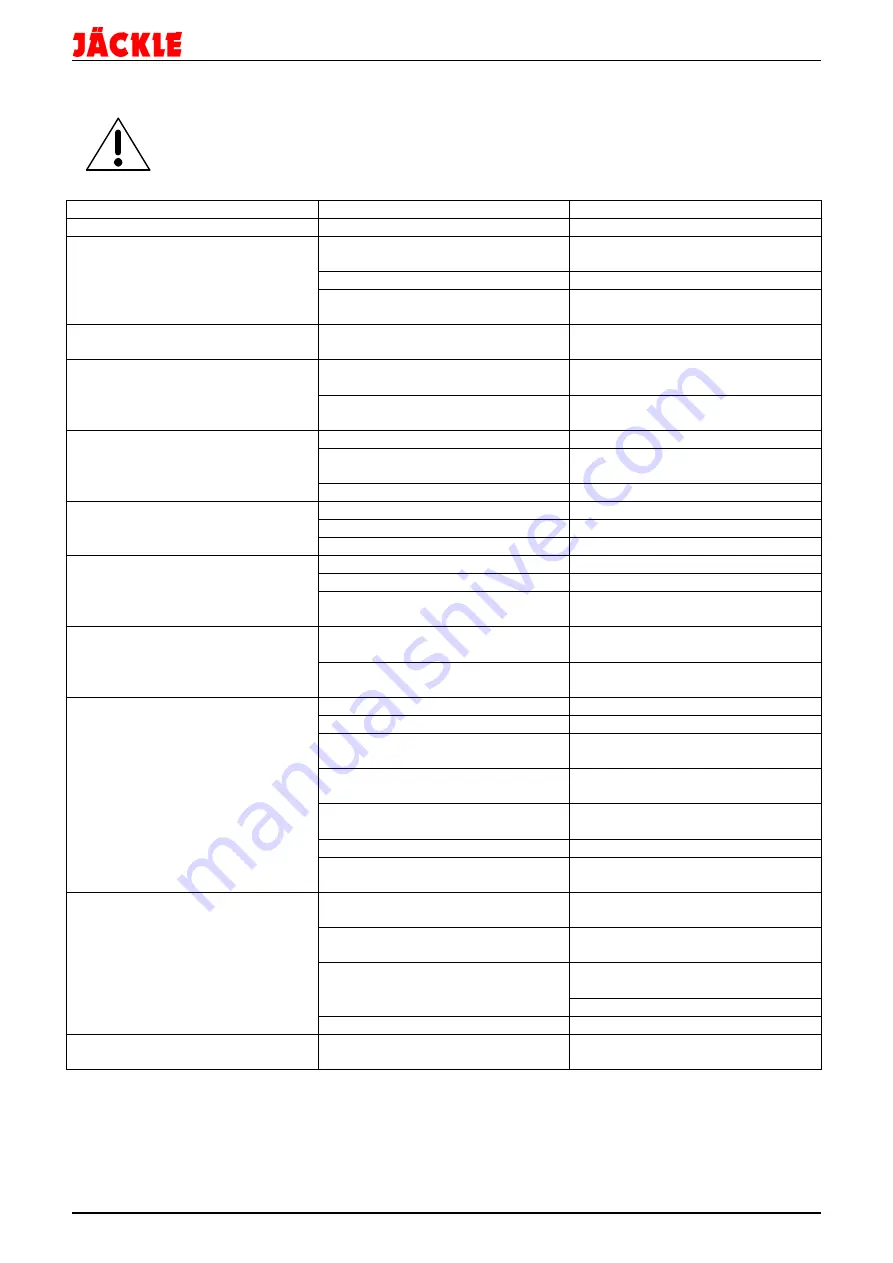
MIG 325,405,505
Operating manual
Page 36
38. Trouble - shooting
Any remedial action to defective electrical equipment must be carried out
by a qualified electrician!
Malfunction/error
Cause
Remedy
Error Display
T°C – 01/02/03 – hot
or
E t°C
Engine overheated
(See Point 33)
Machine to cool down with a
running fan
Thermal sensor line interrupted
Look for and eliminate interruption
Wrong type of machine in the
control box set
Contact service partner
Error display E H2o
(only with watercooled machines)
Cooling water circulation
interrupted
Check circulation
Check water pump function
Display
T°C – int – z.B +56
(See Point 20)
Ambient temperature below -10 ° C
or above +40 ° C
Bring Machine into normal
temperature range
Thermocouple defect in the control
box
Change control box
Sensor repaired
Main switch ON
Control box MC without function
Failed one or more system phases
Check main supply and fuses
Primary fuse on auxiliary
transformer defective
Change fuse 2A slow
Fuse in control box MC defective
Change fuse 6,3A slow
No function after pressing torch
trigger key
Torch trigger defective
Change torch trigger
Torch control line interrupted
Check torch control line
Control box MC defective
Change control box
Fire feed motor out of service
Control box MC defective
Change control box
Fire feed motor defective
Change wire feed motor
Wiring between control box and
Motor interrupted
Check wiring
Wire buckling between wire feed
rollers and guide tube
Pressure of the wire feed rolls to
big
See chapter 29
Distance from wire feed rollers to
guide tube too far
Ceck distance / realign wire guide
tube
Irregular wire feed
Bad uncoiling of wire
Ceck / refit wire coil
Wire-holding arbor runs heavily
Ceck wire- holding arbor
Wrong wire feed roller
Use the right wire feed roller
See chapter 29
Dirty / defective wire guide tube or
spiral
See chapter 29
Cogged / defective current contact
tip
Clean / exchange current contact
tip
Dirty/ rusty welding wire
Exchange welding wire
Wire guide tube misaligned with
wire feed roller groove
See chapter 29
Porous weld seam
Workpiece surface polluted(paint,
rust, oil, grease)
Clean surface
No shieldig gas(solenoid valve not
opening)
Check / exchange solenoid valve
or gas tube
Insufficient shielding gas
Check shielding gas at pressure
reducer
Check gas line for leakage
Gas nozzle polluted
Clean gas nozzle
Wire burns back into current
contact tip at start of process
Deficient wire feed, feed rollers
idling
See chapter 29