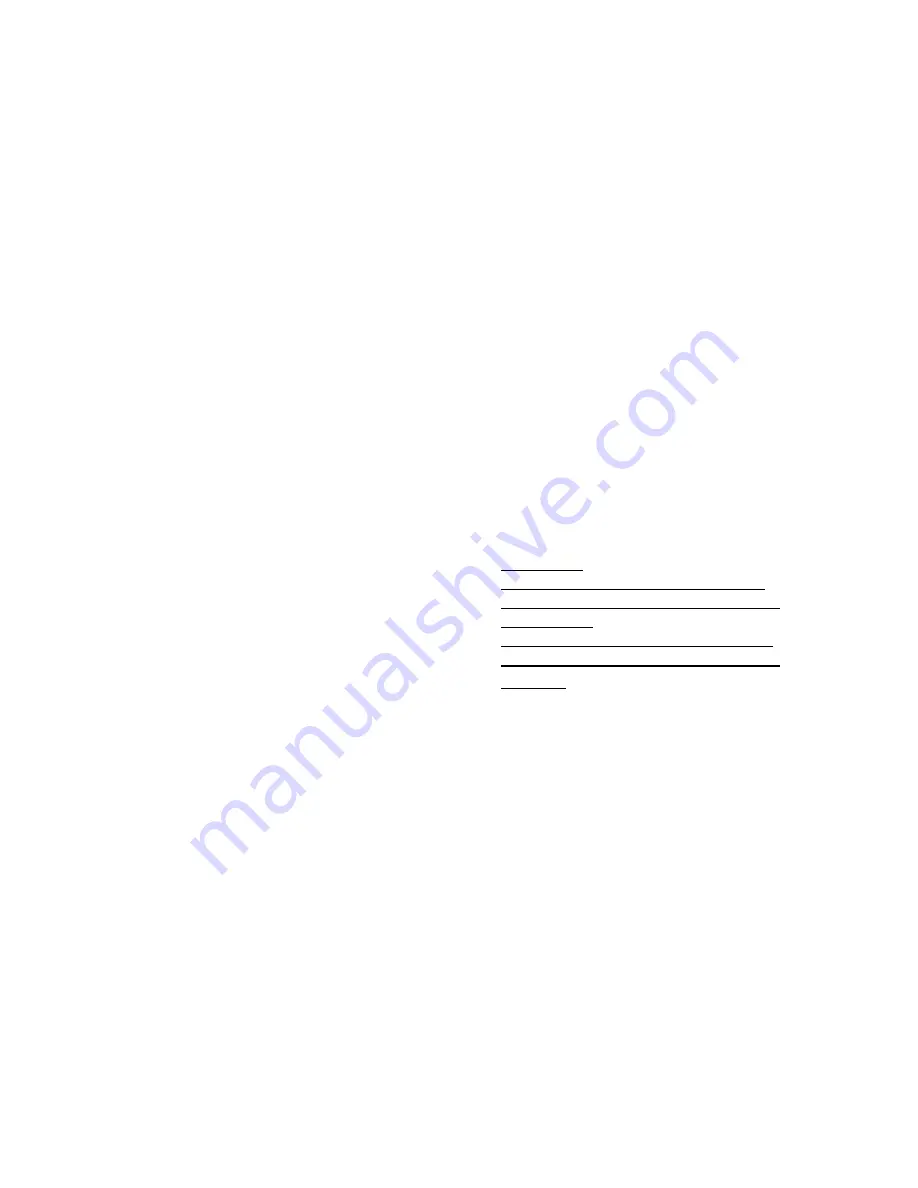
15
2.1.3 Gas connection
The gas supply to this appliance must
be installed in accordance with BS 6891
(1988) and British Gas Publications UP1
and UP2.
Fit the 1/2” gas supply cock supplied
with this unit immediately before the gas
control. No heat or soldered joints
should be applied in the vicinity of the
gas control, as they could cause
damage to the control. All connections
and joints should be tested for gas
soundness with a suitable leak detector
(do not use a naked flame).
N.B. When operating this unit on LPG a
suitable gas supply cock should be
used.
2.1.4 Flue system
The water heater should be fitted with a
flue system connected to the draught
diverter. The flue pipe should rise for at
least 50 cm. vertically before the
inclusion of any bends. If a horizontal
run of flue is required this should be
kept to the minimum lenght possible and
incorporate a rise of 6 cm. per metre of
run. A split clip or flange should be
provided in the flue close to the draught
diverter for ease of servicing.
All flue materials should be corrosion
resident i.e. stainless steel or
galvanised and must include a tested
and apprved terminal to BS 5440 part 1.
If the flue passes through any
combustible marerial measures must be
taken to protect against the possibility of
fire.
All flues must terminate in free air space
approx. 1,5 metres from any vertical
surface of structure i.e. chimney
stacks, roof parapets, etc. If an existing
chimney or flue is to be used this should
be swept clean and be free of debris
before an approved liner is installed and
connected to the water heater.
2.1.5 Draught diverter
The draught diverter, supplied
separately in the delivery crate,
MUST
be fitted to the top of the heater in an
unmodified condition before connecting
the flue system.
The sensor of the combustion products
discharge safety device is pre-fitted to
the draught diverter so care should be
taken not to damage the capillary and
thermostat. With the sensor facing
forward, place the draught diverter
over the flue tube and ensure the three
legs engage with the slots in the top
casing.
To complete the installation of the
combustion products discharge safety
device, remove the two screws from
the top casing, position the bracket with
the pre-assembled thermostat over the
holes and re-apply screws. Complete
the electrical circuit by connecting the
two pin plug to its appropriate socket on
the top casing. Should the safety device
operate, the heater will shut down and
only restart when the sensor
temperature has dropped sufficiently
for the button on the thermostat to be
reset.
Important
The combustion products discharge
safety device should never be put out
of operation.
Re-entry of flue gases to the building
could be harmful and cause poisoning
or death.
2.1.6 Electrical connection
All electrical connections must be
carried out in accordance with IEE
regulations by an accredited electrical
installation company. The appliance
must be connected to the mains by
means of a permanent electrical
connection. A main switch must be
fitted in the phase between the perma-
nent connection and the water heater.
The feeder cable must have cores of at
least 3 * 1.0 mm
2
The connecting clamps
for the electricity supply are indicated
by the symbol for earth Á, N for neutral
and L for live. Always check with a vol-
tage tester if the live and the neutral
have been connected correctly in the
electricity supply. The electricity supply
must comply with the requirements
below: