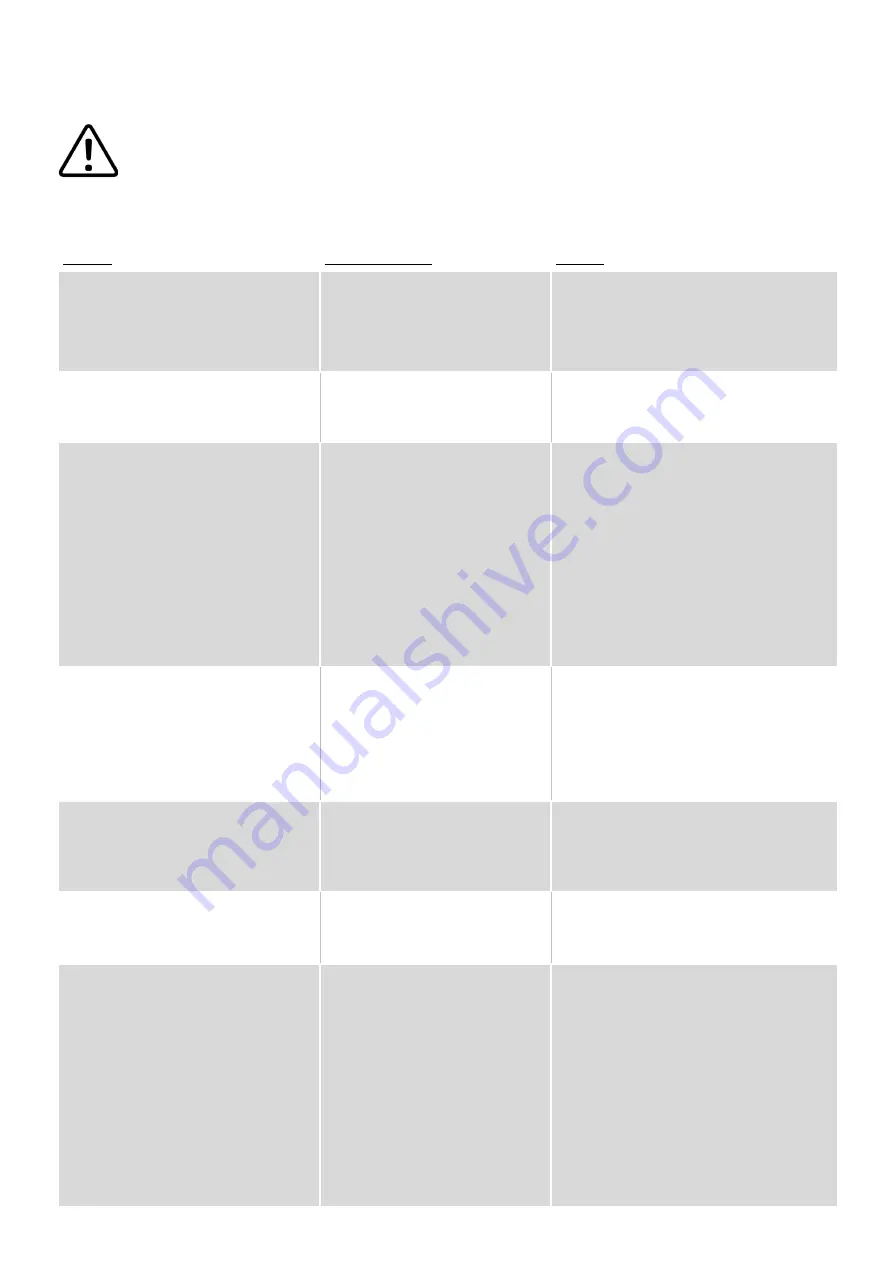
23
MMA WELDING PROBLEMS
Before starting any welding activity ensure that you have suitable eye protection and
protective clothing. Also take the necessary steps to protect any persons within the welding
area.
Arc welding defects and prevention methods
Defect
Possible cause
Action
Excessive spatter (beads of metal
scattered around the weld area)
Amperage too high for the
selected electrode
Reduce amperage or utilise larger
diameter electrode
Voltage too high or arc length
too long
Reduce arc length or voltage
Uneven and erratic weld bead and
direction
Weld bead is inconsistent and
misses joint due to operator
Operator training required
Lack of penetration
-
The weld bead
fails to create complete fusion
between material to be welded,
often surface appears okay but weld
depth is shallow
Poor joint preparation
Insufficient heat input
Poor weld technique
Joint design must allow for full access
to the root of the weld
Material too thick
Increase the amperage or
increase the electrode size
and amperage
Reduce travel speed
Ensure the arc is on the leading edge of
the weld puddle
Porosity
-
Small holes or cavities on
the surface or within the weld
material
Work piece dirty
Electrode is damp
Arc length is excessive
Remove all contaminant from the
material i.e. oil, grease, rust, moisture
prior to welding
Replace or dry the electrode
Reduce the arc length
Excessive penetration
-
The weld
metal is below the surface level of
the material and hangs below
Heat input too high
Poor weld technique
Reduce the amperage or use a smaller
electrode and lower amperage
Use correct welding travel speed
Burning through
-
Holes within the
material where no weld exists
Heat input too high
Use lower amperage or smaller
electrode
Use correct welding travel speed
Poor fusion
-
Failing of weld material
to fuse either with the material to be
welded or previous weld beads
Insufficient heat level
Poor welding technique
Work piece dirty
Increase the amperage or increase the
electrode size and amperage
Joint design must allow for full access to
the root of the weld
Alter welding technique to ensure
penetration such as weaving, arc
positioning or stringer bead technique
Remove all contaminant from the
material i.e. oil, grease, rust, moisture
prior to welding
Summary of Contents for MIG 250C
Page 1: ......
Page 44: ...44 EC Declaration of Conformity...
Page 46: ...46 SCHEMATIC Wiring diagram for the JM 202C JM 252C...
Page 47: ...47 SCHEMATIC Wiring diagram for the JM 352C...
Page 50: ...50 January 2023 Issue 10...