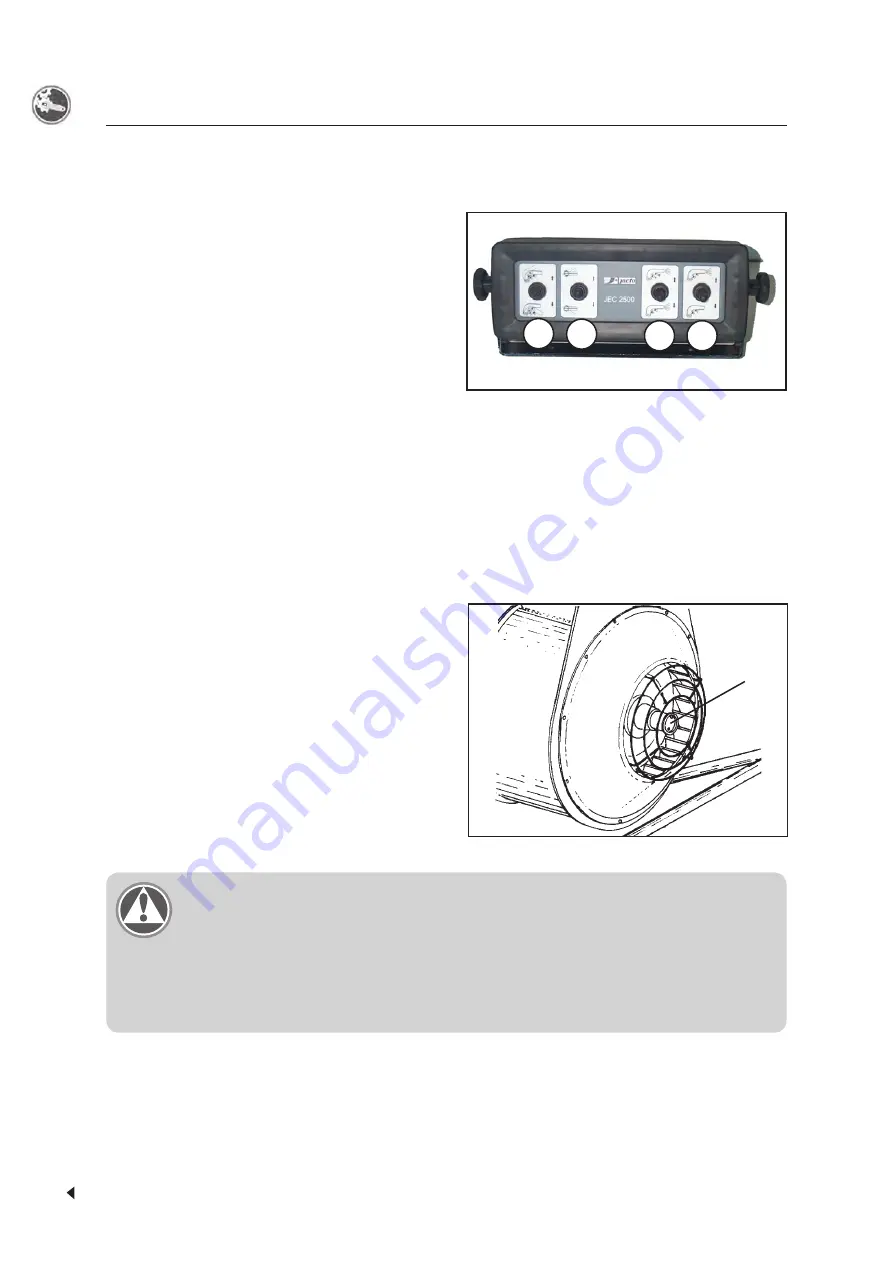
6
CHAPTER 4 - OPERA
TION AND ADJUSTMENTS
J-600 ELECTRIC
JEC-2500 Control panel / Fan lock
∙ The JEC-2500 control panel allows to turn on
and off the duct flow and to adjust the duct
spray angle.
∙ The switch (1) adjusts the duct height down-
ward or upward.
∙ The switch (2) adjusts the duct to the left and
right.
∙ The switch (3) allows to turn on and off the
flow.
∙ The switch (4) sets the flow only to the main
duct or to all ducts (main and auxiliary).
> JEC-2500 control panel
1
2
3
4
∙ This device is specifically designed to lock the
fan off in order to reduce power consumption
when the use of fan is not required, that is, while
filling the tank and agitating the chemical mixture
before starting to spray.
∙ To lock the fan, pull the lock and give it a quar-
ter turn.
∙ To unlock, pull the lock, give it a quarter turn
and then push it again.
> Fan lock
fan lock
ATTENTION!
Always disengage the PTO and wait for fan to stop completely before operating the fan lock.
For tractors with independent PTO, the following is recommended:
∙ Do not engage the PTO with the engine accelerated.
∙ With the engine idling, engage the PTO and gradually accelerate until reaching the rotation
recommended.