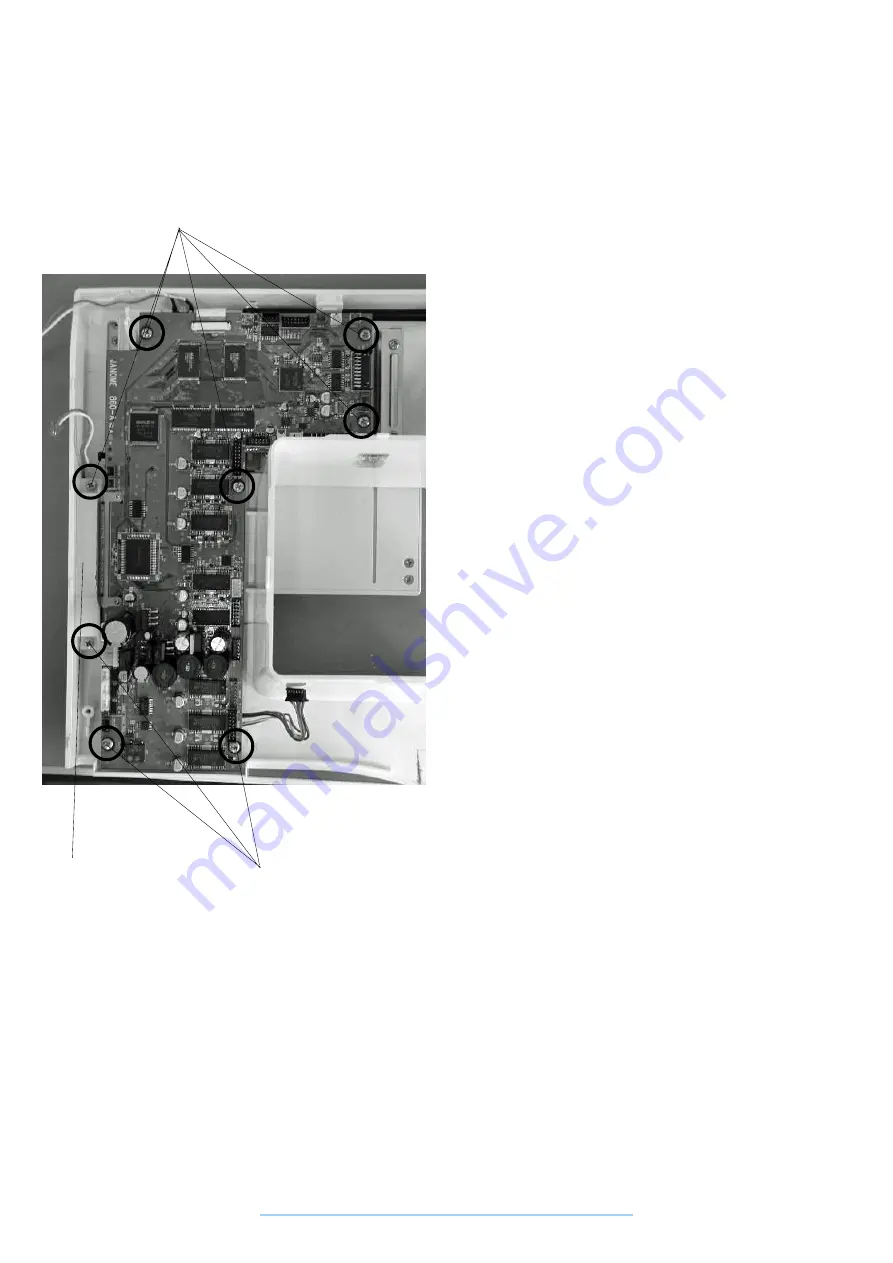
MC 11000
(A)
(A)
Replacing Printed Circuit Board A
To remove:
1. Remove the front cover.
2. Disconnect each connector from printed circuit
board A.
3. Remove the 8 screws (A) and remove printed
circuit board A with the card guide (1).
To remove:
4. Follow the above procedure in reverse.
(1)
12
www.promelectroavtomat.ru