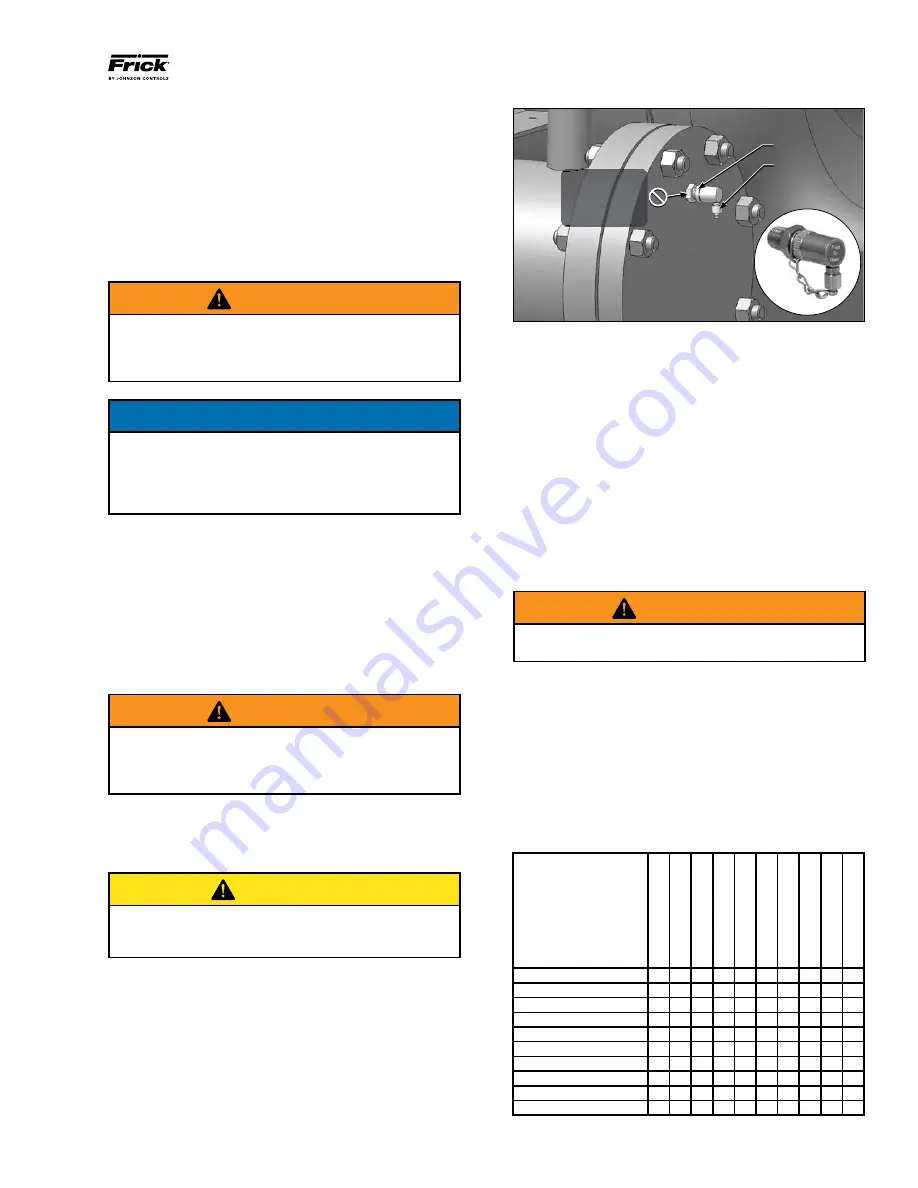
RWH ROTARY SCREW COMPRESSOR UNITS
MAINTENANCE
070.620-IOM (DEC 12)
Page 31
Locknut
Locknut
Valve Cap
& Spout
Valve Cap
& Spout
DO NOT
UNTHREAD
VALVE!
Figure 32
OPERATING LOG
The use of an operating log as included in this manual (see
Table of Contents) permits thorough analysis of the operation
of a refrigeration system by those responsible for its mainte
nance and servicing. Continual recording of gauge pressures,
temperatures, and other pertinent information, enables the
observer and serviceman to be constantly familiar with the
operation of the system and to recognize immediately any
deviations from normal operating conditions. It is recom
mended that readings be taken at least every four hours.
MOTOR BEARINGS
Follow the motor manufacturer’s maintenance recommenda
tions for lubrication. See Figure 33.
WARNING
Make sure the motor bearings are properly lubricated
before start-up as required by the motor manuf ac turer.
GREASE COMPATIBILITY
If it becomes necessary to mix greases, be careful not to
combine different oil bases or thickeners. DO NOT mix a
mineral oilbase grease with a synthetic oilbase grease.
Also, a grease with a lithium thickener should not be mixed
with one containing a sodium thickener. The table illustrates
the compatibility of various types of grease based on results
by National Lubricating Grease Institute (NLGI). The chart indi
cates a great variance in compaibility with the greases tested.
NLGI Grease Compatibility Chart
B = Borderline
C = Compatible
I = Incompatible
Aluminum Comple
x
Barium
Calcium
Calcium 12
h
ydr
oxy
Calcium Comple
x*
Cla
y
Lithium
Lithium 12
h
ydr
oxy
Lithium Comple
x
Polyur
ea
Aluminum Complex
–
I
I
C
I
I
I
I
C
I
Barium
I
–
I
C
I
I
I
I
I
I
Calcium
I
I
–
C
I
C
C
B
C
I
Calcium 12hydroxy
C
C
C
–
B
C
C
C
C
I
Calcium Complex
I
I
I
B
–
I
I
I
C
C
Clay
I
I
C
C
I
–
I
I
I
I
Lithium
I
I
C
C
I
I
–
C
C
I
Lithium 12hydroxy
I
I
B
C
I
I
C
–
C
I
Lithium Complex
C
I
C
C
C
I
C
C
–
I
Polyurea*
I
I
I
I
C
I
I
I
I
–
* Standard
4.
Vibration readings can be influenced by other equip ment
operating in the vicinity or connected to the same piping as
the unit.
OIL QUALITY AND ANALYSIS
High quality refrigeration oil is necessary to ensure compres
sor longevity and reliability. Oil quality will rapidly deteriorate
in refrig eration systems containing moisture and air or other
contaminants. In order to ensure the quality of the refrigera
tion oil in the com pressor unit.
WARNING
DO NOT MIX OILS of different brands, manufacturers, or
types. Mixing of oils may cause excessive oil foaming,
nuisance oil level cutouts, oil pressure loss, gas or oil
leakage and catastrophic compressor failure.
NOTICE
The Frick
®
oil charge shipped with the unit is the best
suited lubricant for the conditions specified at the time
of purchase. If there is any doubt due to the refrigerant,
operating pressures, or temperatures, refer to Frick
®
Oil
publication 160.802-SPC for guidance.
1. Only use Frick
®
oil filter elements or warranty claim
may be denied.
2.
Participate in a regular, periodic oil analysis program to
maintain oil and system integrity. Oil Analysis Kit part number:
333Q0001853.
3.
Oil samples for analysis should be taken after the oil filter.
A 1/4" purge valve is provided in the oil filter canister head.
OIL SAMPLING PROCEDURE
WARNING
Exercise extreme caution in the vicinity of operating
equipment. Skin contact with lube oil or inhalation of
vapors can cause serious injury or death, consider gloves
and eye protection.
Sample hot, active fluid while the equipment is operating.
Sample after 30 minutes of compressor operation.
1.
Unthread the oil sampling valve cap and locknut (Figure 32).
CAUTION
DO NOT UNTHREAD THE VALVE FROM THE FILTER
HOUSING OR PIPING OR UNCONTROLLED RELEASE OF
OIL WILL RESULT.
2.
Unthread the bottle cap and carefully position under the
oil sampling valve spout. Place the spout inside the bottle.
3.
Push the oil sampling valve to open and release to close
(spring actuated, see Figure 32). Fill the bottle ¾ full.
4.
Retighten bottle cap, sampling valve cap and locknut.
Please note that the locknut prevents accidental release of
oil.
5.
Record all necessary sample data and identification on
forms and labels and send promptly to the lab for results.