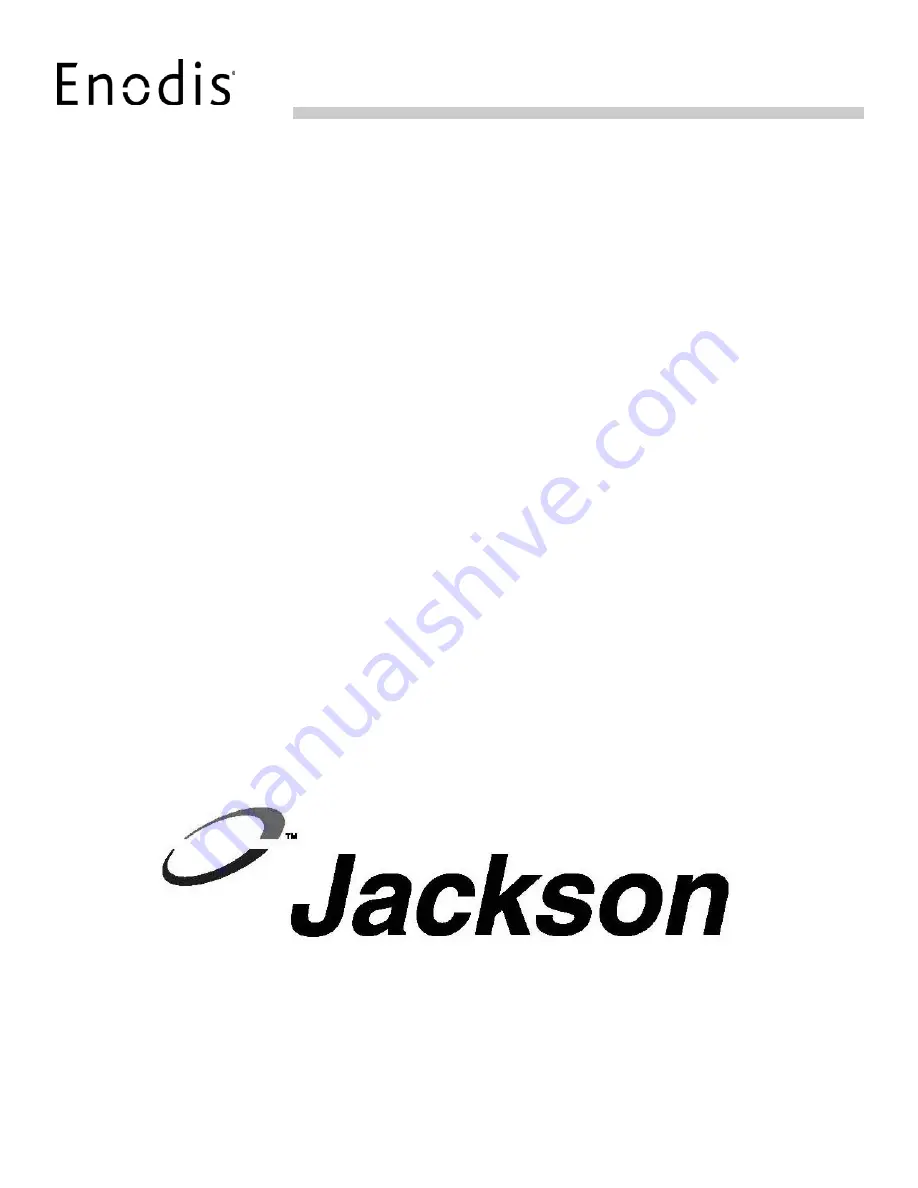
INSTALLATION/OPERATION &
TECHNICAL MANUAL
FOR JACKSON MODELS:
AND ASSOCIATED OPTION PACKAGES INCLUDING:
SIDE LOADER
D226 EXTERNAL STEAM BOOSTER
Jackson MSC LLC.
P.O. Box 1060
Barbourville, KY. 40906
(606) 523-9795
Fax: (606) 523-9196
www.jacksonmsc.com
AJ-54 RACK CONVEYOR DISHMACHINE SERIES
April 19, 2007
P/N 7610-002-30-91 (Revision E)
AJ-54CE
AJ-54CGP
AJ-54CS
AJ-76CE
AJ-76CGP
AJ-76CS
AJ-90CE
AJ-90CS
Summary of Contents for Enodis AJ-54 Series
Page 9: ...1 SECTION 1 SPECIFICATION INFORMATION ...
Page 24: ...16 SECTION 2 INSTALLATION OPERATION INSTRUCTIONS ...
Page 41: ...33 SECTION 3 PREVENTATIVE MAINTENANCE ...
Page 45: ...37 SECTION 4 TROUBLESHOOTING SECTION ...
Page 49: ...41 SECTION 5 SERVICE PROCEDURES ...
Page 72: ...64 SECTION 6 PARTS SECTION ...
Page 132: ...124 SECTION 7 ELECTRICAL SCHEMATICS ...
Page 153: ...145 SECTION 8 JACKSON MAINTENANCE REPAIR CENTERS ...
Page 160: ......