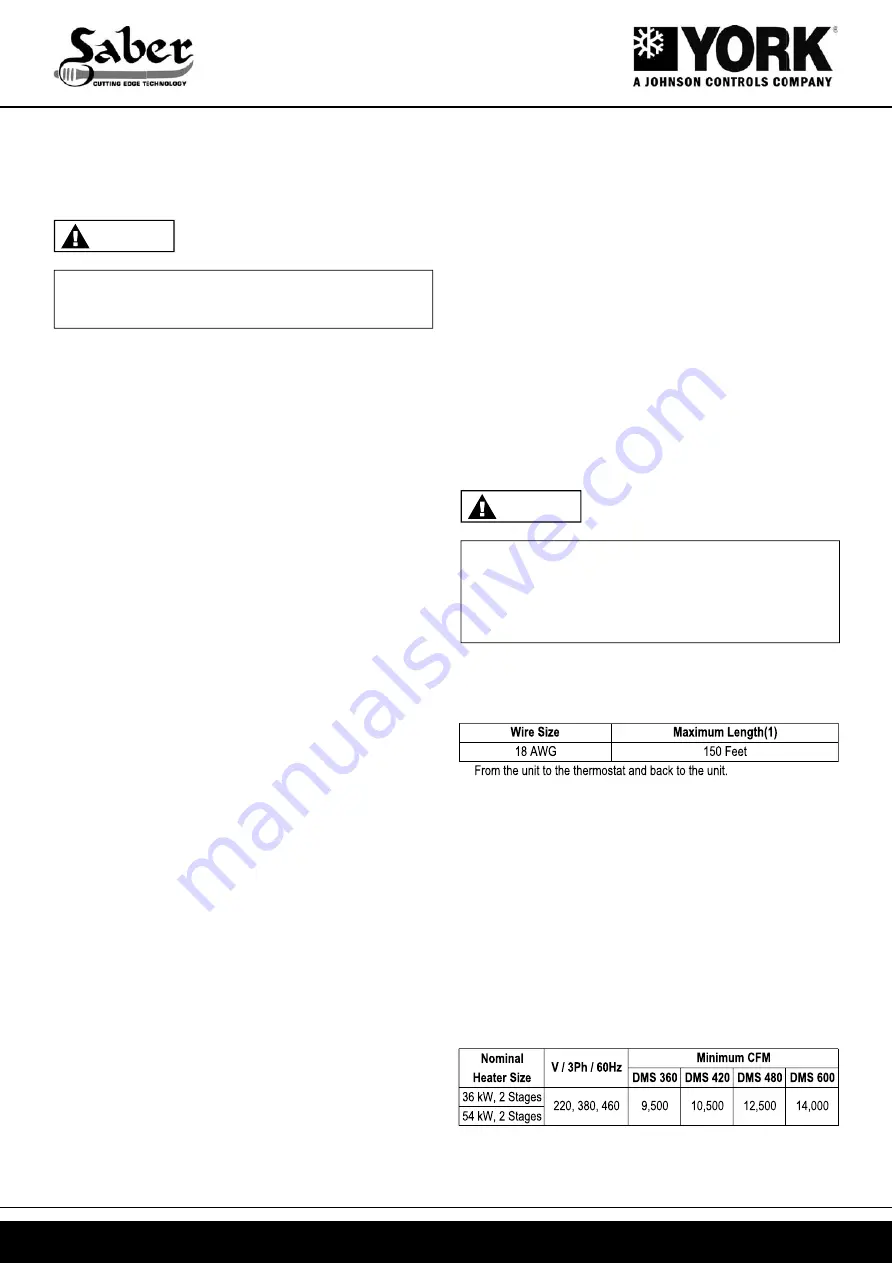
Installation, Operation and Maintenance Manual : 036-1011(0806)
Page 7
CAUTION
DO NOT LOOSEN COMPRESSOR MOUNTING BOLTS.
REMOVE COMPRESSOR SHIPPING BRACKETS BEFORE
START-UP.
FILTERS
Two inch filters can be supplied with each unit. Filters must
always be installed ahead of the evaporator coil and must be
kept clean or replaced with same size and type. Dirty filters
will reduce the capacity of the unit and will result in frosted
coils or safety shutdown. Minimum filter area and required
sizes are shown in Product Data Table 4.
SERVICE ACCESS
The following removable panels provide access to all
serviceable components :
• Compressor
compartment
•
Electric Heat compartment
• Blower
compartment
•
Main control box
• Filter
compartment
Refer to the Dimensions and Clearances Figure 7 for
location of these access panels.
THERMOSTAT
4 Stage Cooling
The room thermostat should be located on an inside wall
approximately 56 inches above the floor where it will not be
subject to drafts, sun exposure or heat from electrical
fixtures or appliances. Follow manufacturers instructions
enclosed with thermostat for general installation procedure.
A minimum of seven color coded insulated wires (#18 AWG)
should be used to connect thermostat to unit.
POWER AND CONTROL WIRING
Field wiring to the unit must conform to provisions of the
National Electrical Code and/or local ordinances. The unit
must be electrically grounded in accordance with NEC
and/or local codes.
Voltage tolerances, which must be maintained at the
compressor terminals, during starting and running
conditions, are indicated on the unit Rating Plate and the
Unit Application Data table.
A fused disconnect switch should be field provided based on
COMPRESSORS
Units are shipped with factory adjusted compressor
mountings and ready for operation.
the tabulated rating, with a short circuit capacity of 10K or
more, for the unit. The switch must be separate from all other
circuits. Wire entry at knockout openings require conduit
fittings to comply with local codes. Refer to the Dimensions
and Clearances Figure 7 for installation location.
If any of the wire supplied with the unit must be replaced,
replacement wire must be of the type shown on the wiring
diagram and the same minimum gauge as the replaced wire.
Electrical line must be sized properly to carry the load. Use
copper conductors only. Each unit must be wired with a
separate branch circuit fed directly from the meter panel and
properly fused.
Emergency stop button should be field installed as per wiring
diagram. The activator should be red in colour with a yellow
outline background, and should be easily accessible. The
device should be self latching type and contacts must be of
positive opening operation, certified to EN60947 - 5 - 1.
CAUTION
WHEN CONNECTING ELECTRICAL POWER AND CONTROL
WIRING TO THE UNIT, WATERPROOF TYPE CONNECTORS
MUST BE USED SO THAT WATER OR MOISTURE CANNOT BE
DRAWN INTO THE UNIT DURING NORMAL OPERATION. THE
ABOVE WATERPROOFING CONDITIONS WILL ALSO APPLY
WHEN INSTALLING A FIELD SUPPLIED DISCONNECT SWITCH.
Refer to Typical Wiring Diagram, Figure 7 and to the
appropriate unit wiring diagram for control circuit and power
wiring information.
OPTIONAL ELECTRIC HEAT
The factory installed heaters are wired for single point power
supply. Power supply need only be brought into the single
point terminal block and thermostat wiring to the low voltage
terminal strip located in the upper portion of the unit control
box.
These heaters are located within the supply air chamber.
Refer to Figure 8 for access panel location. Fuses are
supplied by the factory. Refer to Table 3 for minimum CFM
limitations and to Table 5 for electrical data.
TABLE 2 : CONTROL WIRE SIZES
TABLE 3 : MINIMUM CFM LIMITATION