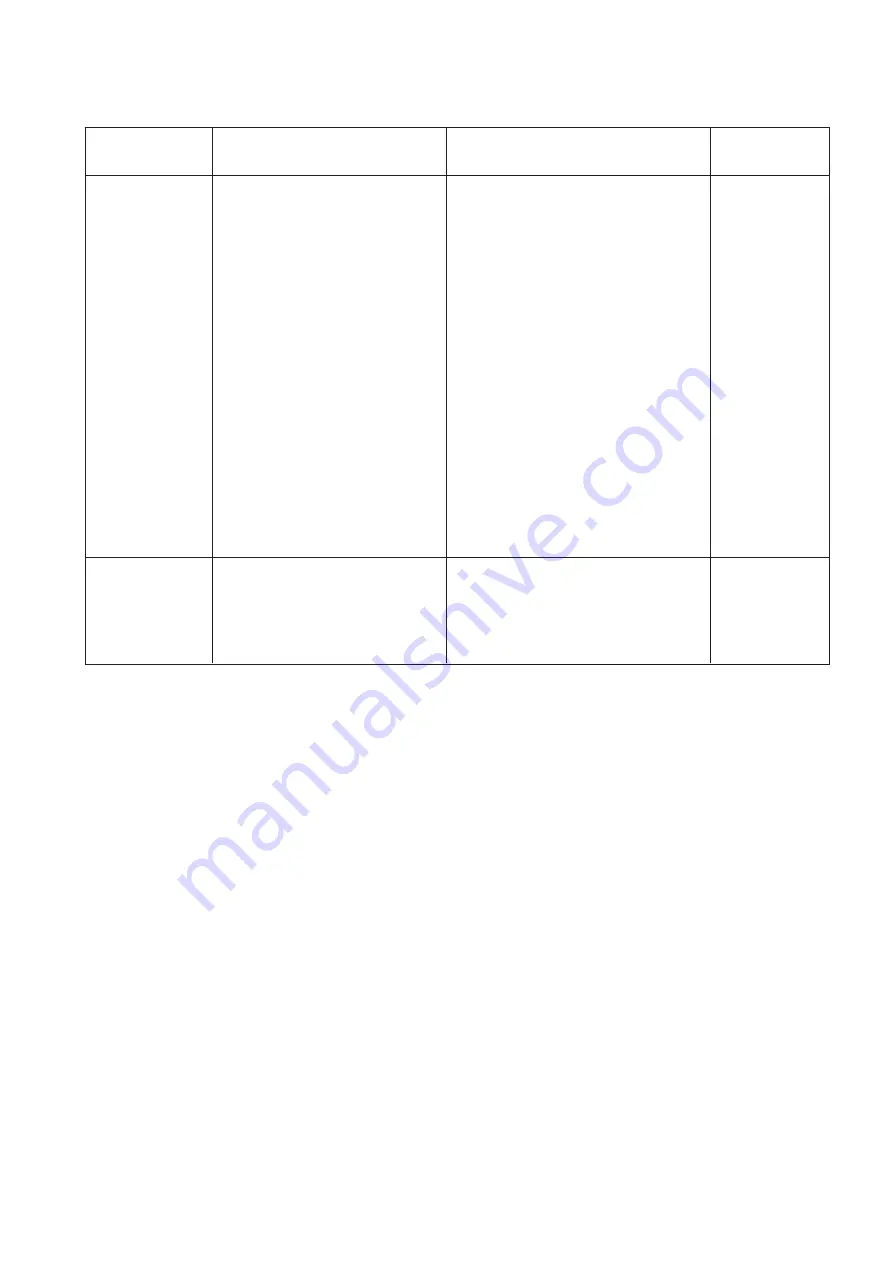
3
Condition
Cause
How to fix
Reference
6. Noisy
operation
1. Backlash between hook gear
and lower shaft gear is too
great.
2. Lower shaft gear is loose.
3. Inappropriate belt tension.
4. Not enough oil.
5. Upper shaft gear is loose.
Eliminate the backlash.
Eliminate the looseness.
See part removal and replacement
“Driving motor (DC motor)”.
Oil all moving parts.
Eliminate the looseness.
P. 33
7. Deformation
pattern
1. Inappropriate feed balance.
2. Top tension is too strong.
Adjust the feed balancing dial.
See mechanical adjustment
“Top tension”.
P. 17
P. 16
WHAT TO DO WHEN
Summary of Contents for 5270QDC
Page 1: ...First Edition 06 March 2020 SERVICE MANUAL PARTS LIST MODEL 5270QDC For Europe only...
Page 39: ...37 TOUCH PANEL KEY POSITION ADJUSTMENT GUIDE Print this illustration guide to its actual size...
Page 52: ...50 MODEL 5270QDC PARTS LIST 1 2 3 4 6 5 7 8 9 10 11 12 13 14 17 15 18 19 20 9 21 21 22 23 16...