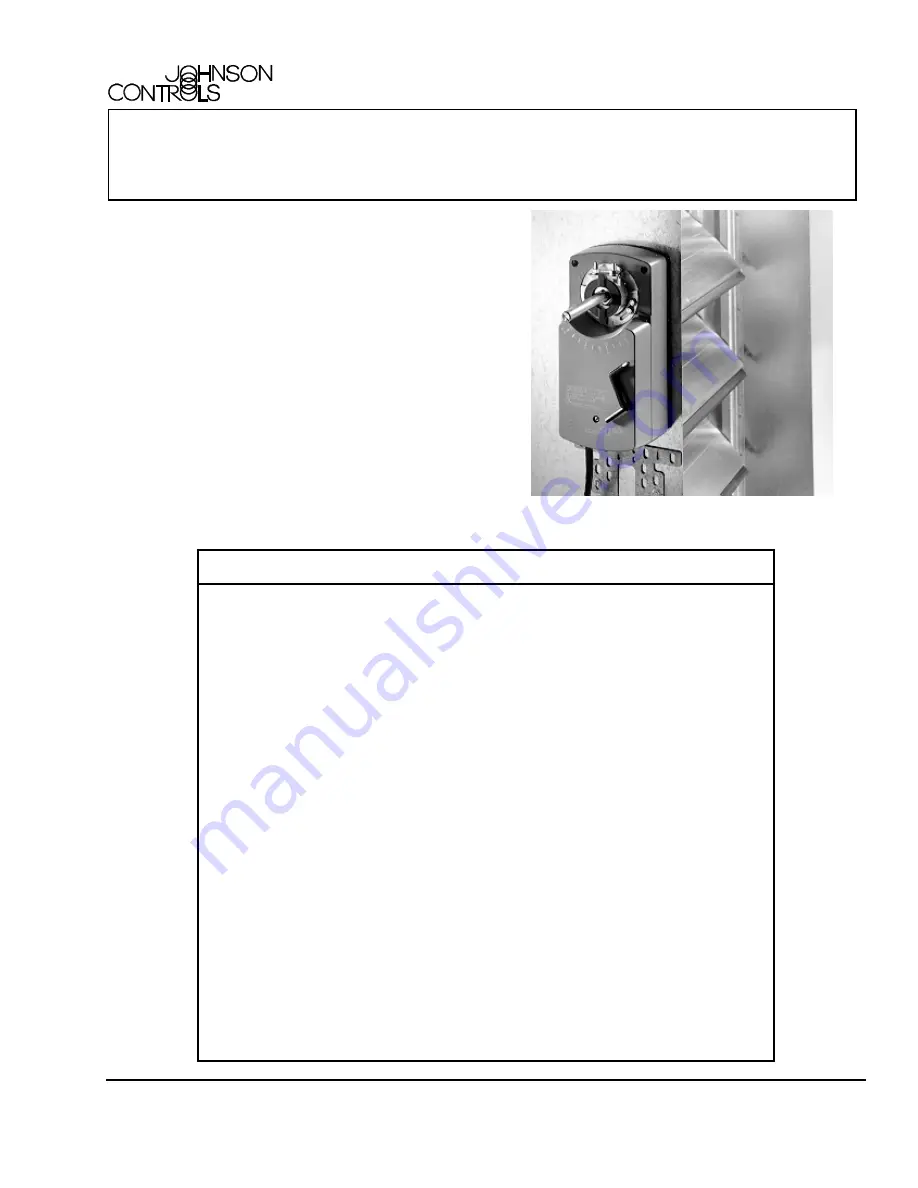
FANs 268.1, 1628.3, 977
Product/Technical Bulletin
M9200
Issue Date
0599
© 1999 Johnson Controls, Inc.
1
Part No. 34-636-461, Rev. D
www.johnsoncontrols.com
Code No. LIT-2681071
M9200 Series Electric Spring Return Actuator
The M9200 Series is a direct-mount, spring return line
of electric actuators that operates on 24 VAC or VDC
power and is available for use with on/off, floating,
proportional, or resistive controllers. These
bi-directional actuators do not require a damper
linkage, and are easily installed on a round shaft up to
3/4 in. (20 mm) diameter or a square shaft up to 5/8 in.
(16 mm). They can also be mounted to valves using
one of the M9000-5xx Valve Linkage Kits.
The M9200 models deliver 140 lb·in (16 N·m) of
torque. The angle of rotation is mechanically adjustable
from 30 to 90°. Integral auxiliary switches are available
to indicate end-stop position or to perform switching
functions at any angle within the selected rotation
range. Position feedback is available through switches,
a potentiometer, or a 0 (2) to 10 VDC signal.
Figure 1: M9200 Series Spring Return Actuator
Features and Benefits
❑
Bi-directional, Fail-safe
Spring Return
Allows selectable rotation/spring return direction
simplifying installation
❑
Four Control Input Types
Meets the needs of most applications
❑
Wide Range Resistive Input
Interfaces to 3-wire resistive controllers from
100 to 10,000 ohms
❑
Zero and Span Adjustment
on Proportional Models
Allows sequential operation of dampers from a
single input signal of 0 (2) to 10 VDC or
0 (4) to 20 mA
❑
On/Off Control
Provides simple, 2-wire control for low-cost
applications
❑
Electronic Stall Detection
Provides higher reliability by deactivating the
actuator when a stall condition is detected
❑
Output Position Feedback
Provides simple, closed-loop control with
accurate position sensing (standard on
proportional and resistive models, optional on
floating models)
❑
Calibration Output on
Proportional Models
Increases speed and accuracy of zero and
span adjustments over the entire range without
waiting for mechanical rotation
❑
Manual Override
Allows manual positioning when the actuator is not
powered; simplifies setup and field adjustments
❑
NPT Conduit Adaptor
(Included)
Meets electrical code requirements