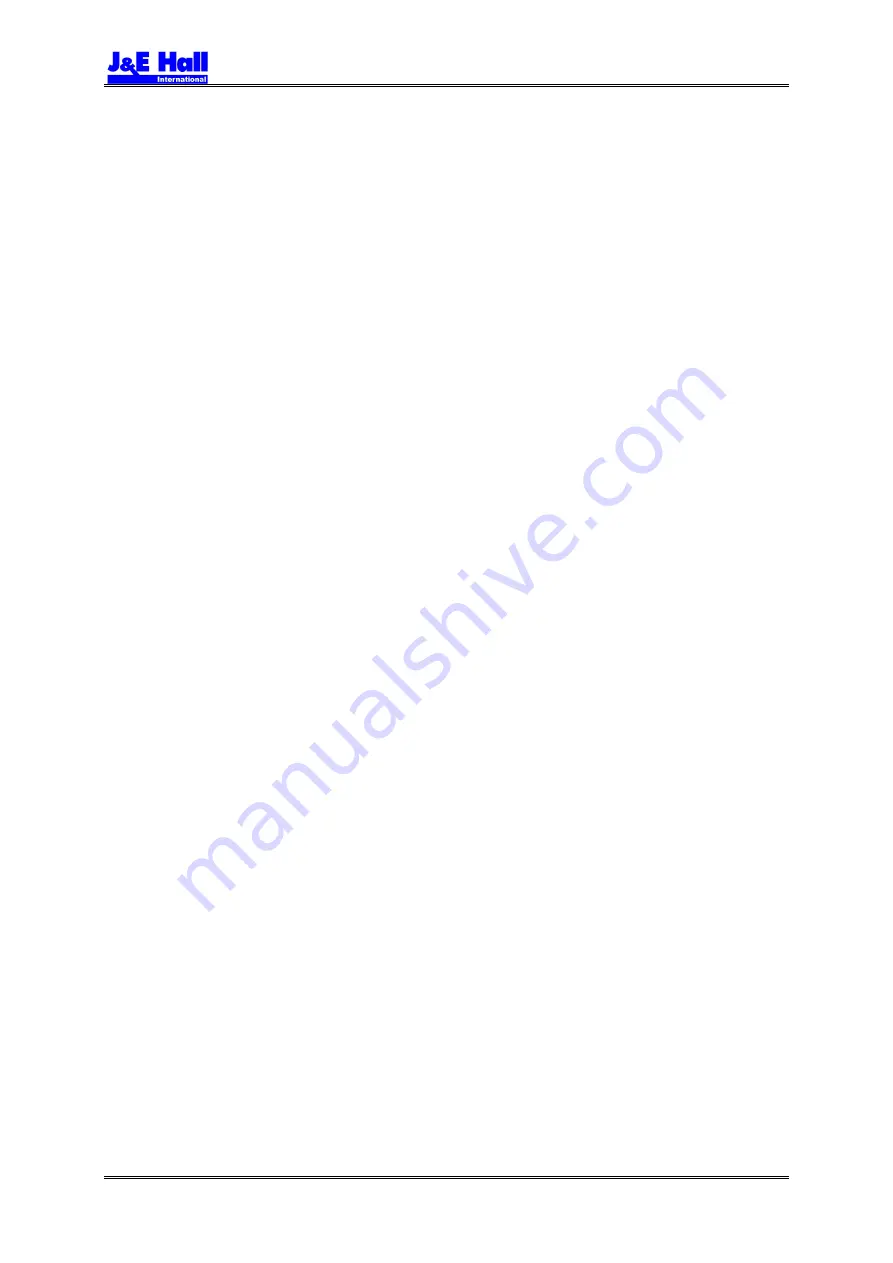
HSO 2024 to HSO 2035 Installation, Operation and Maintenance Manual
Page 2 of 94
Publication 2-119
Issue 1.2 : 03/10
J & E Hall International
©
2010
All rights reserved. No part of this publication may be reproduced or transmitted in any form or by
any means, electronic or mechanical, including photocopying, recording or by any information
storage or retrieval system, without permission in writing from the copyright holder.
The copyright in this publication shall be and remain the sole property of J & E Hall International.