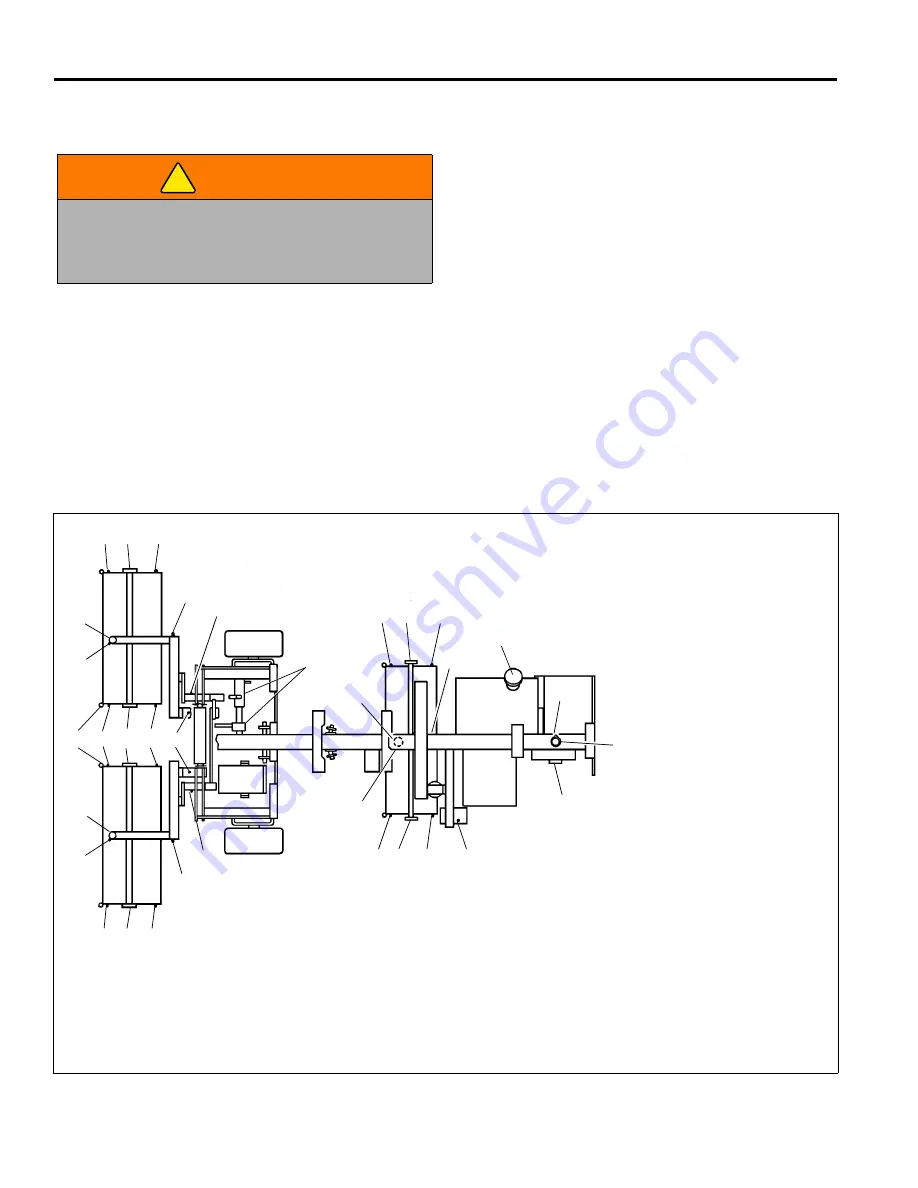
6 LUBRICATION CHART
22
6
LUBRICATION CHART
6.1 GENERAL ________________________________________________________________
1.
Always clean the grease fitting before and after
lubricating.
2.
Lubricate with grease that meets or exceeds NLGI
Grade 2 LB specifications. Apply grease with a
manual grease gun and fill slowly until grease begins
to seep out. Do not use compressed air guns.
3.
Periodically apply a small amount of lithium based
grease to the seat runners.
4.
For smooth operation of all levers, pivot points, and
other friction points that are not shown on the
lubrication chart apply several drops of SAE 30 oil
every 40 hours or as required.
5.
Grease roller fittings (
F
) every 100 hours and coat
cam surfaces and pins of swivel housing (
J
) every 50
hours.
6.2
LUBRICATION CHART _____________________________________________________
WARNING
Before you clean, adjust, or repair this equipment,
disengage all drives, lower implements to the ground,
engage parking brake, stop engine, and remove key
from ignition switch to prevent injuries.
!
H
F
L
F
B
F
L
F
B
H
E
K
G
J
A
F L
F
B
D
A
A
J
J
B
B
C
C
F L
F
F L
F
A.
Mower Swivel Housings
B.
Lift Arms
C.
Cam Lift Shafts
D.
Treadle
E.
Steering Shaft
F.
Rollers
G.
Rear Wheel Bearings (See Chart)
H.
Hydraulic Oil Tank (See Chart)
J.
Swivel Arm Assembly
K.
Rear Wheel Bearing
L.
Reel Bearing Cavities
Summary of Contents for Greens King IV 62302
Page 23: ...NOTES 7 23 7 NOTES...
Page 24: ...7 NOTES 24...