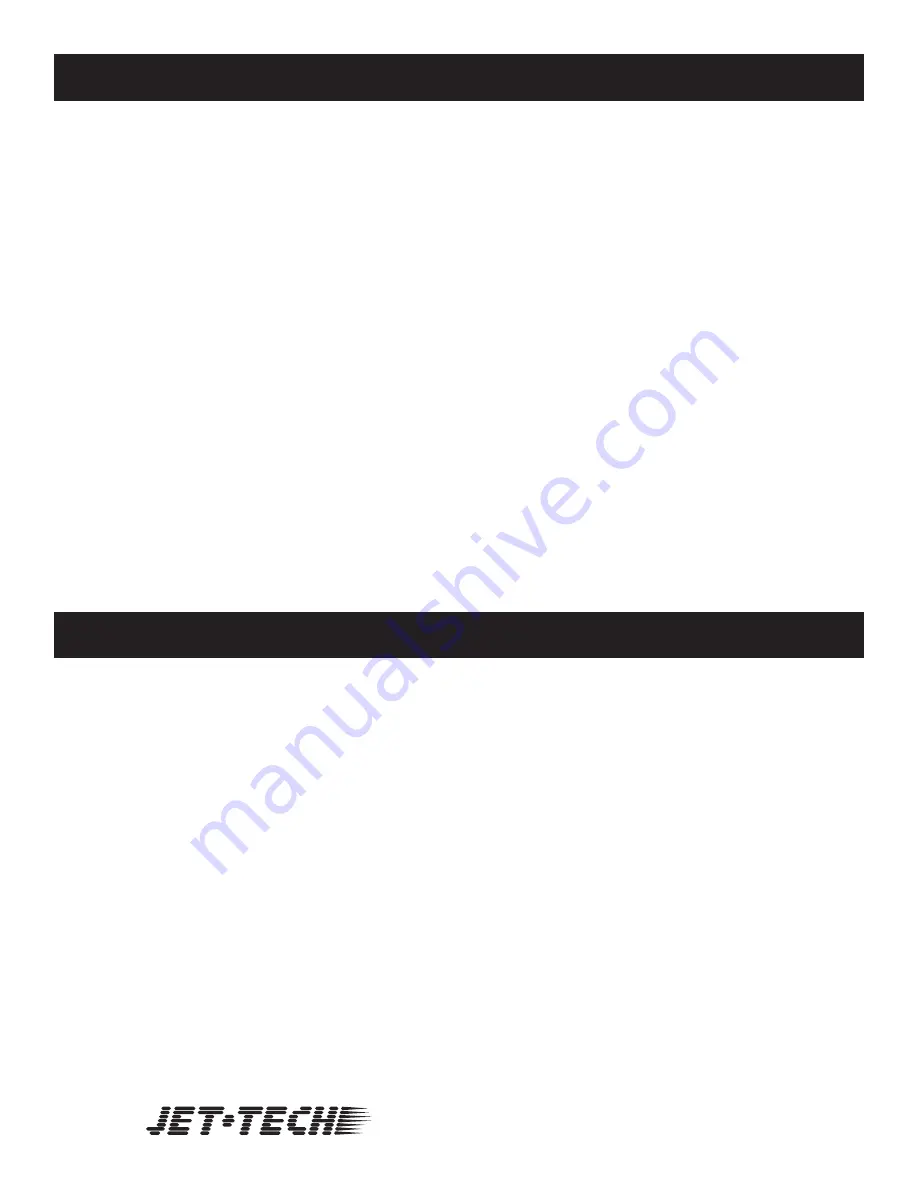
11
MVP Group Corp - 5659 Royalmount Ave., Montreal, QC, Canada H4P 2P9
Tel: 514.737.9701 / 888.275.4538 - Fax: 514.342.3854 / 877.453.8832
[email protected] - www.mvpgroupcorp.com
1. NEVER, NEVER
wash ash trays in the glasswasher. Since ashes are smaller than the opening in the Pump Inlet Screens, ashes can
adhere to glasses. Also, with ashes recirculating in the wash water, the cleaning effectiveness of the detergent is greatly reduced.
The final result of washing ash trays is dirty glasses.
2. For best results, run glasswasher full of glassware. This keeps the water and detergent consumption to a minimum and helps prevent glass-
ware from tipping over.
3. Water spotting can occur when glassware is placed on a flat surface after washing, thus preventing air to assist the drying process. Make
sure the proper shelf liner or drying surface is used.
4. Clearance below the top cover of the glasswasher allows for a maximum glass height of ten (10) inches. Keep this in mind when
ordering beer pitchers and wine carafes.
5. Glasses which have been frequently washed by hand may have deposits of invisible “film”. Although initially appearing clean, these
glasses may show unsightly signs of “dirt” after passing through the glasswasher. This unsightly condition will exist until the film is
removed with frequent passes through the glasswasher, or it may be necessary to use a de-liming agent to clean glassware.
6. Do not place wet glasses into glass chillers or frosters. Allow glasses to dry and sanitizer odors to dissipate first.
7. Changing detergents may require readjustment of the Detergent Pump to maintain .30% detergent concentration. A greater volume of
low strength detergent is required to maintain the proper level.
8. Only Jet-Tech replacement parts should be used. Components from other suppliers may result in machine malfunctions.
Please consult your Jet-Tech service agent if service or technical assistance is required. The factory is also available to answer any
operational questions.
The XG-37 glasswasher has chemical pumps that automatically dispense chemicals into the machine. The detergent and sanitizer
chemicals are supplied by a chemical vendor. Since the type of chemicals and the condition of water varies by region, the chemical
pumps are not pre-set at the factory.
The chemical pumps must be adjusted at start-up to achieve the proper titration levels or the
machine may not produce good wash results.
Typically, the chemical vendor is responsible for adjusting the chemical pumps.
Since detergent and sanitizer chemicals play an important role in the performance of a glasswasher, understanding how the chemical
pumps work and how to maintain them is very important. Reviewing the following information will help ensure the proper operation
of your glasswasher and its chemical pumps:
1. CAUTION: Always cycle the machine after using the prime switches to rinse out the wash/rinse tank. Undiluted chemicals will
damage stainless steel.
2. The chemical feed lines must be properly placed inside the appropriate chemical container. Damaged chemical lines will spill
chemicals on the machine and floor and create poor wash results.
3. Every glasswasher requires chemical pump adjustment and titrating by a chemical vendor. Poor wash results will occur if the
chemicals are not in proper concentration (see page 5, Step 6, for proper concentration levels).
4. Glasswasher chemicals are highly caustic and will cause severe burns when they contact human skin. These same caustic chemi-
cals will also corrode stainless steel and destroy machine components. A glasswasher should be checked regularly for chemical
leaks. Any leaks should be corrected immediately.
5. All of the chemical tubing on a glasswasher should be inspected regularly and replaced at least once per year. The highly caustic
chemicals cause the chemical tubing to get brittle, and since leaking chemicals destroy glasswasher components, it is good preven-
tative maintenance to replace chemical tubing often. The various tubing includes the lower tubing assembly or main chemical feed
line, the pump squeeze tube (especially susceptible to damage), and the upper tubing assembly from the pump to the glasswasher
tank.
6. Chemical vendors that deliver chemicals to your establishment are typically responsible for adjusting the chemical levels in
your glasswasher. They are also helpful for assisting you with chemical tubing inspection and replacement. Nothing removes
your responsibility for proper maintenance, but the chemical vendor will help.
I
mportant
I
nFormatIon
a
bout
c
hemIcals
t
Ips
For
t
rouble
-F
ree
o
peratIon
Summary of Contents for XG-37
Page 5: ...Operation Manual XG 37 Glasswasher 2012 Jet Tech Rev 13 01 12...
Page 21: ...Parts Directory XG 37 GlassWasher...
Page 24: ...5 InterIor and exterIor ComPonents 3 7 8 2 9 11 1 10 12 17 13 14 15 18 16...
Page 26: ...eleCtrICal ComPonents 7 3 4 10 11 5 7 8 6 9 1 2 19 16 20 14 21 18 17 15 28 27 26 12 13 24...
Page 28: ...reCIrCulatInG PumP and related Parts 9 6 7 1 2 3 8 4 5 9 10...
Page 30: ...PerIstaltIC PumP ChemICal tubInG and related Parts 11 10 12 11 1 8 7 9 13 3 16 2 15 14...
Page 32: ...drIve assembly ComPonents 13 1 10 7 8 2 3 6 11 4 9 10 8 5...