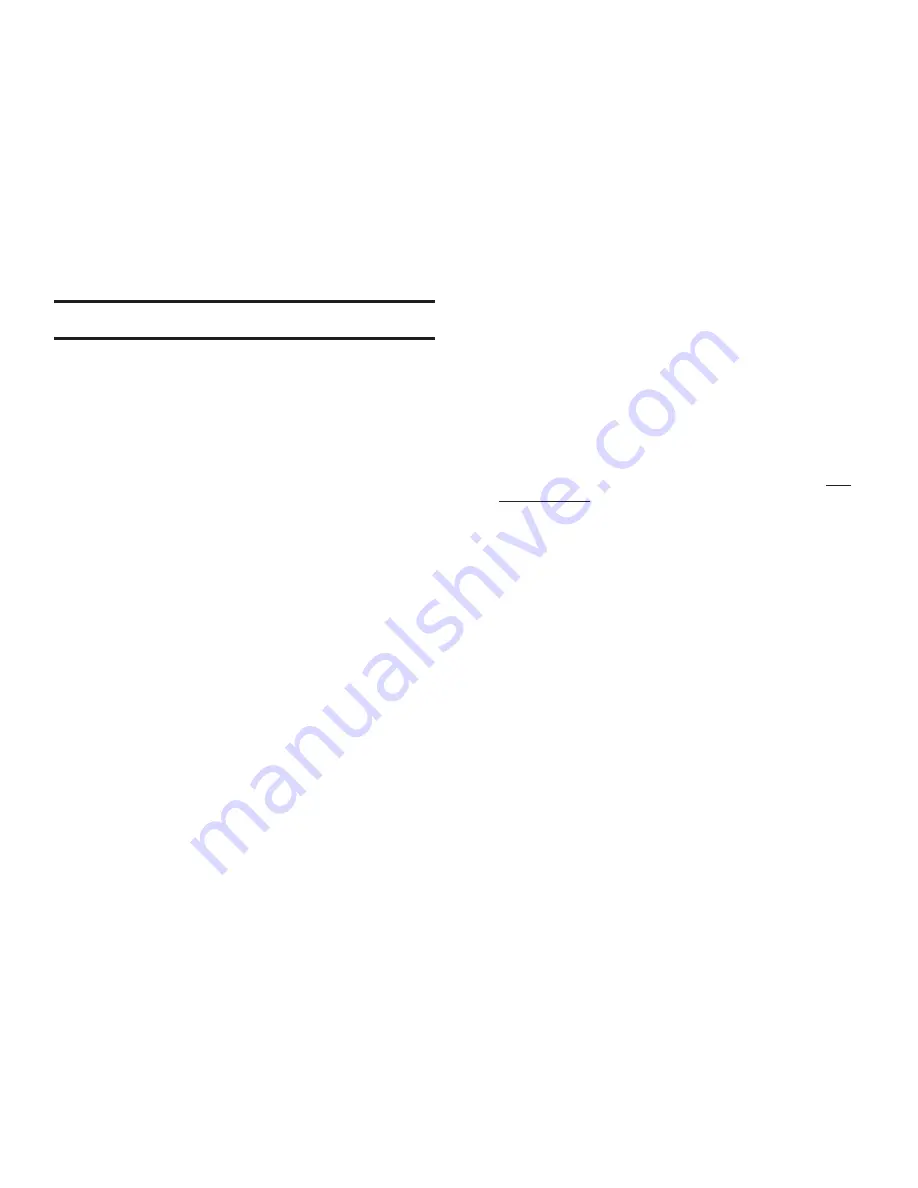
Maintenance
2. The control valve has been pre-set by Jordan Valve,
however, finer adjustment may be required to
compensate for the system conditions of your
application.
3. With inlet, outlet and bypass shutoff valves closed, and
no pressure in the down stream line, fully open the outlet
valve. Slowly open the inlet valve just enough to start
flow through the control valve. Increase the flow
gradually by slowly opening the inlet shutoff valve. Do
not fully open the inlet valve until you are sure that the
controller and control valve have control of the system.
Usually, the handwheel on the inlet valve will turn freely
when this point is reached.
4. To shut off the line fluid, close the inlet shutoff valve
first, and then close the outlet shutoff valve.
Caution: Make certain that there in no pressure in the
valve before loosening any fittings or joints. The
following steps are recommended:
1. Close the inlet shutoff valve.
2. Allow pressure to bleed off through the downstream
piping. Do not attempt to reverse the flow through the
valve by bleeding pressure from the upstream side of
the valve
3. When the pressure gauges indicate that all pressure
has been removed from the system, close the outlet
shutoff valve, and the valve may be serviced.
Note: refer to the drawing at the end of this document
for description and proper orientation of parts.
To reduce maintenance time, refer to proper figure and follow
steps indicated below for applicable maintenance operation.
Proposed Maintenance Procedure Follow Steps….
Renewing stem packing……………………..Packing
Replacement
Valve disassembly, inspecting
Parts, replacing plug or seat ring…………...Valve disassembly
Valve reassembly……………………………..Valve Reassembly
Actuator spring preload adjustment………..Actuator Spring
Load Adjustment
Actuator maintenance……………………......Actuator
Maintenance
Changing valve action……………………… Reversing Action
Motor valve seat spring preload…………….Motor Valve Seat
Spring Preload
Renew valve plug stem packing if control valve has been in
service beyond normal maintenance, and packing shows
signs of wear. Wear will be indicated by leakage, which
cannot be corrected by minor tightening of the packing
flange.An additional packing ring can be installed to
overcome minor leakage without dismantling the control
valve or breaking valve plug connection.
1.
Remove the actuator from the bonnet. (See Removing
Actuator from Valve.)
2.
Remove all of the packing and discard. Clean valve
stem and packing box thoroughly. The valve stem may
be dressed with a very fine crocus cloth, but generally
it is best not to as the stem has a fine machined finish.
Use approved non-residue-forming solvent for cleaning.
Wipe dry with clean cloth.
3.
Insert a new set of packing in packing box. Press each
ring down in place with a tube as it is installed.
4.
After packing is installed, assemble packing adapter,
gland, and gland nuts. Tighten the nuts hand tight.
5.
The final packing adjustment should be made with the
valve pressurized and the packing tightened just enough
to stop any leakage, while stroking the valve.
Excessive tightening could cause the stem to stick
and result in improper valve operation due to high
friction forces.
Packing Replacement
Removing Actuator from Valve
1a. Direct Acting Actuator (ATC): Shut off pressure to the
actuator and remove supply tubing from the actuator
case.
1b. Reverse Acting Actuator (ATO): Apply approximately 6
psig air pressure to the actuator to lift the plug off of
the seat.
1c. Motor Valve (Mark 709MV): Position the bottom inlet
to full open and disconnect all electrical connections.
2. Remove the actuator from the valve as follows: loosen
the two stem nuts and move them down the stem.
Lock these nuts together. Remove the two nuts that
secure the support legs to the bonnet. Using a wrench
on the nuts and on the flats of the actuator stem, turn
the valve stem (while holding the actuator stem in place)
until the stems disengage. The actuator will be free of
the valve.
Body & Bonnet Disassembly
1.
For actuator removal, refer to section on “Removing
Actuator”.
2.
Remove the body/bonnet bolts and carefully separate
the body from the bonnet so as not to damage delicate
trim components.
3.
Remove stem nuts and indicator. Loosen the packing
gland nuts and withdraw the stem and plug out of the
bonnet. (The smaller trims have a one-piece stem and
plug, which can be withdrawn through the packing.)
4.
With a socket wrench, remove both seats from the
body. Remove and discard the body/bonnet gasket.
5.
Soft seats are disassembled by removing the seat cap
from the seat and then the soft seat can be removed.
6.
Clean all parts with an approved non-residue-forming
solvent. Remove encrusted material with a very fine
Crocus or aluminum oxide cloth. However, do not use
these abrasives on the seating surface or the trim
surface (the portion of the plug that enters the seat
bore.) The machining tolerances on these surfaces are
so closely controlled that you might change the valves
flow characteristic.
7.
Inspect all parts and replace and worn or damaged
parts. It is always advisable to replace seals and
gaskets. DO NOT attempt to resurface seating surfaces
of the plug or seat. Seats and plugs are only sold in
factory-matched sets.
Valve Reassembly
1.
Soft seated valves: insert soft seat into the seat cavity,
install the seat cap and tighten.
2.
Lubricate the seat threads with a lubricant such as
NO-LOK and thread both seats into the body. Torque
to values shown.