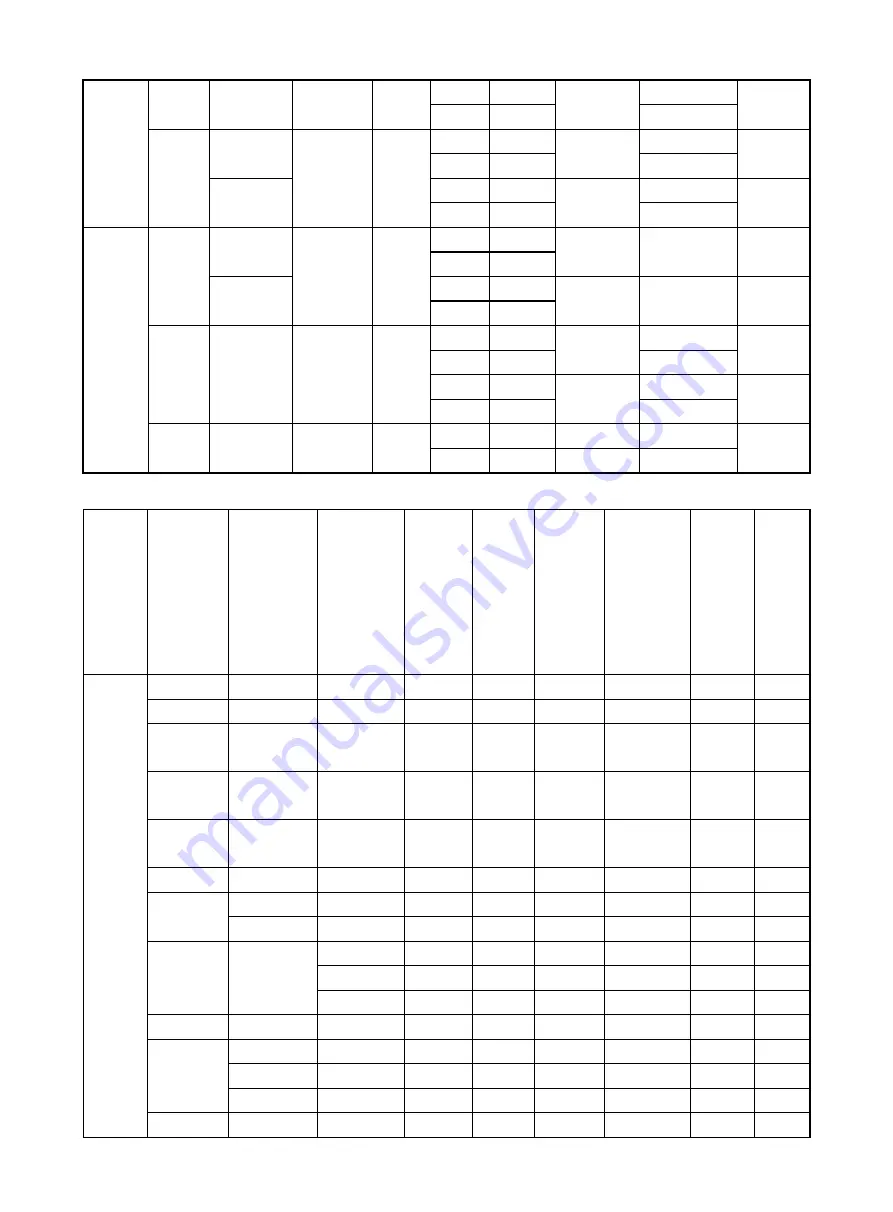
34
welding
1.6
outer 1 380-420
36-39
35-40
20-25
inner1
380-420
45-50
16
1.2
0-0.5
4-6
outer 1 300-350
32-35
25-30
20-25
inner1
300-350
30-35
1.6
outer 1 380-420
36-39
30-35
20-25
inner1
380-420
35-40
X type
butt
welding
16
1.2
0
4-6
outer 1 300-350
32-35
30-50
20-25
inner1
300-350
1.6
outer 1 380-420
36-39
35-40
20-25
inner1
380-420
19
1.6
0
5-7
outer 1 400-450
36-42
25-30
20-25
inner1
400-450
25-30
outer 1 400-420
36-39
45-50
20-25
Inner2
400-420
35-40
25
1.6
0
5-7
outer 1 400-420
36-39
40-45
20-25
Inner2
420-450
39-42
30-35
Table 6-5-3
CO
2
welding
(
solid wire
)
Type
Workpie
ce
thickness
(mm)
Wire
diameter
Φ(mm)
Leg
size(mm)
Weldin
g
current
(
A
)
Weldi
ng
voltag
e
V
Weldin
g speed
cm/min
The
distance
between
contact tip
and
workpiece
(
mm
)
Gas
flow
L/min
Weld
ing
angle
T type
flat fillet
welding
(
low
speed
conditio
n
)
1.0
0.8
2.5-3
70-80
17-18
50-60
10
10-15
45°
1.2
1.0
3-3.5
85-90
18-19
50-60
10
10-15
45°
1.6
1.0 1.2
3-3.5
100-110
18-19.
5
50-60
10
10-15
45°
2.0
1.0 1.2
3-3.5
115-125
19.5-2
0
50-60
10
10-15
45°
2.3
1.0 1.2
3-3.5
130-140
19.5-2
1
50-60
10
10-15
45°
3.2
1.0 1.2
3.5-4
150-170
21-22
45-50
15
15-20
45°
4.5
1.0 1.2
4.5-5
180-220
21-23
40-45
15
15-20
45°
1.2
5-5.5
200-250
24-26
40-50
10-15
10-20
45°
6
1.2
5-5.5
230-260
25-27
40-45
20
15-20
45°
6
220-250
25-27
40-45
13-18
10-20
45°
4-4.5
270-300
28-31
60-70
13-18
10-20
45°
8
,
9
1.2 1.6
6-7
270-380
29-35
40-45
25
20-25
50°
8
1.2
5-6
270-300
28-31
55-60
13-18
10-20
45°
1.2
7-8
260-300
26-32
25-35
15-20
10-20
50°
1.6
6.5-7
300-330
30-34
30-35
15-20
10-20
50°
12
1.2 1.6
7-8
270-380
27-35
27-40
20-25
20-25
50°
Summary of Contents for MIG 350P
Page 13: ...11 4 6 2 Separated machine installation Figure 4 3 ...
Page 19: ...17 3 Operation modes Table 5 2 DC MIG operation modes Modes Sketch map 2T 4T ...
Page 20: ...18 Repeat Spot weldin g 5 2 3 Pulse MIG 1 Synergic and Separate ...
Page 22: ...20 2T with initial crater 4T ...
Page 23: ...21 4T with initial segmen t Special 4T pro gram 4T ...
Page 40: ...38 7 Wiring Diagram ...
Page 42: ...40 ...