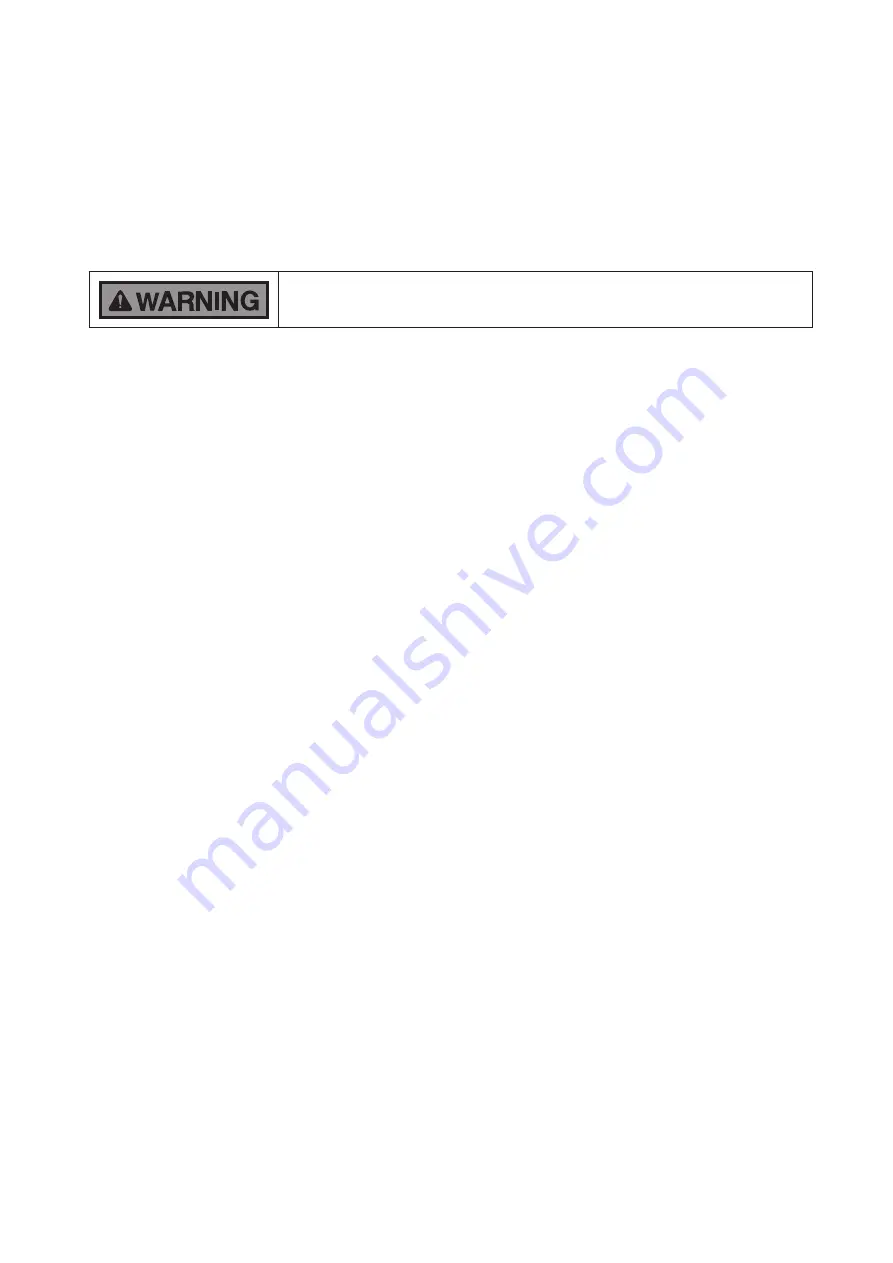
4
P5417050-rev.1
●
Clean up the site when finished, remembering to check that no metal scraps or bits of wiring have
been left inside the unit being installed.
After installation work for the system has been completed, explain the “Safety Precautions,” the proper use
and maintenance of this unit to the customer according to the information in all manuals that came with the
system. All manuals and warranty information must be given to the user or left near the indoor unit.
Refrigerant Precautions
To reduce the risk of serious injury or death, the following refrigerant
precautions must be followed.
●
As originally manufactured, this unit contains refrigerant installed by Johnson Controls. Johnson
Controls uses only refrigerants that have been approved for use in the unit’s intended home country
or market. Johnson Controls' distributors similarly are only authorized to provide refrigerants that
have been approved for use in the countries or markets they serve. The refrigerant used in this unit
is identified on the unit’s faceplate and/or in the associated manuals. Any additions of refrigerant into
this unit must comply with the country’s requirements with regard to refrigerant use and should be
obtained from Johnson Controls' distributors. Use of any non-approved refrigerant substitutes will void
the warranty and will increase the potential risk of injury or death.
●
If installed in a small room, take measures to prevent the refrigerant from exceeding the maximum
allowable concentration in the event that refrigerant gases should escape. The installation should
meet the requirements in ASHRAE Standards 15 and 34. If refrigerant gas has leaked during the
installation work, ventilate the room immediately.
●
Check the design pressure for this product is 601 psi (4.15MPa). The pressure of the refrigerant
R410A is 1.4 times higher than that of the refrigerant R22. Therefore, the refrigerant piping for
R410A shall be thicker than that for R22. Make sure to use the specified refrigerant piping. If not, the
refrigerant piping may rupture due to an excessive refrigerant pressure. Besides, pay attention to
the piping thickness when using copper refrigerant piping. The thickness of copper refrigerant piping
differs depending on its material.
●
The refrigerant R410A is adopted. The refrigerant oil tends to be affected by foreign matters such
as moisture, oxide film, (or fat). Perform the installation work with care to prevent moisture, dust, or
different refrigerant from entering the refrigerant cycle. Foreign matter can be introduced into the cycle
from such parts as expansion valve and the operation may be unavailable.
●
To avoid the possibility of different refrigerant or refrigerant oil being introduced into the cycle, the
sizes of the charging connections have been changed from R407C type and R22 type. It is necessary
to prepare the following tools listed in Section 3 before performing the installation work. Use
refrigerant pipes and joints that are approved for use with R410A.
●
Before installation is complete, make sure that the refrigerant leak test has been performed. If
refrigerant gases escape into the air, turn OFF the main switch, extinguish any open flames and
contact your service contractor. Refrigerant (fluorocarbon) for this unit is odorless. If the refrigerant
should leak and come into contact with open flames, toxic gas could be generated. Also, because the
fluorocarbons are heavier than air, they settle to the floor, which could cause asphyxiation.
●
When installing the unit, and connecting refrigerant piping, keep all piping runs as short as possible,
and make sure to securely connect the refrigerant piping before the compressor starts operating. If
the refrigerant piping is not connected, and the compressor activates with the stop valve opened, the
refrigerant system is subjected to extremely high pressure, which can cause an explosion or fire.
●
Tighten the flare nut with a torque wrench in the specified manner. Do not apply excessive force to the
flare nut when tightening. If you do, the flare nut can crack and refrigerant leakage may occur.