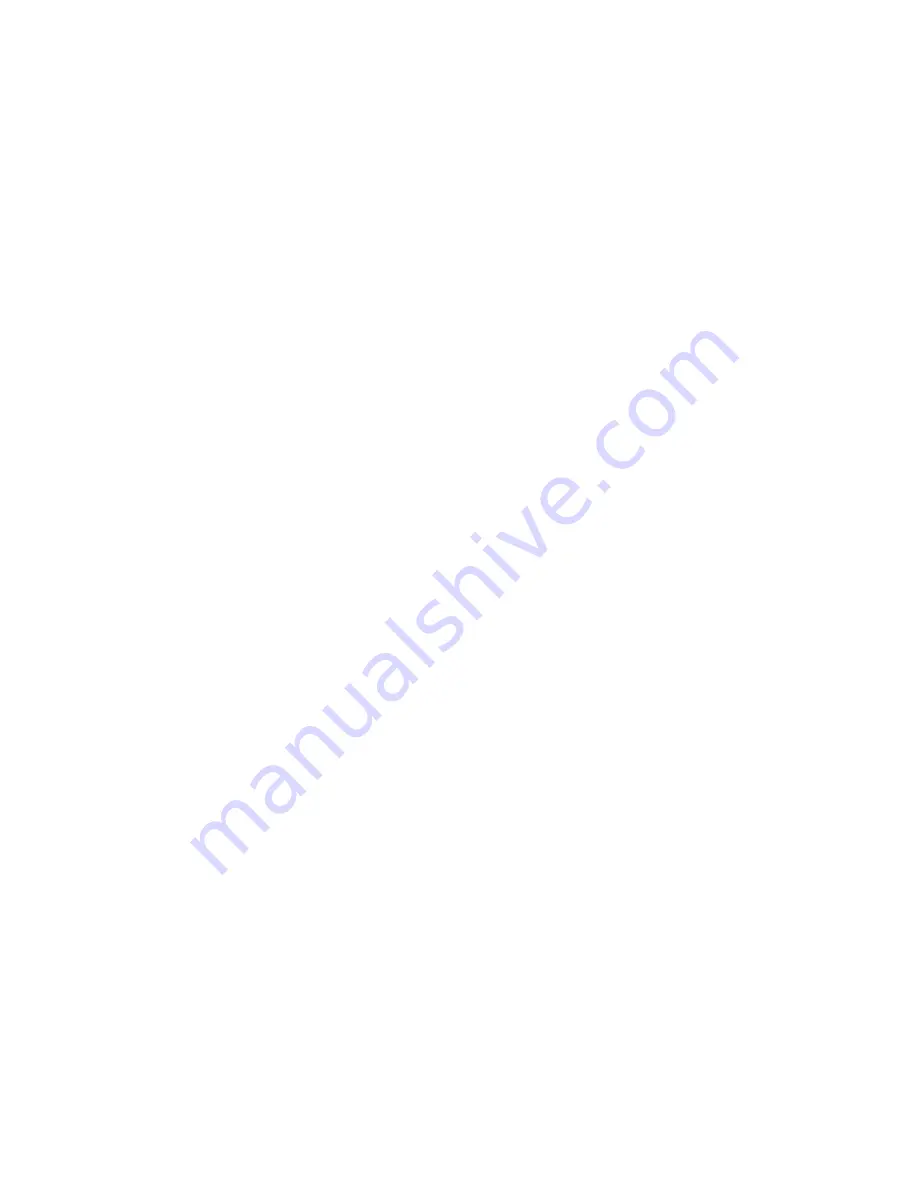
and discard the o-ring and two backup rings.
5.
If there is a need to clean the parts, use a solvent
that will not harm Buna-N elastomers, such as
Stoddard solvent.
Reassembly of Actuator — 7M & 14M
1.
Replacement of the actuator stem seal is
recommended. The o-ring and back–up rings are
standard Buna-N, size 112. Lubricate and install
the two back-up rings and the o-ring into the cavity
in the lower case. The back-up rings are installed
on either side of the o-ring.
2.
The retaining ring closest to the top end (bolted) of
the actuator stem must be in place. The retaining
ring nearest the other end ((with wrench flats) must
be removed.
3a. Direct Acting Actuator (ATC): attach the following
parts to the top of the actuator stem in the order
indicated: ThredSeal, diaphragm plate, diaphragm,
diaphragm washer, and lockwasher. Secure them
with the bolt. Hold the actuator stem on the wrench
flats and tighten the bolts.
3b. Reverse Acting Actuator (ATO): attach the following
parts to the top of the actuator stem in the order
indicated: ThredSeal, diaphragm plate, diaphragm,
diaphragm washer, and lockwasher. Secure them
with the bolt. Hold the actuator stem on the wrench
flats and tighten the bolt.
4a. Direct Acting Actuator (ATC): hold this assembly
by the bolt head in a vise, stem pointing upward.
Install the springs over the dimples in the diaphragm
plate. Take the lower case and carefully install it
onto the actuator stem by firmly pressing the stem
through the stem o-ring seal, keeping the springs
inplace. Install the retaining ring into the groove in
the actuator stem. This will keep the springs
compressed and prevent them from coming out of
place.
4b. Reverse Acting Actuator (ATO): install this assembly
into the lower actuator case by pressing the actuator
stem through the stem o-ring seal. Then install the
lower retaining ring onto the actuator plate. Next,
install the springs over the dimples in the diaphragm
plate.
5.
Position the flange of the diaphragm on the flange
of the lower actuator case and align the holes.
Attach the upper actuator case with the bolts.
6.
Reassemble the actuator to the valve as described
in “Valve Reassembly” steps 8 & 9.
Reversing Action
Changing the valve action from direct to reverse acting
or from reverse to direct acting. Reversing the action
of the actuator reverses the action of the Mark 709
Control Valve. The same parts are used for either action.
1. Disassemble the actuator as described in “Actuator
Maintenance”.
2. Reassemble the actuator with the desired action.
Refer to “Actuator Maintenance”. To change the
action of a motor valve, refer to Motor Manual IM-
0577 and Electric Connection drawing 95/C/032783,
which are provided with all Mark 708MV motor
valves.
Motor Valve Seat Spring Preload
1.
Position the bottom seat to be full open.
2.
The two stem nuts should be loosened and
threaded down the stem and then locked together.
3.
Slowly stroke the motor to closed position, while
rotating valve stem and stem nuts back and forth
(approximately ¼ turn). Caution: valve stem should
rotate freely. When it no longer rotates freely, the
plug is in contact with the bottom seat, and the
motor must be stopped or damage may occur. If
required, the valve stem may be threaded into the
actuator stem to allow motor to complete stroke.
4.
With motor in full closed position and stopped by
limit switch, rotate the stem down until the plug is
in contact with the seat, and turn and additional ¼
- ½ turn to preload the seat.
5.
Position motor to bottom seat open position, and
confirm that the motor is stopped by the limit switch
prior to the plug reaching the upper stop. Without
rotating the stem, thread the stem nuts up and lock
them against the actuator stem.
Note: limit switches and high/low set points are
factory-set. If command signal range will not fully
stroke the valve, refer to electrical connection
drawing 95/C/032783 for set point adjustment
procedure. With seat spring preload set, if plug hits
upper stop prior to limit switch, the limit switch will
require adjustment; consult factory for procedure.