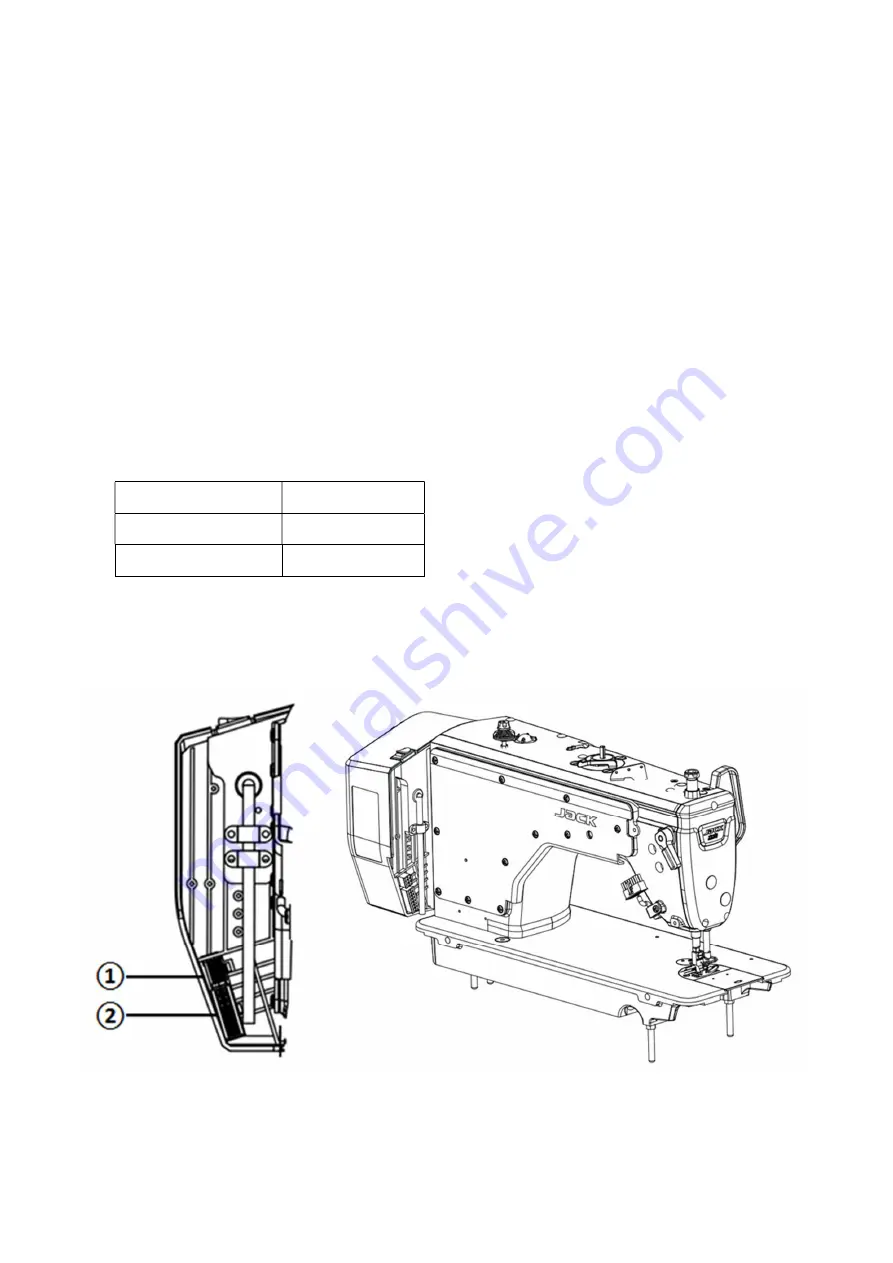
1
/
14
ZB-A4F electric control box manual
·
Safety Precautions
·
Before using this product, please read the User's Guide and the manual of the machine attached with it.
·
This product must be installed or operated by professionally trained personnel.
·
Please keep away from the arc welding equipment to avoid the electromagnetic wave from interfering with the
controller.
·
Please do not use it at room temperature above 45°or below 0°
。
·
Please do not use it in places with humidity below 30% or above 95% or where there is dew and acid mist.
·
When installing the control box and other parts, turn off the power and unplug the power plug.
·
To prevent interference or electric leakage accidents, make a good grounding work. The grounding wire of the
power cord must be firmly connected to the earth.
·
All parts for maintenance must be supplied or approved by the Company before they can be used.
·
The power must be turned off and the plug unplugged before any maintenance action is performed.There is a
high-voltage danger in the control box. You must shut down the power for 5 minutes before opening the control
box.
1 Product Installation
1.1 product specification
Voltage
AC 220±20% V
Supply frequency
50Hz/60Hz
maximum output power
550W
1.2 The connection of interface plug
Insert the connecting plugs of the foot pedal and the head of the machine into the corresponding socket at the back of the
controller. Each socket names are shown in figure 1-2-2.Please check whether the plug is inserted.