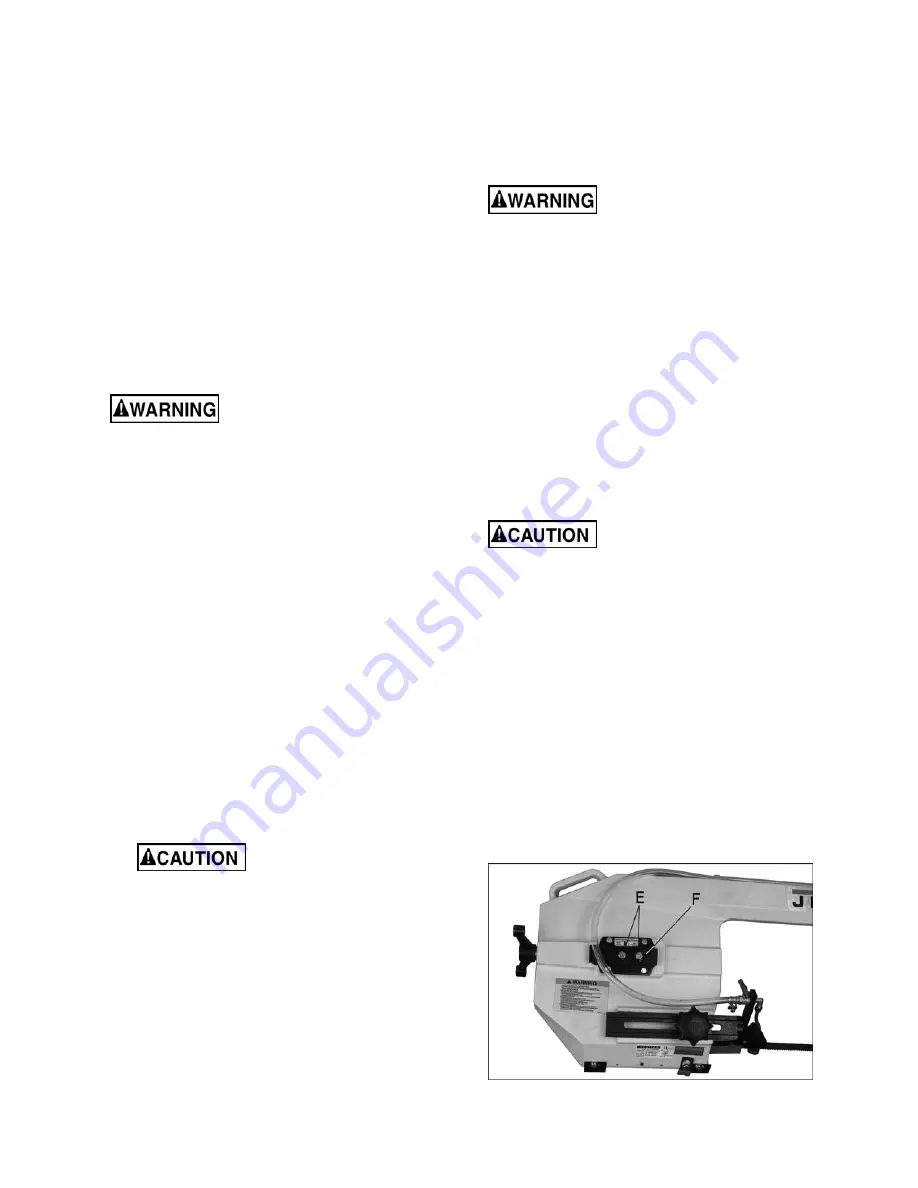
15
direction as shown on the blade direction
label on saw. (If teeth still point in wrong
direction despite mounting blade properly,
the blade has been turned inside-out. Twist
blade right side-out and reinstall.)
9. Position blade around wheels, making sure
it rests near the flange on both wheels.
10. Tension blade using handle. Do not over-
tension. See
section 9.7,
Blade tension
.
11. Close back cover and secure with knobs.
12. Install red blade guard, and brush assembly.
13. Connect machine to power source.
14. Run machine to verify that blade is tracking
properly. See
section 9.8,
Blade tracking
.
9.7
Blade tension
Disconnect machine from
power source, and use caution when
working with sharp blade.
Blade tension is vital to achieving proper results
from the band saw. For shipping purposes, the
blade may not be at full tension – verify tension
before operating.
Proper blade tension is 1550 to 1760 kg/cm
2
(22000-25000 lb/in
2
) as measured on a blade
tension gauge (not provided).
To set tension without the use of a tension
gauge:
1. Disconnect machine from power source.
2. Install blade between wheels and between
bearings on blade guides.
3. Lightly tension blade to remove any sag by
turning handle (C, Figure 20) slightly
clockwise.
4. Turn tension handle (C, Figure 20) 1-3/4 to
two revolutions clockwise. This is equivalent
to 800 kg (1764 lb) of blade tension.
Do not overtighten blade;
this may cause it to stretch or warp.
5. Close covers, connect to power source, and
run saw for 2 to 3 minutes to allow blade to
seat properly.
6. Disconnect machine from power source.
Open cover and loosen blade until it just
begins to sag.
7. Tighten blade until it straightens between
blade wheels and all sag is eliminated.
8. Tighten blade by turning handle (C, Figure
20) two full revolutions.
TIP:
Slacken blade tension when finished with
operations, to prolong blade life. Make note of
indicator position on tension label (D, Figure 20)
for quickly returning tension to its previous
setting.
9.8
Blade tracking
Tracking the blade requires
that the band saw be operating while the
back cover is removed. This adjustment
should be performed by qualified persons
only.
Blade tracking has been tested at the factory.
Adjustment is rarely required when the blade is
used properly and if the blade is correctly
welded. If a tracking problem occurs, first
inspect blade condition, then adjust tracking as
follows:
1. Raise bow to vertical position and secure by
turning off hydraulic cylinder valve.
2. The blade should be properly tensioned.
Refer to
section 9.7 Blade tension.
3. Open back cover.
While performing the
following steps, keep the blade from rubbing
excessively on wheel flange. Excess rubbing
will damage wheel and/or blade.
4. Start saw and observe blade movement.
Blade should run next to, but not tightly
against, wheel flange.
5. If blade will not track in position, loosen
screws (E, Figure 21), but do not remove.
6. Turn set screw (F, Figure 21) counter-
clockwise so that blade starts to move away
from the flange; then immediately turn set
screw in the other direction so that blade
stops, then moves slowly back toward
flange. NOTE: This adjustment is sensitive;
do it gradually and in small increments
allowing blade to respond to the changes.
Figure 21