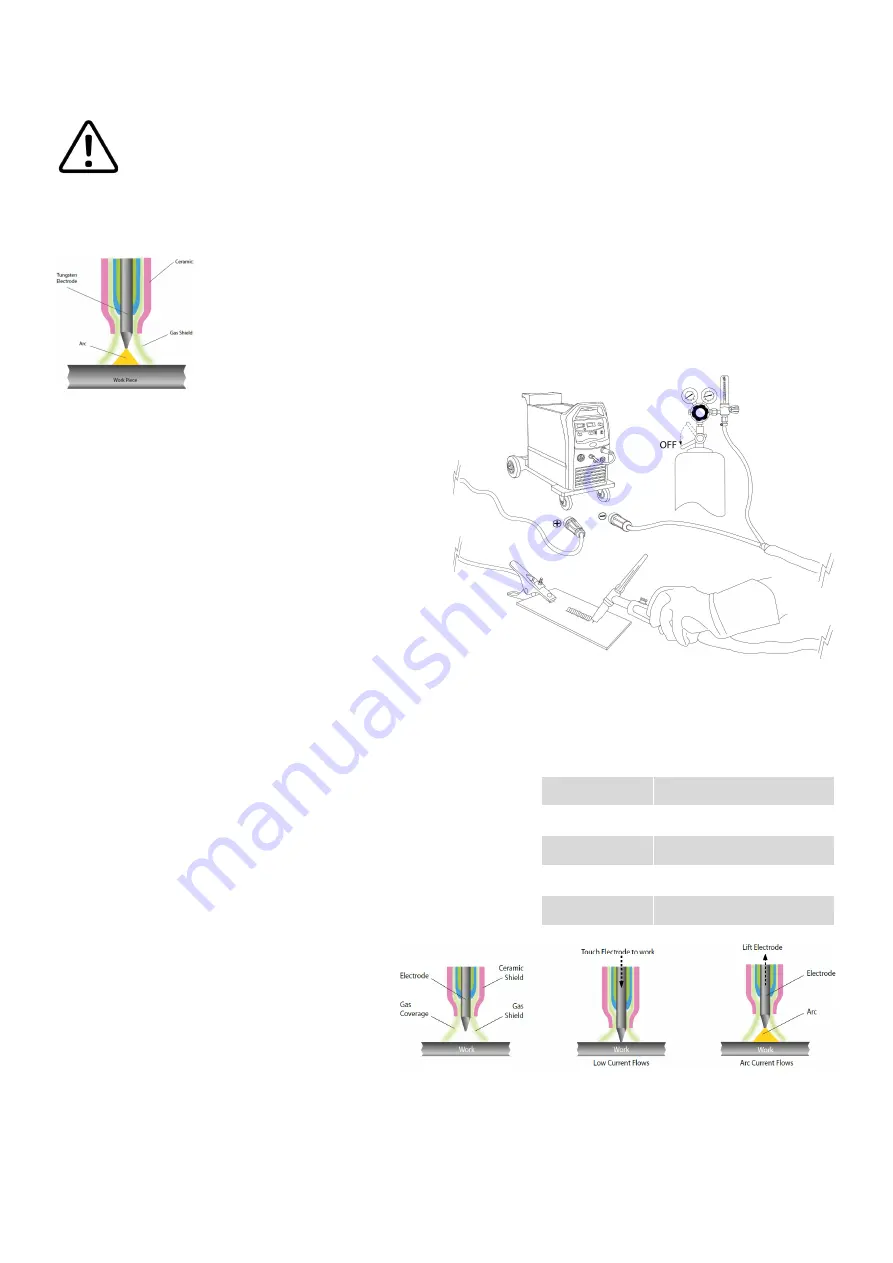
18
OPERATION
-
TIG (JM
-
352C ONLY)
Before starting any welding activity ensure that you have suitable eye protection and
protective clothing. Also take the necessary steps to protect any persons within the welding
area.
TIG welding mode
Terms used: TIG –
Tungsten Inert Gas, GTAW –
Gas Tungsten Arc Welding.
TIG welding is an arc welding process that uses a non
-
consumable tungsten electrode
to produce the heat for welding.
The weld area is protected from atmospheric contamination by a shielding gas (usually
an inert gas such as argon or helium) and a filler rod matching the base material is
normally used, though some welds, known as autogenous welds, are carried out
without the need for filler wire.
When the Jasic 352C is used in Lift TIG mode, you
are required to use a
‘
valve
’
type TIG torch.
Insert the dinse cable plug of the TIG torch to the
“
-
”
socket on the front panel of the machine and fully
tighten clockwise.
Insert the dinse cable plug for the work clamp into
the
“+”
socket on the front panel of the welding
machine and fully tighten clockwise.
Connect the TIG torch gas hose to the regulator or
flowmeter located on the shield gas cylinder.
Before starting any welding activity ensure that you have suitable eye protection and protective
clothing. Also take the necessary steps to protect any persons within the area.
Rotate the power switch on the back panel to
“
ON
”
and then select TIG by switching the welding mode
switch to TIG. Set the amperage on the machine suitable for the application and tungsten being used (see
table).
Ensure you have adequate welding current according to the
thickness of the work and weld prep being carried out and filler
wire being used.
Open the gas valve of the cylinder and then open the gas valve
on the TIG torch and adjust the gas regulator to obtain the
desired flow rate.
The MIG 352C allows the tungsten to be in
direct contact with the work piece with
minimal current so as not to leave tungsten
deposits.
Offer the TIG torch tungsten to the material
to be welded and once contact has been
made (B) the tungsten can then be lifted away 2
-
4mm from the work piece and the welding arc is then
established (C).
Once welding is complete, pull the TIG torch away from the weld area enough to stop the welding arc but
ensure you leave the torch in place to shield the weld with gas for a few seconds until the preset post flow
gas turns off.
Tungsten Size
DC –
Electrode Negative
1.0mm
15
–
80A
1.6mm
70
–
150A
2.4mm
150
–
250A
3.2mm
250A –
400A
A B C
Summary of Contents for MIG 250C
Page 1: ......
Page 44: ...44 EC Declaration of Conformity...
Page 46: ...46 SCHEMATIC Wiring diagram for the JM 202C JM 252C...
Page 47: ...47 SCHEMATIC Wiring diagram for the JM 352C...
Page 50: ...50 January 2023 Issue 10...