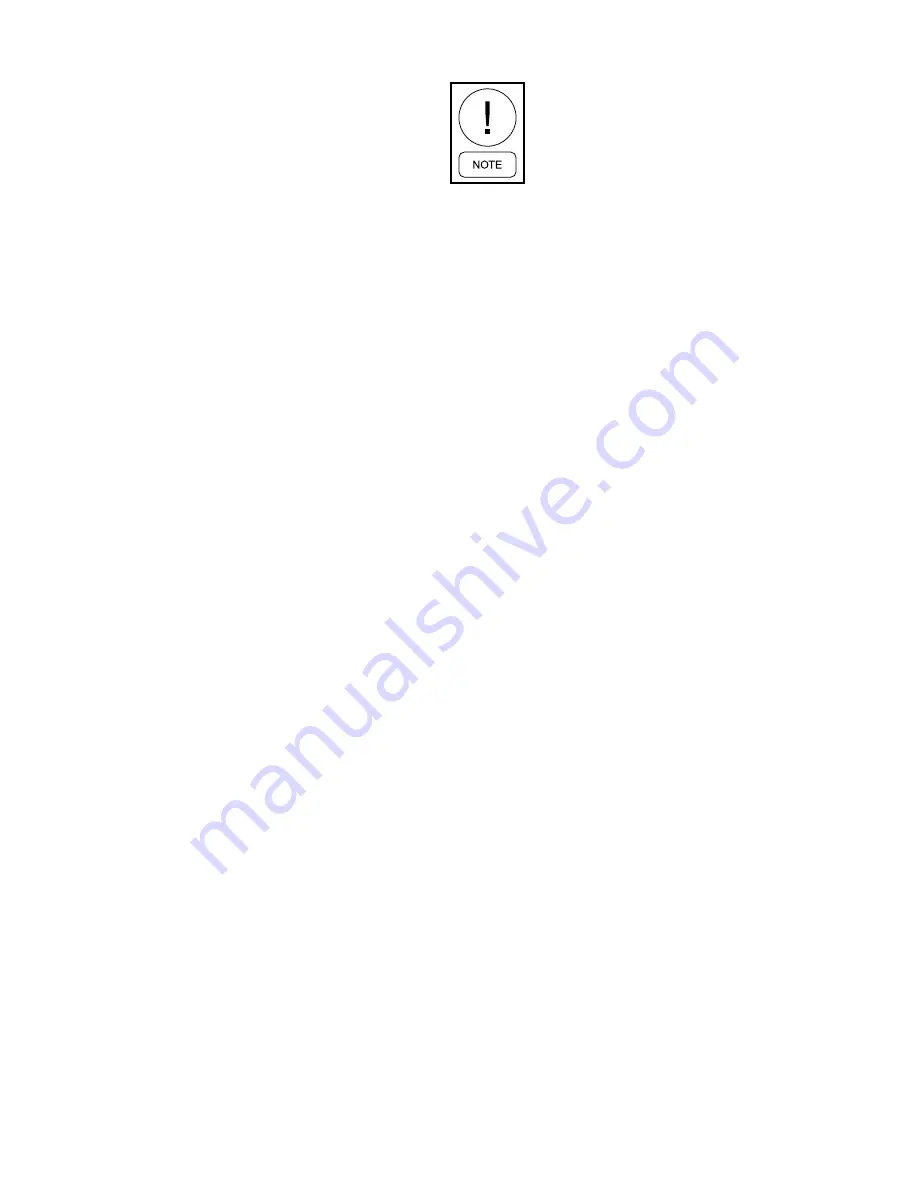
JOHNSON CONTROLS
18
FORM 150.27-NM1
ISSUE DATE: 09/30/2015
SECTION 2 – PRODUCT DESCRIPTION
EVAPORATOR
The 2-pass dual circuit shell and tube type direct expan-
sion (DX) evaporator has refrigerant in the tubes and
chilled liquid flowing through the baffled shell. The
waterside (shell) design working pressure of the cooler
is 150 PSIG (10.3 barg). The refrigerant side (tubes)
design working pressure is 450 PSIG (31.0 barg). The
refrigerant side is protected by pressure relief valve(s).
The evaporator shall have water pass baffles fabricated
from galvanized steel to resist corrosion. Removable
heads are provided for access to internally enhanced,
seamless, copper tubes. Water vent and drain connec-
tions are included. The cooler is insulated with 3/4"
(19mm) flexible closed-cell foam.
Water connection to the evaporator is via Victaulic
grooved connections. Flange connections are available
as an option. The shell will be constructed and tested in
accordance with Section VII, Division 1 of the ASME
Pressure Vessel Code. The water side is exempt per
paragraph U-1 (ºC) of Section VII, Division 1 of the
ASME Pressure Vessel Code.
The evaporator is constructed and tested in accordance
with applicable sections of the ASME Pressure Vessel
Code, Section VIII, Division (1). The water side will
be exempt per paragraph U-1, (ºC) (6).
A strainer with a mesh size between .5 and 1.5 mm (40
mesh) is recommended upstream of the evaporator to
prevent clogging.
CONDENSER
The condenser can be either a field supplied YORK
VDC remote air-cooled condenser (available separate-
ly from Johnson Controls) or an evaporative condenser.
REFRIGERANT CIRCUIT
Two independent refrigerant circuits will be furnished
on each unit. All piping will be copper with brazed
joints. The liquid line will include: a shutoff valve with
charging port; sight-glass with moisture indicator; ther-
mal expansion valve; solenoid valve; and high absorp-
tion removable-core filter drier. The entire suction line
and the liquid line between the expansion valve and the
evaporator will be insulated with flexible, closed-cell,
foam insulation.
MILLENNIUM CONTROL CENTER
All controls are contained in a NEMA 1 (and equiva-
lent to IP32) powder painted steel cabinet with hinged
outer door and includes:
•
Liquid Crystal Display with Light Emitting Diode
backlighting for outdoor viewing:
•
Two display lines
•
Twenty characters per line
•
Color coded 12-button non-tactile keypad with
sections for:
•
Control supply fuses and connections for a
remote emergency stop device.
•
ON/OFF rocker switch, microcomputer
keypad and display, microprocessor board,
I/O expansion board, relay boards, and 24V
fused power supply board.
•
Customer terminal block for control inputs
and liquid flow switch.
The microprocessor control includes:
•
Automatic control of compressor start/stop, an-
ticoincidence and anti-recycle timers, automatic
pumpdown on shutdown, evaporator pump and
unit alarm contacts. Automatic reset to normal
chiller operation after power failure.
•
Remote water temperature reset via a pulse width
modulated (PWM) input signal or up to two steps
of demand (load) limiting.
•
Software stored in non-volatile memory
(EPROM), with programmed setpoints retained in
a lithium battery backed Real Time Clock (RTC)
memory for a minimum of five years.
•
Forty character liquid crystal display, with de-
scription available in five languages (English,
French, German, Spanish or Italian).
Refrigerant R410A is field supplied.