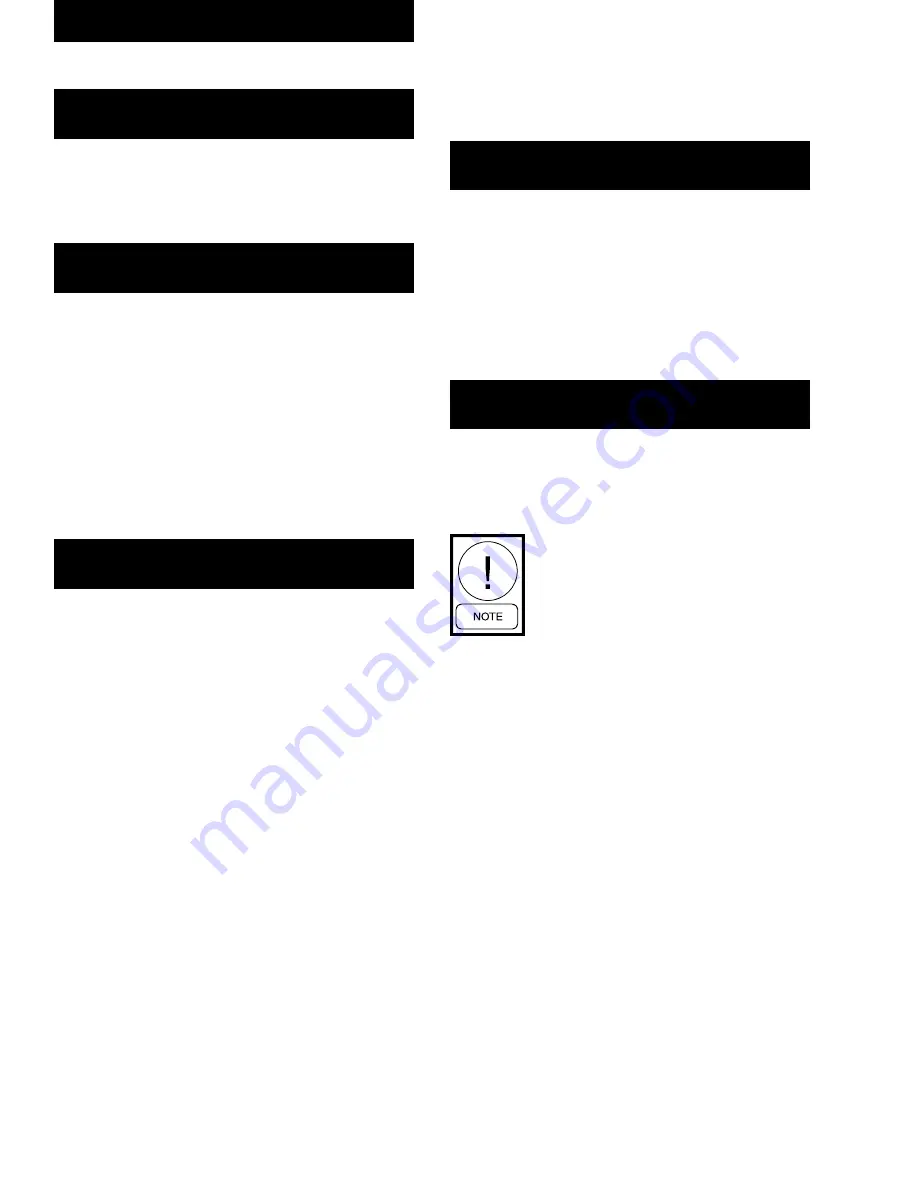
JOHNSON CONTROLS
66
FORM 150.62-NM9 (709)
INTRODUCTION
S Y S 1 L O A D L I M I T X X %
S Y S 2 L O A D L I M I T X X %
This message indicates that load limiting is in effect and
the percentage of the limiting in effect. This limiting
could be due to the load limit/pwm input, ISN or RCC
controller could be sending a load limit command.
M A N U A L
O V E R R I D E
If MANUAL OVERRIDE mode is selected, the STATUS
display will display this message. This will indicate that
the Daily Schedule is being ignored and the chiller will
start-up when chilled liquid temperature allows, Remote
Contacts, UNIT switch and SYSTEM switches permit-
ting. This is a priority message and cannot be overridden
by anti-recycle messages, fault messages, etc. when in
the STATUS display mode. Therefore, do not expect to
see any other STATUS messages when in the MANUAL
OVERRIDE mode. MANUAL OVERRIDE is to only be
used in emergencies or for servicing. Manual override
mode automatically disables itself after 30 minutes.
S Y S 1 P U M P I N G D O W N
S Y S 2 P U M P I N G D O W N
The PUMPING DOWN message indicates that a com-
pressor in the respective system is presently in the pro-
cess of pumping the system down. When pumpdown is
initiated on shutdown, the liquid line solenoid or EEV
will close and a compressor will continue to run. When
the suction pressure decreases to the suction pressure
cutout setpoint or runs for 180 seconds, whichever
comes first, the compressor will cycle off.
FAULT STATUS MESSAGES
Safeties are divided into two categories – system
safeties and unit safeties. System safeties are faults
that cause the individual system to be shut down. Unit
safeties are faults that cause all running compressors
to be shut down. Following are display messages and
explanations.
System Safeties:
System safeties are faults that cause individual systems
to be shut down if a safety threshold is exceeded for 3
seconds. They are auto reset faults in that the system
will be allowed to restart automatically after the fault
condition is no longer present. However, if 3 faults on
the same system occur within 90 minutes, that system
will be locked out on the last fault. This condition is then
a manual reset. The system switch (under OPTIONS
key) must be turned off and then back on to clear the
lockout fault.
S Y S 1 H I G H D S C H P R E S
S Y S 2 H I G H D S C H P R E S
The Discharge Pressure Cutout is a software cutout in
the microprocessor and is backed-up by a mechanical
high pressure cutout switch located in the refrigerant
circuit. It assures that the system pressure does not
exceed safe working limits. The system will shutdown
when the programmable cutout is exceeded and will be
allowed to restart when the discharge pressure falls 40
PSIG below the cutout.
Discharge transducers must be
installed for this function to operate.
S Y S 1 L O W S U C T P R E S S
S Y S 2 L O W S U C T P R E S S
The Suction Pressure Cutout is a software cutout that
helps protect the chiller from an evaporator freeze-up
should the system attempt to run with a low refrigerant
charge or a restriction in the refrigerant circuit.
Repeated starts after resetting a low suc
-
tion pressure fault will cause evaporator
freezeup. Whenever a system locks out
on this safety, immediate steps should
be taken to identify the cause.
At system start, the cutout is set to 10% of pro-
grammed value. During the next 3 minutes the cutout
point is ramped up to the programmed cutout point.
If at any time during this 3 minutes the suction pres-
sure falls below the ramped cutout point, the system
will stop.
This cutout is ignored for the first 30 seconds of sys-
tem run time to avoid nuisance shutdowns, especially
on units that utilize a low pressure switch in place of
the suction pressure transducer.
After the first 3 minutes, if the suction pressure falls
below the programmed cutout setting, a “transient
protection routine” is activated. This sets the cutout at
10% of the programmed value and ramps up the cutout
over the next 30 seconds. If at any time during this 30
seconds the suction pressure falls below the ramped
cutout, the system will stop. This transient protection
scheme only works if the suction pressure transducer
is installed. When using the mechanical LP switch, the
operating points of the LP switch are: opens at 23 PSIG
+/- 5 PSIG (1.59 barg +/- .34 barg), and closes at 35
PSIG +/- 5 PSIG (2.62 barg +/- .34 barg).
Summary of Contents for YORK YCAL0043E Series
Page 21: ...JOHNSON CONTROLS 21 FORM 150 62 NM9 709 THIS PAGE INTENTIONALLY LEFT BLANK ...
Page 102: ...JOHNSON CONTROLS 102 FORM 150 62 NM9 709 THIS PAGE INTENTIONALLY LEFT BLANK ...
Page 123: ...JOHNSON CONTROLS 123 FORM 150 62 NM9 709 THIS PAGE INTENTIONALLY LEFT BLANK ...
Page 125: ...JOHNSON CONTROLS 125 FORM 150 62 NM9 709 4 ...
Page 127: ...JOHNSON CONTROLS 127 FORM 150 62 NM9 709 4 ...
Page 129: ...JOHNSON CONTROLS 129 FORM 150 62 NM9 709 THIS PAGE INTENTIONALLY LEFT BLANK ...
Page 131: ...JOHNSON CONTROLS 131 FORM 150 62 NM9 709 4 LD08855 035 21627 000 REV B ...
Page 133: ...JOHNSON CONTROLS 133 FORM 150 62 NM9 709 4 035 19213 106 REV C ...
Page 135: ...JOHNSON CONTROLS 135 FORM 150 62 NM9 709 4 ...
Page 137: ...JOHNSON CONTROLS 137 FORM 150 62 NM9 709 4 ...
Page 139: ...JOHNSON CONTROLS 139 FORM 150 62 NM9 709 THIS PAGE INTENTIONALLY LEFT BLANK ...
Page 141: ...JOHNSON CONTROLS 141 FORM 150 62 NM9 709 4 035 21628 000 REV B ...
Page 143: ...JOHNSON CONTROLS 143 FORM 150 62 NM9 709 4 035 19213 105 REV C ...
Page 145: ...JOHNSON CONTROLS 145 FORM 150 62 NM9 709 4 ...
Page 147: ...JOHNSON CONTROLS 147 FORM 150 62 NM9 709 4 ...
Page 149: ...JOHNSON CONTROLS 149 FORM 150 62 NM9 709 4 ...
Page 151: ...JOHNSON CONTROLS 151 FORM 150 62 NM9 709 4 035 21625 000 REV B ...
Page 153: ...JOHNSON CONTROLS 153 FORM 150 62 NM9 709 4 035 19213 104 REV C ...
Page 155: ...JOHNSON CONTROLS 155 FORM 150 62 NM9 709 4 ...
Page 157: ...JOHNSON CONTROLS 157 FORM 150 62 NM9 709 4 ...
Page 159: ...JOHNSON CONTROLS 159 FORM 150 62 NM9 709 4 ...
Page 161: ...JOHNSON CONTROLS 161 FORM 150 62 NM9 709 4 035 21626 000 REV B ...
Page 163: ...JOHNSON CONTROLS 163 FORM 150 62 NM9 709 4 035 19213 103 REV C ...
Page 165: ...JOHNSON CONTROLS 165 FORM 150 62 NM9 709 4 ...
Page 167: ...JOHNSON CONTROLS 167 FORM 150 62 NM9 709 4 LD08833 ...
Page 169: ...JOHNSON CONTROLS 169 FORM 150 62 NM9 709 4 035 21610 104 REV ...
Page 171: ...JOHNSON CONTROLS 171 FORM 150 62 NM9 709 4 035 18150 102 REV D ...
Page 173: ...JOHNSON CONTROLS 173 FORM 150 62 NM9 709 4 ...
Page 175: ...JOHNSON CONTROLS 175 FORM 150 62 NM9 709 4 ...
Page 177: ...JOHNSON CONTROLS 177 FORM 150 62 NM9 709 4 035 21606 104 REV ...