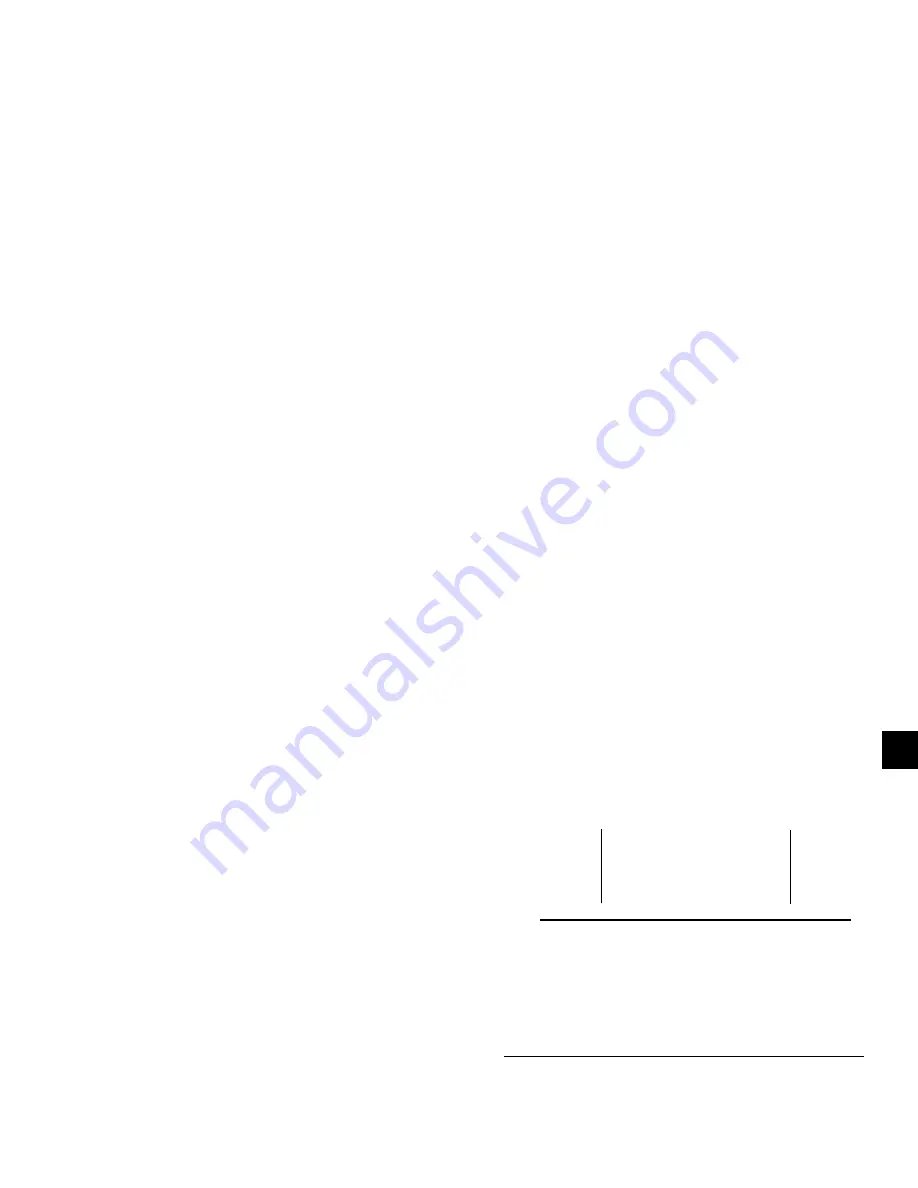
JOHNSON CONTROLS
129
FORM 150.27-NM1
ISSUE DATE: 09/30/2015
8
CAPACITY CONTROL
To initiate the start sequence of the chiller, all run per-
missive inputs must be satisfied (flow/remote start/stop
switch), and no chiller or system faults exist.
The first phase of the start sequence is initiated by the
Daily Schedule Start or any Remote Cycling Device. If
the unit is shut down on the Daily Schedule, the chilled
water pump microboard contacts (TB8 6-7) will close
to start the pump when the Daily Schedule start time
has been reached. Once flow has been established and
the flow switch closes, capacity control functions are
initiated, if the remote cycling contacts wired in series
with the flow switch are closed.
It should be noted that the chilled water pump con-
tacts (TB8 6-7) are not required to be used to cycle
the chilled water pump. However, in all cases the flow
switch must be closed to allow unit operation.
The control system will evaluate the need for cooling
by comparing the actual leaving or return chilled liq-
uid temperature to the desired setpoint, and regulate
the leaving or return chilled liquid temperature to meet
that desired setpoint.
SUCTION PRESSURE LIMIT CONTROLS
The anticipatory controls are intended to prevent the
unit from ever actually reaching a low-pressure cut-
out. Loading is prevented, if the suction pressure drops
below 1.15 x suction pressure cutout (15% below the
cutout). Loading may reoccur after suction pressure
rises above the unload point and a period of one min-
ute elapses. This control is only operable if the optional
suction pressure transducers are installed.
DISCHARGE PRESSURE LIMIT CONTROLS
The discharge pressure limit controls unload a system
before it reaches a safety limit due to high load or dirty
condenser coils. The microprocessor monitors dis-
charge pressure and unloads a system, if fully loaded,
by one compressor when discharge pressure exceeds
the programmed cutout minus 10 PSIG (0.69 barg).
Reloading will occur when the discharge pressure on
the affected system drops to 85% of the unload pres-
sure and 10 minutes have elapsed.
This control is only applicable if optional discharge
pressure transducers are installed.
LEAVING CHILLED LIQUID CONTROL
The setpoint, when programmed for Leaving Chilled
Liquid Control, is the temperature the unit will control
to within plus or minus the (control) cooling range. The
Setpoint High Limit is the Setpoint plus the cooling
range. The Setpoint Low Limit is the Setpoint minus
should be
utilized to aid in understanding the following descrip-
tion of Leaving Chilled Liquid Control.
If the leaving chilled liquid temperature is above the
Setpoint High Limit, the lead compressor on the lead
system will be energized along with the liquid line so-
lenoid. Upon energizing any compressor, the 60 sec-
ond anti-coincidence timer will be initiated to prevent
multiple compressors from turning ON.
If after 60 seconds of run-time the leaving chilled liq-
uid temperature is still above the Setpoint High Limit,
the next compressor in sequence will be energized.
Additional compressors will be energized at a rate of
once every 60 seconds if the chilled liquid temperature
remains above the Setpoint High Limit and the chilled
liquid temperature is dropping less than 3 °F/min. The
lag system will not be allowed to start a compressor
until the lead system has run for 5 minutes.
If the chilled liquid temperature falls below the Set-
point High Limit but is greater than the Setpoint Low
Limit, loading and unloading do not occur. This area of
control is called the control range.
If the chilled liquid temperature drops to between Set-
point Low Limit and 0.5 °F (.28 °C) below the Setpoint
Low Limit, unloading (a compressor turns off) occurs
at a rate of one every 30 seconds.
FIGURE 35 -
LEAVING WATER TEMPERATURE
CONTROL EXAMPLE
44.0 ºF
(6.7 ºC)
Low Limit
46.0 ºF
(7.8 ºC)
Setpoint
48.0 ºF
(8.9 ºC)
High Limit
Leaving Water Temp. Control - Compressor Staging
Setpoint = 46.0 ºF (7.8 ºC) Range = +/-2 ºF (1.1 ºC)
30 sec.
unloading
60 sec.
loading
Contol Range
(no compressor staging)
LWT
LD14404
SECTION 8 – UNIT OPERATION