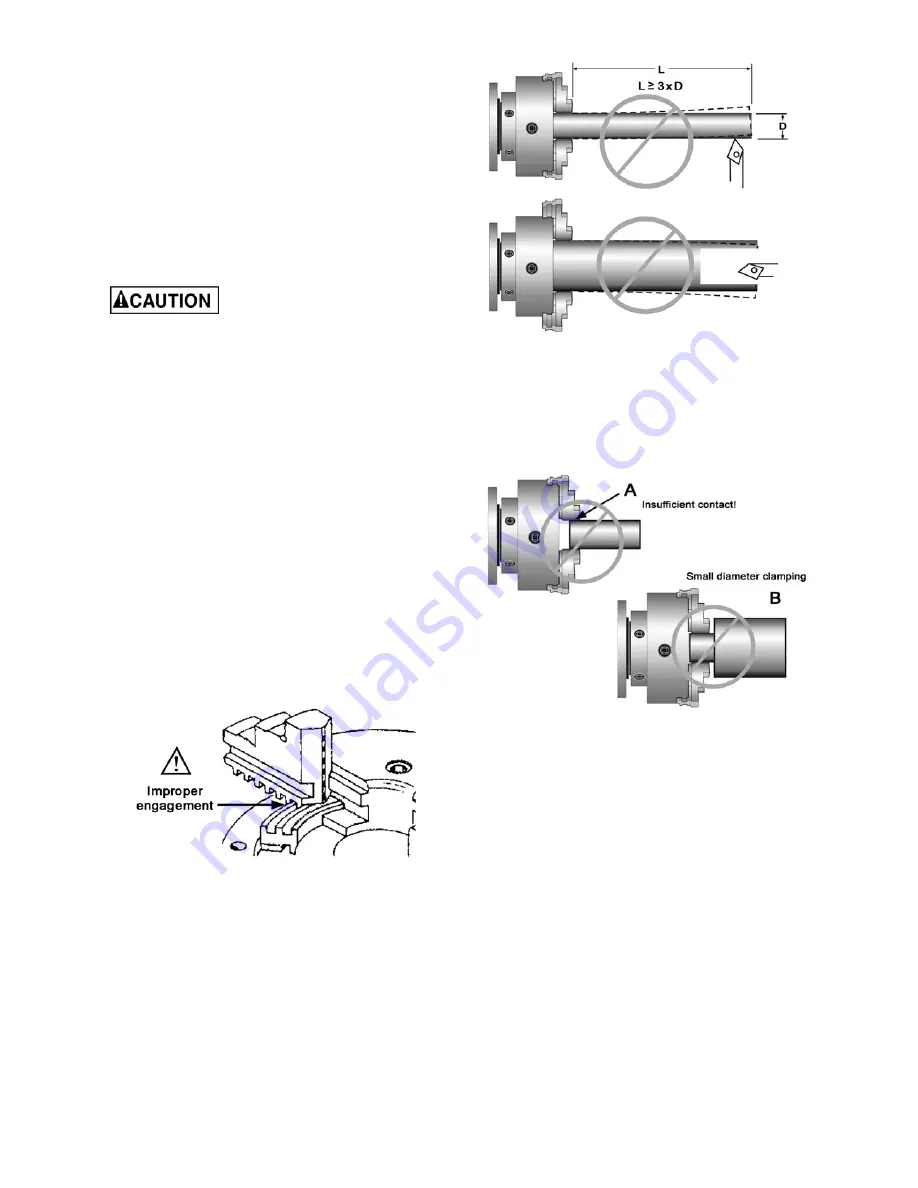
18
12.0
Operation
The operator should consult shop manuals such as
“Machinery’s Handbook” for cutting speeds and
feeds appropriate to specific workpieces. Correct
feed depends upon material to be cut, cutting
operation, tool type, chucking rigidity, depth of cut,
and desired surface quality.
IMPORTANT:
Allow a break-in period for the new
lathe so that gears and bearings can adapt; do not
run the lathe above 560 RPM for the first six hours
of operation.
The following points must be
observed when operating the lathe:
•
Never turn any handles or levers when spindle
is at high speed.
•
Change spindle speed only after spindle stops.
•
Change feed rate only when spindle is at low
speed or is stopped.
•
Never exceed maximum speed limitation of the
work holding device.
•
Before starting spindle, check that each handle
or lever is at correct position to ensure normal
engagement of gears. The spindle direction
control lever should be at neutral position.
•
If the brake becomes ineffective, turn off
machine and adjust brake immediately.
•
When operating spindle direction control lever,
always turn it to correct position; never use
“pre-position” for cutting at a reduced speed.
•
Jaw teeth and scroll must be fully engaged, to
prevent the jaws from breaking and being
thrown from chuck (see Figure 24).
Figure 24 – Insufficient jaw tooth engagement
•
Avoid long workpiece extensions, as parts may
bend or fly off (see figure 25). Use rests or the
tailstock for support.
Figure 25 – Improper setups
•
Avoid short clamping contact (Figure 26, A) or
clamping on a minor part diameter (Figure 26,
B). Face-locate the workpiece for added
support.
Figure 26 – Improper setups
12.1
Tool setup
The cutting angle is correct when the cutting edge
is in line with the center axis of workpiece. Use the
point of the tailstock center as a gauge and shims
under the tool to obtain correct center height.
Use a minimum of two clamping screws to secure
each tool.
Summary of Contents for GH-1640ZK
Page 26: ...26 This page intentionally left blank ...
Page 27: ...27 This page intentionally left blank ...
Page 32: ...4 3 0 Stand Assembly Exploded View ...
Page 34: ...6 4 0 Brake Assembly Exploded View ...
Page 36: ...8 5 0 Bed Assembly Exploded View ...
Page 39: ...11 6 0 Headstock Assembly I Exploded View ...
Page 41: ...13 7 0 Headstock Assembly II Exploded View ...
Page 44: ...16 8 0 Headstock Assembly III Exploded View ...
Page 46: ...18 9 0 Headstock Assembly IV Exploded View ...
Page 48: ...20 10 0 Change Gear Box Assembly I Exploded View ...
Page 50: ...22 11 0 Change Gear Box Assembly II Exploded View ...
Page 52: ...24 12 0 Quick Change Gear Box I Exploded View ...
Page 55: ...27 13 0 Quick Change Gear Box II Exploded View ...
Page 57: ...29 14 0 Quick Change Gear Box III Exploded View ...
Page 59: ...31 15 0 Apron Assembly I Exploded View ...
Page 62: ...34 16 0 Apron Assembly II Exploded View ...
Page 65: ...37 17 0 Apron Assembly III Threading Dial Exploded View ...
Page 67: ...39 18 0 Saddle and Cross Slide Assembly Exploded View ...
Page 70: ...42 19 0 Tool Post and Compound Rest Exploded View ...
Page 72: ...44 20 0 Tailstock Assembly I Exploded View ...
Page 75: ...47 22 0 Steady Rest Assembly Exploded View ...
Page 78: ...50 24 0 Coolant and Work Light Assembly Exploded View ...
Page 83: ...55 28 1 Electrical Diagram GH 1640ZK Lathe 3PH 230V ...