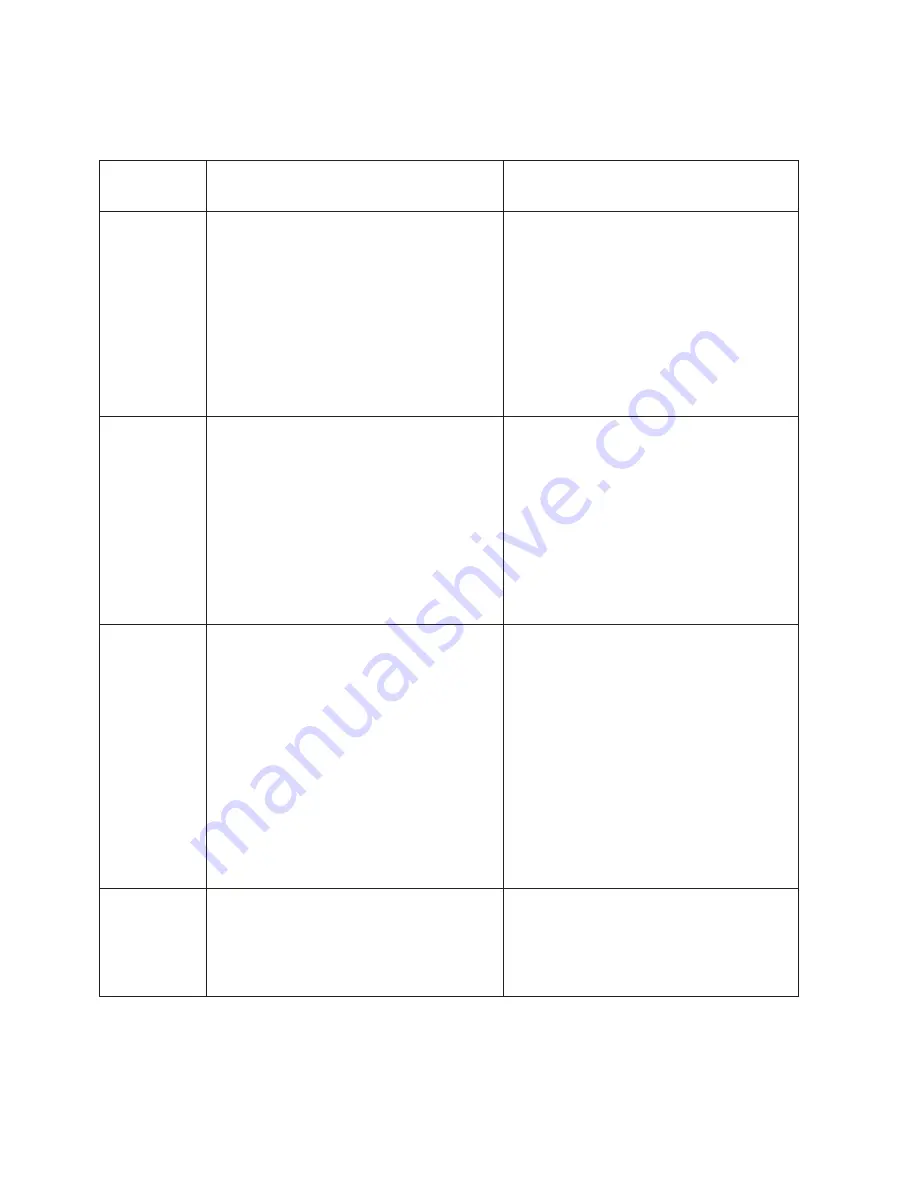
2
1. Bobbin holder is incorrectly threaded.
2. Too much thread is wound on the bobbin.
3. Lint is stuck inside the bobbin holder.
4. Thread quality is too low.
5. Thread is jamming around the bobbin
holder.
1. Needle is hitting the needle plate.
2. Needle is bent or worn.
3. Needle is hitting the hook.
4. Fabric is being pulled too strongly while
sewing.
Set the bobbin thread correctly.
Adjust the position of bobbin winder
stopper.
Clean the bobbin holder.
Change to a high quality sewing thread.
Clear out the jamming thread.
Adjustment of Needle Drop Position
(Reference P.9)
Change the needle.
Adjustment of Clearance between Needle
and Tip of Hook Rotary (Reference P.12)
Guide the fabric gently while sewing
Needle
breakes
Condition
Cause
How to Fix
1. Lower shaft gear is loose.
2. Inappropriatte belt tension.
3. Not enough oil.
4. Upper shaft gear is loose.
Eliminate the looseness.
See part removal and
replacement “driving motor (DC motor)”.
(Reference P.25)
Oil all moving parts.
Eliminate the looseness.
1. Top tension is too strong.
2. Inappropriate feed balance.
Adjustment of top tension.
Adjust the feed balancing screw.
Noisy
operation
Deformation
pattern