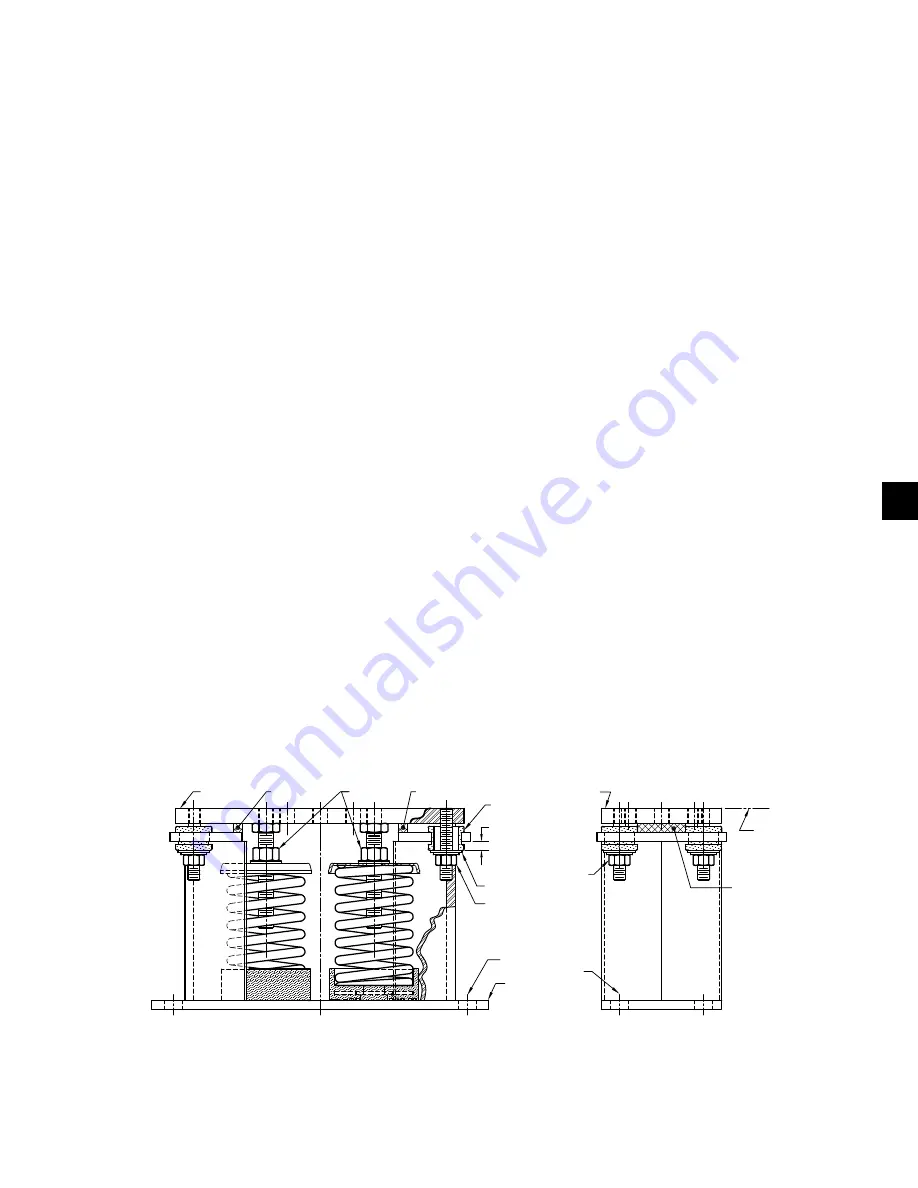
JOHNSON CONTROLS
91
SECTION 5 – TECHNICAL DATA
FORM 150.27-NM1
ISSUE DATE: 09/30/2015
55
WASHER
("F")
("B")
GROMMET
("G")
("A")
("C")
("F")
("E")
("E")
("E")
1/4 - 3/8 GAP
CL
CL
("C")
EQUIPMENT
("A")
7. THE ADJUSTMENT PROCESS CAN ONLY BEGIN AFTER THE EQUIPMENT OR MACHINE IS AT ITS
FULL OPERATING WEIGHT.
8. BACK OFF EACH OF THE (4) LIMIT STOP LOCK NUTS ("F") ON ISOLATORS 1/2".
9. ADJUST EACH ISOLATOR IN SEQUENCE BY TURNING SPRING ADJUSTING NUTS ("G") ONE FULL
CLOCKWISE TURN AT A TIME. REPEAT THIS PROCEDURE ON ALL ISOLATORS, ONE AT A TIME.
CHECK THE LIMIT STOP LOCK NUTS ("F") PERIODICALLY TO ENSURE THAT CLEARANCE
BETWEEN THE WASHER AND RUBBER GROMMET IS MAINTAINED. STOP ADJUSTMENT OF
ISOLATOR ONLY WHEN THE TOP PLATE ("A") HAS RISEN JUST ABOVE THE SHIM ("E").
10. REMOVE ALL SPACER SHIMS ("E").
11. FINE ADJUST ISOLATORS TO LEVEL EQUIPMENT.
12. ADJUST ALL LIMIT STOP LOCK NUTS ("F") PER ISOLATOR, MAINTAINING 1/4-TO 3/8-INCH GAP.
THE LIMIT STOP NUTS MUST BE KEPT AT THIS GAP TO ENSURE UNIFORM BOLT LOADING
DURING UPLIFT (AS THE CASE WHEN EQUIPMENT IS DRAINED).
13. INSTALLATION IS COMPLETE.
1. READ INSTRUCTIONS IN THEIR ENTIRETY BEFORE BEGINNING INSTALLATION.
2.ISOLATORS ARE SHIPPED FULLY ASSEMBLED AND ARE TO BE POSITIONED IN
ACCORDANCE WITH THE SUBMITTAL DRAWINGS OR AS OTHERWISE RECOMMENDED.
3.SET ISOLATORS ON FLOOR, HOUSEKEEPING PAD, OR SUB-BASE, ENSURING THAT
ALL ISOLATOR CENTERLINES MATCH THE EQUIPMENT MOUNTING HOLES. THE VMC
GROUP RECOMMENDS THAT THE ISOLATOR BASE PLATES ("B") BE INSTALLED ON A
LEVEL SURFACE. SHIM OR GROUT AS REQUIRED, LEVELING ALL ISOLATOR BASE
PLATES TO THE SAME ELEVATION (1/4-INCH MAXIMUM DIFFERENCE CAN BE
TOLERATED).
4.BOLT OR ANCHOR ALL ISOLATORS TO SUPPORTING STRUCTURE UTILIZING BASE
PLATE THRU HOLES ("C") OR WELD BASE PLATE TO SUPPORTING STRUCTURE WITH
3/8 FILLET WELD 2" LONG @ 4" ON CENTER AROUND ENTIRE BASE PLATE OR AS
ENGINEERED FOR SPECIFIC LOAD AND OR FIELD CONDITIONS.
5.ISOLATORS ARE SHIPPED TO THE JOB SITE WITH (2) REMOVABLE SPACER SHIMS
("E") BETWEEN THE TOP PLATE AND THE HOUSING. THESE SHIMS MUST BE IN PLACE
WHEN THE EQUIPMENT IS POSITIONED OVER THE ISOLATORS.
6.WITH ALL SHIMS ("E") IN PLACE, POSITION EQUIPMENT ON TOP OF PLATE ("A") OF
ISOLATOR. BOLT EQUIPMENT SECURELY TO TOP PLATE OF ISOLATOR USING A
MINIMUM OF (2) 5/8 UNC A325 GRADE 5 SAE BOLT OR WELD EQUIPMENT OR BRACKET
TO THE TOP PLATE ("A") OF ISOLATOR WITH A MINIMUM 3/8 FILLET WELDS 2" LONG
@ 3" O.C. FOR A MINIMUM TOTAL WELD OF 10". (ALL SIDES OF EQUIPMENT OR
BRACKET RESTING ON TOP PLATE ("A") MUST BE WELDED).
LD13763A
SEISMIC ISOLATOR INSTALLATION AND
ADJUSTMENT
1. Read instructions in their entirety before begin-
ning installation.
2. Isolators are shipped fully assembled and are to be
positioned in accordance with the submittal draw-
ings or as otherwise recommended.
3.
Set isolators on floor, housekeeping pad, or sub-
base, ensuring that all isolator centerlines match
the equipment mounting holes. The VMC group
recommends that the isolator base plates (“B”) be
installed on a level surface. Shim or grout as re-
quired, leveling all isolator base plates to the same
elevation (1/4-inch maximum difference can be
tolerated).
4. Bolt or anchor all isolators to supporting structure
utilizing base plate thru holes (“C”) or weld base
plate to supporting structure with 3/8 fillet weld
2" long @ 4" on center around entire base plate or
as engineered for specific load and or field condi
-
tions.
5. Isolators are shipped to the job site with (2) re-
movable spacer shims (“E”) between the top plate
and the housing. These shims must be in place
when the equipment is positioned over the isola-
tors.
6. With all shims (“E”) in place, position equipment
on top of plate (“A”) of isolator. Bolt equipment
securely to top plate of isolator using a minimum
of (2) 5/8 UNC A325 grade 5 SAE bolts or weld
equipment or bracket to the top plate (“A”) of iso-
lator with a minimum of 3/8 fillet welds 2" long @
3" on center for a minimum total weld of 10". (All
sides of equipment or bracket resting on top plate
(“A”) must be welded).
7. The adjustment process can only begin after the
equipment or machine is at its full operating
weight.
8. Back off each of the (4) limit stop lock nuts (“F”)
on isolators 1/2".
9. Adjust each isolator in sequence by turning spring
adjusting nuts (“G”) one full clockwise turn at a
time. Repeat this procedure on all isolators, one
at a time. Check the limit stop lock nuts (“F”)
periodically to ensure that clearance between the
washer and rubber grommet is maintained. Stop
adjustment of isolator only when the top plate
(“A”) has risen just above the shim (“E”).
10. Remove all spacer shims (“E”).
11. Fine adjust isolators to level equipment.
12. Adjust all limit stop lock nuts (“F”) per isolator,
maintaining a 1/4 to 3/8-inch gap. The limit stop
nuts must be kept at this gap to ensure uniform
bolt loading during uplift (as the case when equip-
ment is drained).
13. Installation is complete.