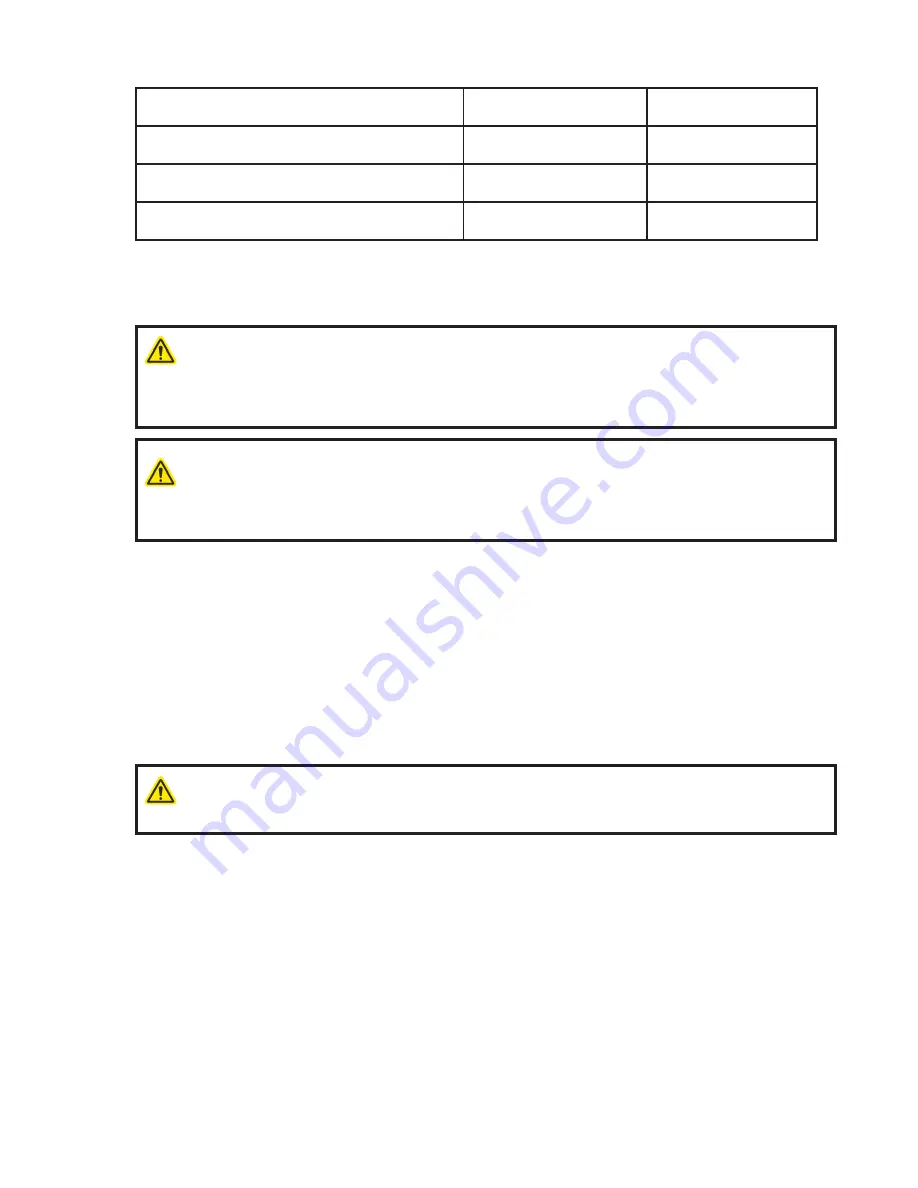
Page 6 of 21
TriPod User Manual
AA0277.indd REV 04
14
Performance Specifications
Vertical Payload*:
10 kg
23 lbs
Umbilical Length**:
30 m
100 ft
Max Controller Cable Length**:
30 m
100 ft
Travel Speed:
0 - 18 m/min.
0 - 60 ft/min.
*attachments and umbilical are considered part of payload
**contact Jireh Industries for custom cable lengths
15
Power Requirements
WARNING!
A reliable power source must be used for powering the crawler.
Connections must be secured to prevent accidental disconnection. Power failure may cause the
crawler to freewheel down if operating in a vertical orientation. Portable generator usage is not
recommended unless accompanied by the use of an uninterruptible power supply system.
WARNING!
Proper grounding of the power supply is important for safe operation. If
a generator is being used to supply power to the system (not recommended), the generator must be
properly grounded (see the generator manual).
Power Requirements: 85-264VAC, 45-65Hz, 5 Amps
NOTE: The TriPod power supply automatically adjusts to the supplied voltage.
16
Operating Environment
The TriPod is designed for use in an industrial environment that is:
• dry or damp (the crawler its self is rated to IP67);
• between -20°C and 50°C;
•
free of explosion or fire hazards.
17
Unintended Use
DANGER!
FALLING OBJECT HAZARD. Using the TriPod outside of its intended use is
dangerous. Severe injury or death could result. Do NOT use the TriPod as listed below!
The TriPod is NOT intended for:
• operation on surfaces that are not clean. (e.g. excess rust, scale, ferrous debris, ice, frost);
• lifting / lowering objects or people (I.e. using the crawler as a crane / elevator);
• driving into obstructions;
• operating in ambient temperatures below -20°C or above 50°C;
In addition to the above points, for operating at a height greater than 2m (6’), the crawler is not intended
for:
• operation without a proper tether system;
• operating up-side-down;
• operating while oriented such that the umbilical strain relief points upwards, or at worst, horizontal
(front of the TriPod is lower than the umbilical connection).