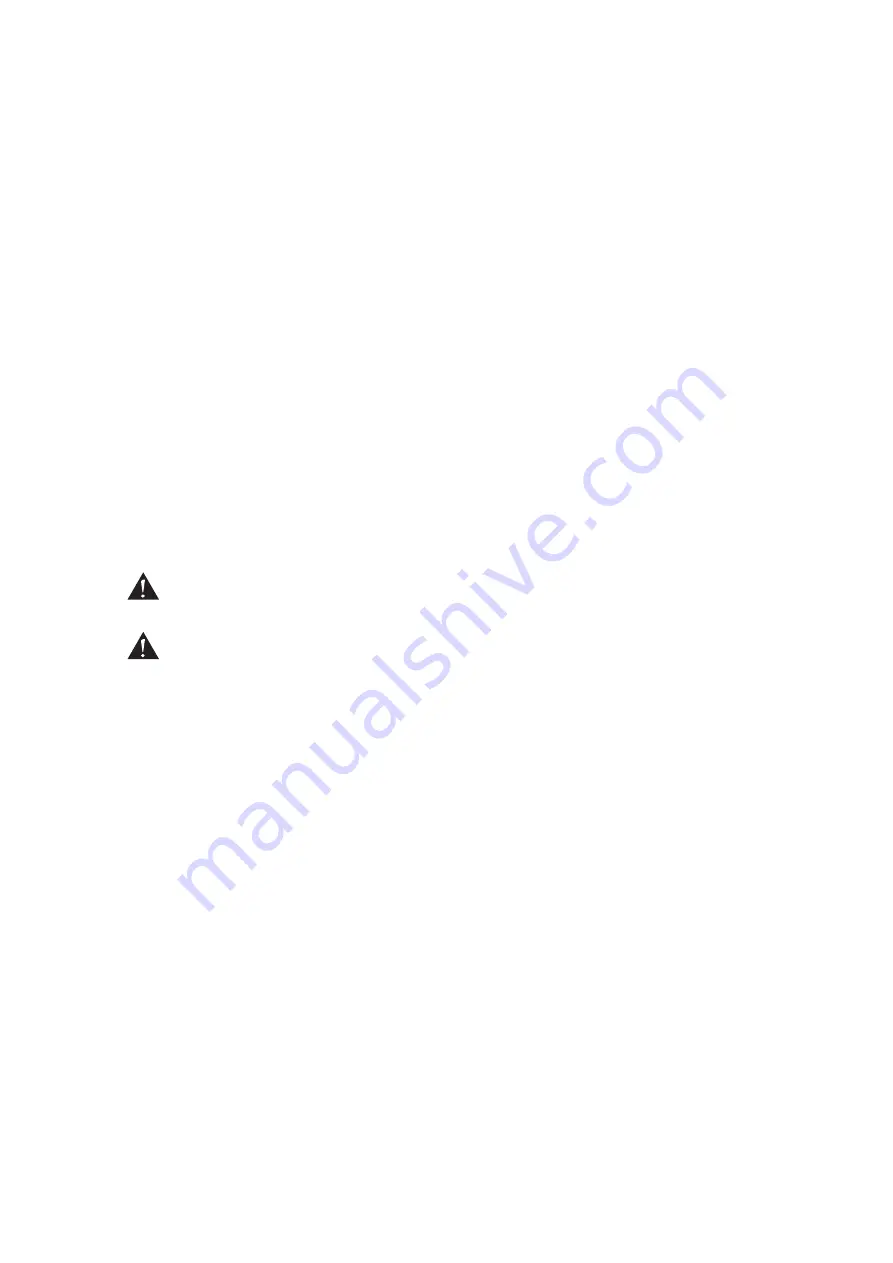
16
A.0500.601 – Atex IM -TG G/H/MAG/SRT/08.00 EN (01/2021)
• Follow the separate instructions for gear and motor drive and for explosion protected
shaft couplings.
• When using a belt drive, ensure the belts have sufficient electrical conductivity to avoid
electrostatic loads. Use only belts with electrical leakage resistance lower than 10
9
Ohm
and avoid using aluminium or light metal pulleys containing more than 7.5% magnesium.
• Certification of the protection guard must be included in the explosion protection
certificate of the drive or pump unit or should be certified separately by the manufacturer
or supplier of the guard. The coupling guard must be made of non-sparking materials.
Never use light metals containing more than 7.5% magnesium!
In case of
aluminium coupling parts or belt-pulleys, the coupling guard must be made of brass.
• For magnetically driven pumps, the size of the magnetic coupling (break-away torque)
must be selected in function of the start-up torque of the electric motor to avoid that the
magnetic coupling slips during start-up. This could lead to unacceptable high surface
temperatures and/or failure of the magnetic coupling and/or bearings.
3.6 Direction of rotation
• Gear pumps can run in both rotation directions: ensure that the relief valve or top cover
is set to the right direction of rotation, see IM.
• The pump units’ direction of rotation should be tested with the pump filled only, to avoid
dry running.
• If necessary the direction of rotation of the motor should be tested independently from
the pump i.e. not coupled to the pump. Remember to secure or remove the shaft key in
case of separate testing.
Always align the coupling after having disassembled it and refit the coupling
guard!
• TG MAG pumps are assembled for only one specific direction of rotation, due to the
internal cooling system of the magnetic coupling. The direction of rotation is indicated
on the name plate and with an arrow-plate on the top cover or the safey relief valve.
The last digit of the pump type description on the nameplate, (2) pump internals, is
indicating the direction of rotation:
R = clockwise seen from the shaft end
L = counter-clockwise seen from the shaft end
3.7 Piping
The suction and discharge lines should be designed properly for the required per-
formance conditions and should be executed accordingly (see IM). Non compliance to the
working conditions of the pump unit can cause severe problems such as NPSH-problems,
vapour lock, excessive vibrations and premature pump failure. Lines should be checked on
dimensions and tightness under pressure and should be internally cleaned and be free of
welding and foreign particles before they are connected to the pump.
3.8 Shaft sealing auxiliary connections
The gear pumps allow the application of several types of shaft seals. In order to ensure
proper functioning, venting and lubrication of the shaft seal a number of connections are
available which will enable liquid circulation or flushing. See IM for more information on the
possibilities and connections.
3.9 Check alignment
After installation the alignment of the pump shaft and drive shaft must be checked,
preferably with the pump and the pipes completely filled with liquid, and must be
corrected if necessary.