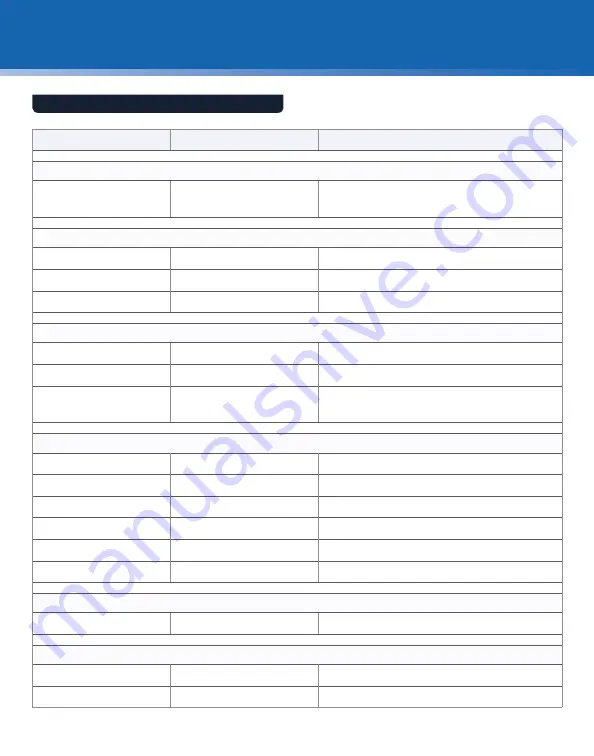
22
User ManUal
troUBleshootInG
Symptom
Potential Cause
Test / Remedy
A – unit will not turn ON
No power to unit
• Make sure power cord is connected.
• Make sure power switch is in the correct position.
B – unit is ON, but will not fire
Power light is blinking
Run button
on handset is depressed
• Turn OFF power, release
run button,
and turn unit ON
Power light is solid RED
Safety is not disengaged
• Apply pressure to cleaning nozzle to disable safety
Low Solvent light ON
Solvent tank is empty
• Refill the tank with cleaning solvent
C – unit fires but no solvent is dispensed
Solvent refill cap may be open
• Close solvent refill cap
Line may need to be PRIMED
• Prime the system
(see page 16)
Cleaning tip damaged or plugged
• Place the tip in electrostatic wash; if problem persists,
replace tip
D – unit operates but doesn't clean properly
No cleaning tip or wrong tip installed • Verify correct cleaning tip and install
Tip not fully inserted into bulkhead
• Make sure the tip comes to a stop inside mating adapter
No solvent spray
• See Symptom C above for remedy
Vacuum flow restricted
• Check exhaust port or filter for obstruction
Air flow restricted
• Check air filters
Nozzle damaged
• Check nozzle inside tip for damage and replace if necessary
E – Service light is ON
System at service interval
• Replace air filters
(see page 21)
F – No image on LCD
No power to LCD
• Verify the unit and LCD power switches are ON
No probe connected to unit
• Install probe to probe input
TROuBLEShOOTINg TIPS