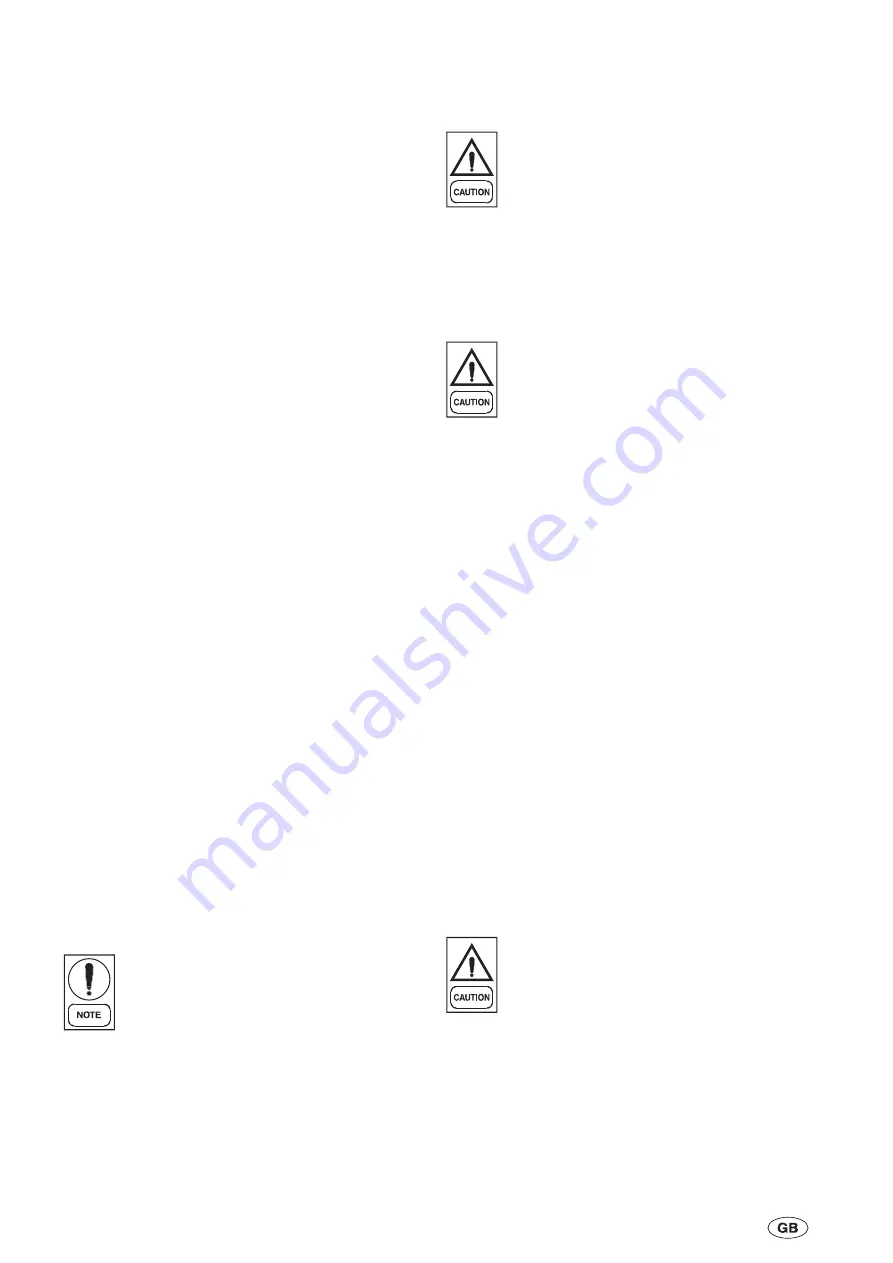
n
Pipework and fittings must be separately
supported to prevent any loading on the heat
e x c h a n g e r ( s ) . F l e x i b l e c o n n e c t i o n s a r e
r e c o m m e n d e d w h i c h w i l l a l s o m i n i m i s e
transmission of vibrations to the building. Flexible
connections must be used if the unit is mounted on
anti-vibration mounts as some movement of the
unit can be expected in normal operation.
n
Pipework and fittings immediately next to the heat
exchangers should be readily de-mountable to
enable cleaning prior to operation, and to facilitate
visual inspection of the exchanger nozzles.
n
Each heat exchanger must be protected by a 20
mesh strainer, available as an option, fitted as
close as possible to the liquid inlet connection, and
provided with a means of local isolation.
n
The heat exchanger(s) must not be exposed to
flushing velocities or debris released during
flushing. It is recommended that a suitably sized
by-pass and valve arrangement is installed to allow
flushing of the pipework system. The by-pass can
be used during maintenance to isolate the heat
exchanger without disrupting flow to other units. Do
not exceed heat exchanger design pressures
during water side pressure tests.
n
Thermometer and pressure gauge connections
should be provided on the inlet and outlet
connections of each heat exchanger.
n
Drain and air vent connections should be provided
at all low and high points in the pipework to permit
drainage of the system, and to vent any air in the
pipes.
n
Liquid systems at risk of freezing, due to low
ambient temperatures, should be protected using
insulation and heater tape and/or a suitable glycol
solution. The liquid pump(s) must also be used to
ensure liquid is circulated when the ambient
temperature approaches freezing point. Insulation
should also be installed around the heat exchanger
nozzles.
Heater tape of 21 watts per metre under the
insulation is recommended, supplied
independently and controlled by an ambient
temperature thermostat set to switch on at
3°C above the freezing temperature of the
liquid.
Any debris left in the water pipework between
the strainer and heat exchanger could cause
serious damage to the plates in the heat
exchanger and must be avoided. The
installer/user must also ensure that the quality
of the water in circulation is adequate, without
any dissolved gasses which can cause
oxidation of steel parts within the heat
exchanger(s).
4.4
Water Treatment
The unit performance given in the Design
Guide is based on a fouling factor of 0.044
m² °C/kW. Dirt, scale, grease and certain
types of water treatment will adversely affect
the heat exchanger surfaces and therefore
unit performance. Foreign matter in the water
system(s) can increase the heat exchanger
pressure drop, reducing the flow rate and
causing potential damage to the heat
exchanger plates.
Aerated, brackish or salt water is not recommended for
use in the water system(s). JCI recommend that a water
treatment specialist is consulted to determine that the
proposed water composition will not affect the
evaporator materials of stainless steel. The pH value of
the water flowing through the heat exchangers must be
kept between 7 and 8.5. The total installed sytem
including pumps, cooling coils, pipework, couplings and
chiller should be assesed with regards to correct water
treatment. Poor or incorrect water treatment can lead to
warranty being avoided.
Glycol Solutions
For unit operation with chilled liquid temperatures
leaving the cooler at below 5°C, glycol solutions should
be used to help prevent freezing. Section 9, gives
recommended solution strength with water, as a
percentage by weight, for the most common types of
glycol. It is important to check glycol concentration
regularly to ensure adequate concentration and avoid
possible freeze-up in the cooler.
When using glycol solutions, pressure drops
are higher than with water. Special care must
be taken not to exceed the maximum pressure
drop allowed.
4
-
2
035-21786-100 Rev. 1 (0909)
Summary of Contents for York YCRE 040
Page 2: ......
Page 49: ...9 3 035 21786 100 Rev 1 0909 Suction Pressure Evaporator Sub cooling Temperatures...
Page 54: ...9 7 Clearances and Foundations 9 8 035 21786 100 Rev 1 0909...
Page 55: ...9 8 Dimensions 9 9 035 21786 100 Rev 1 0909 Model YCSE 040...
Page 56: ...9 10 035 21786 100 Rev 1 0909 Model YCSE 050...
Page 57: ...9 11 035 21786 100 Rev 1 0909 Model YCSE 060...
Page 58: ...9 12 035 21786 100 Rev 1 0909 Model YCSE 080...
Page 59: ...9 13 035 21786 100 Rev 1 0909 Model YCSE 100...
Page 60: ...9 14 035 21786 100 Rev 1 0909 Model YCRE 040...
Page 61: ...9 15 035 21786 100 Rev 1 0909 Model YCRE 050...
Page 62: ...9 16 035 21786 100 Rev 1 0909 Model YCRE 060...
Page 63: ...9 17 035 21786 100 Rev 1 0909 Model YCRE 080...
Page 64: ...9 18 035 21786 100 Rev 1 0909 Model YCRE 100...
Page 66: ...This Page Intentionally Blank 10 2 035 21786 100 Rev 1 0909...