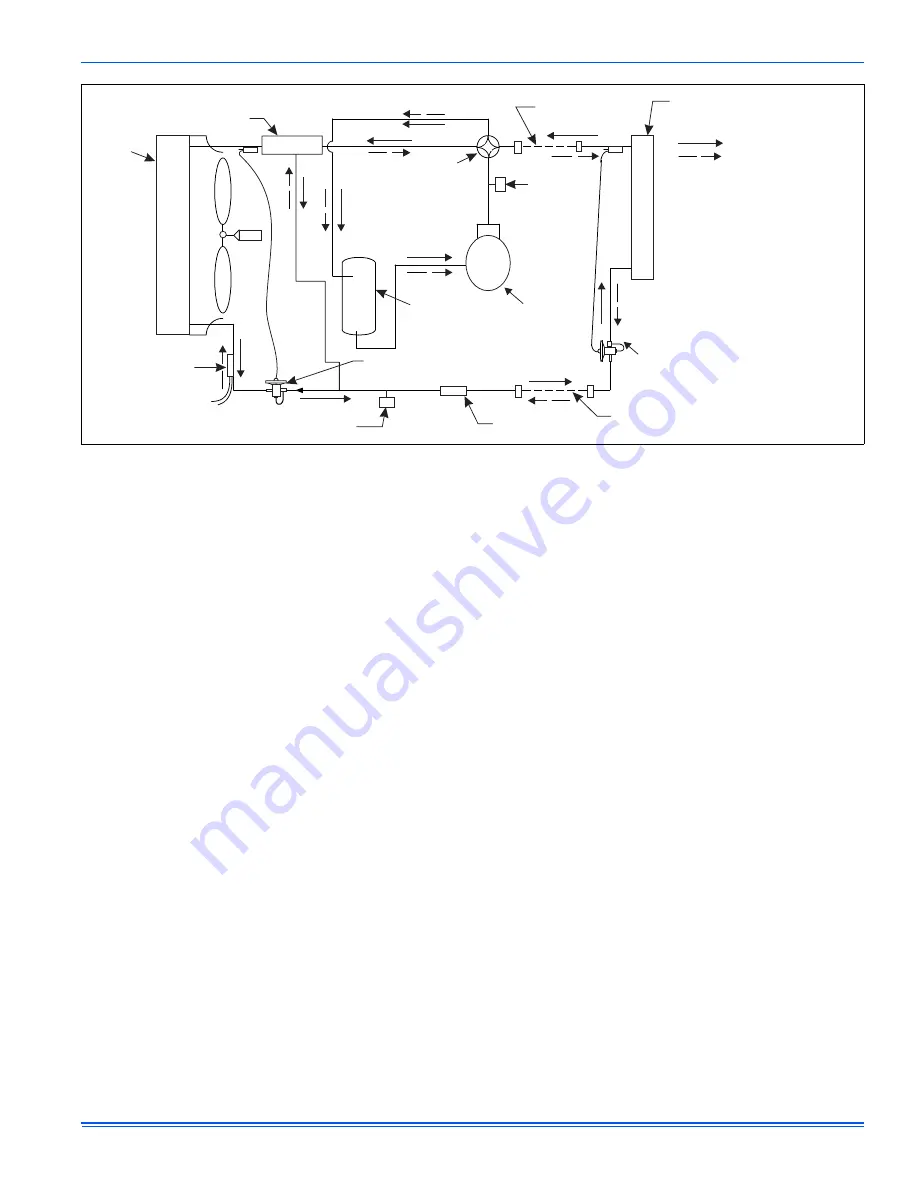
689103-BIM-B-1012
Johnson Controls Unitary Products
9
SECTION VI: INSTRUCTING THE OWNER
Assist owner with processing warranty cards and/or online registration.
Review Owners Guide and provide a copy to the owner and guidance
on proper operation and maintenance. Instruct the owner or the opera-
tor how to start, stop and adjust temperature setting.
When applicable, instruct the owner that the compressor is equipped
with a crankcase heater to prevent the migration of refrigerant to the
compressor during the “OFF” cycle. The heater is energized only when
the unit is not running. If the main switch is disconnected for long peri-
ods of shut down, do not attempt to start the unit until 8 hours after the
switch has been connected. This will allow sufficient time for all liquid
refrigerant to be driven out of the compressor.
The installer should also instruct the owner on proper operation and
maintenance of all other system components.
MAINTENANCE
1. Dirt should not be allowed to accumulate on the outdoor coils or
other parts in the air circuit. Clean as often as necessary to keep the
unit clean. Use a brush, vacuum cleaner attachment, or other suit-
able means.
2. The outdoor fan motor is permanently lubricated and does not
require periodic oiling.
3. If the coil needs to be cleaned, it should be washed with Calgon
Coilclean (mix one part Coilclean to seven parts water). Allow solu-
tion to remain on coil for 30 minutes before rinsing with clean water.
Solution should not be permitted to come in contact with painted
surfaces.
4. Refer to the furnace or air handler instructions for filter and blower
motor maintenance.
5. The indoor coil and drain pan should be inspected and cleaned reg-
ularly to prevent odors and assure proper drainage.
FIGURE 11:
Heat Pump Flow Diagram
CHARGE COMPENSATOR
(Empty in cooling / full in heating)
(Not included in all Units)
FIELD
CONNECTED LINE
INDOOR COIL
OUTDOOR
COIL
4-WAY
REVERSING
VALVE
FILTER DRYER
(Solid core)
SUCTION
ACCUMULATOR
LIQUID
SENSOR
COMPRESSOR
FIELD CONNECTED LINE
SHOWN IN COOLING POSITION.
COOLING CYCLE FLOW
HEATING CYCLE FLOW
BI-FLOW
TXV/CHECK
VALVE (Cooling) **
** NOTE: The indoor coil is shipped
with an orifice. The orifice must be
replaced with a TXV Kit.
BI-FLOW TXV/CHECK
VALVE OR ORIFICE (Heating)
LOW PRESSURE SWITCH
HIGH
PRESSURE
SWITCH