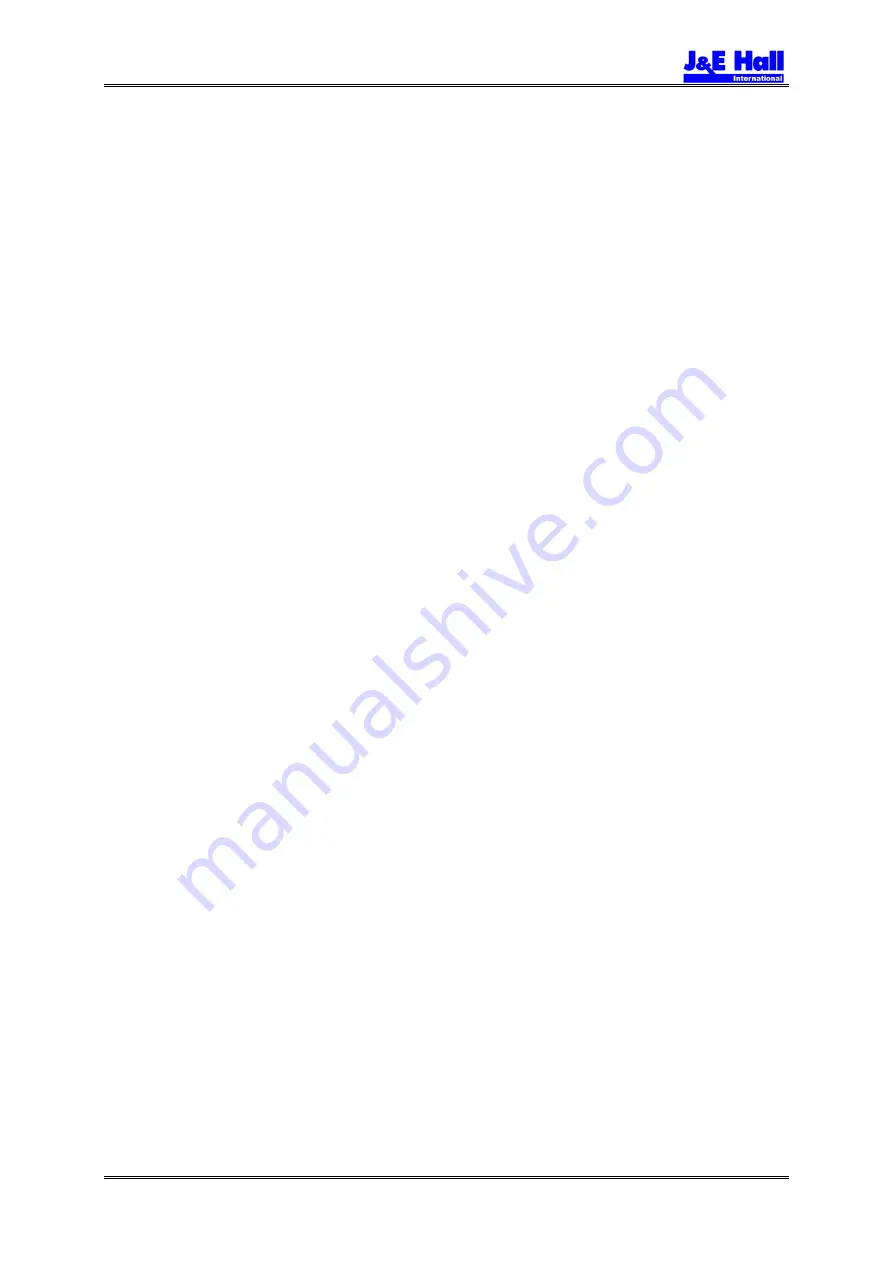
HSO 2024 to HSO 2035 Installation, Operation and Maintenance Manual
Issue 1.2 : 03/10
Publication 2-119
Page 25 of 94
4.5.
Capacity Control by Inverter Drive
Instead of using the slide valves, compressor capacity can be controlled
using a frequency inverter (also known as Variable Speed Drive or
Variable Frequency Drive). If an inverter is used, the load/unload
solenoid valves need to be controlled to allow the compressor to start at
minimum load but load to full load when the compressor is running.
There are three methods of achieving this;
•
Energise the load solenoid continuously irrespective of
whether the compressor is running or not.
•
Energise the load solenoid continuously when the
compressor is running and the unload solenoid continuously
when the compressor is stopped.
•
Remove the plunger from the load solenoid valve (only) and
do not fit the coils.
When using an inverter, it is of utmost importance that it is both sized and
set up correctly.
4.5.1.
Inverter Size
The inverter must be sized to deliver the maximum current taken by the
compressor motor at the maximum power conditions – in most cases this
is during pull down.
NOTE: the current capacity of an inverter drive is not
reduced by running at less than synchronous speed.
During pull down, the current can be limited by either using the slide
valves to run the compressor unloaded, or by throttling the suction. If it is
required to use the slide valves during pull down, then normal manual
slide valve control can be used; refer to 4.2. Capacity Control Solenoid
Valve Arrangements.
4.5.2.
Inverter Set-up
The inverter drive used must have the following facilities as a minimum;
•
Load type: constant torque.
•
Control method: PID (automatic) with facility for manual
frequency control.
Particular attention has to paid to setting up the inverter with the correct
minimum frequency, maximum frequency and acceleration time.
NOTE: minimum frequency and maximum frequency
must be set according to the operating conditions; refer
to J & E Hall International.