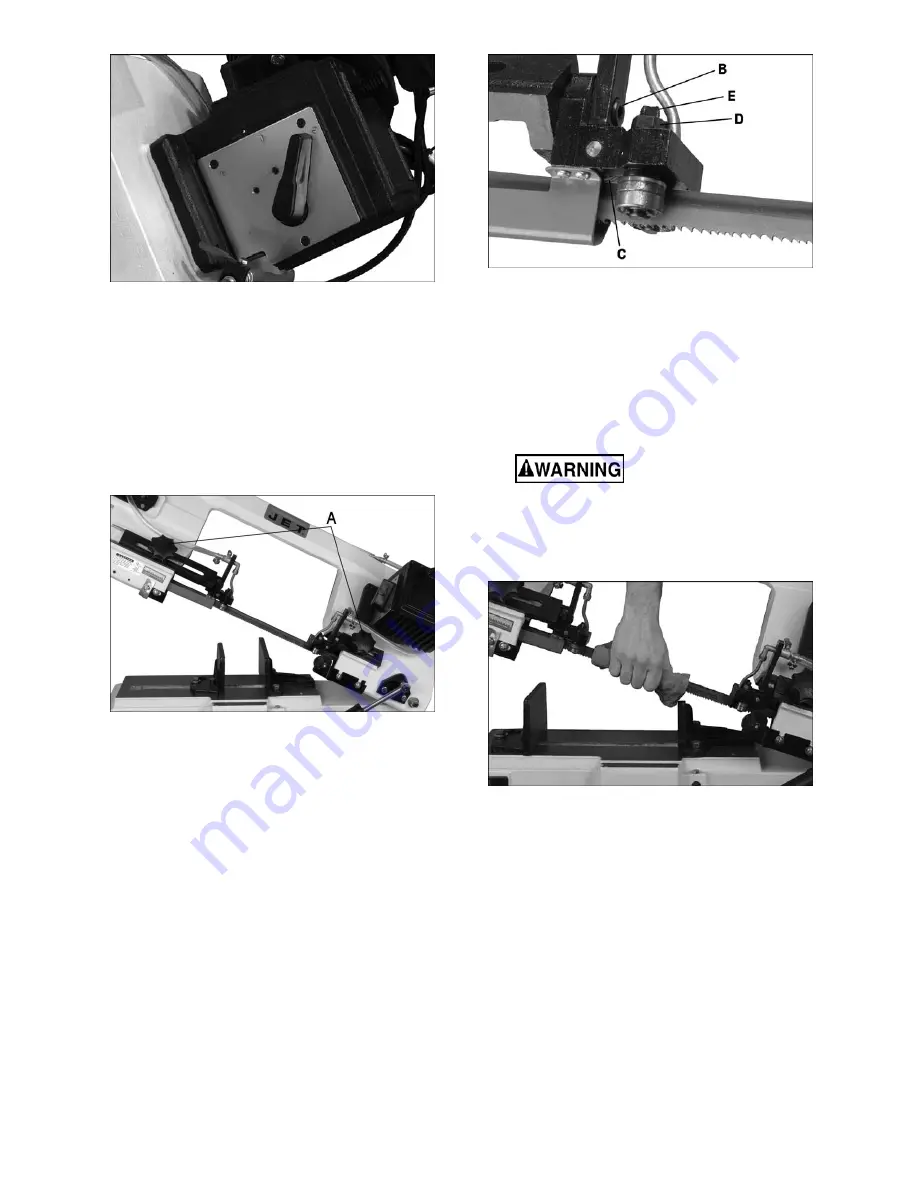
17
Figure 23
9.11
Blade guide adjustment
1. Loosen knobs (A, Figure 24).
2. Slide guide assemblies as close to
workpiece as possible without interfering
with cut. This will prevent excessive blade
exposure, and deflection of blade during
cutting.
3. Retighten
knobs.
Figure 24
The guide bearings come pre-adjusted from the
factory, but should be inspected frequently and
adjustments made as needed.
For most efficient operation and maximum
accuracy, provide 0.001” clearance between the
blade and the guide bearings. The bearings will
still turn freely with this clearance. If the
clearance is incorrect, the blade may track off
the drive wheel.
1. Disconnect machine from power source.
2. Raise bow to vertical and secure in place by
turning off hydraulic cylinder.
3. Loosen socket head cap screw (B, Figure
25) and adjust guide assembly until back
roller bearing (C) is slightly contacting back
edge of blade.
Figure 25
4. Loosen nut (D) and rotate eccentric shaft (E)
to adjust side bearing until bearing just
touches side of blade. Do not pinch the
blade.
5. Blade should still move up and down freely
when grasped as in Figure 26. Make sure
blade teeth do not interfere with guide
bearings.
Make sure power is
disconnected and hands are protected
before handling blade.
6. Tighten nut (D).
7. Repeat for other blade guide assembly.
Figure 26
9.12
Chip brush
The chip brush (B, Figure 19) must be properly
adjusted and maintained in working condition;
otherwise damage to blade can occur. Adjust
the brush so that its bristles overlap the blade.
Replace brush if it becomes worn or damaged.