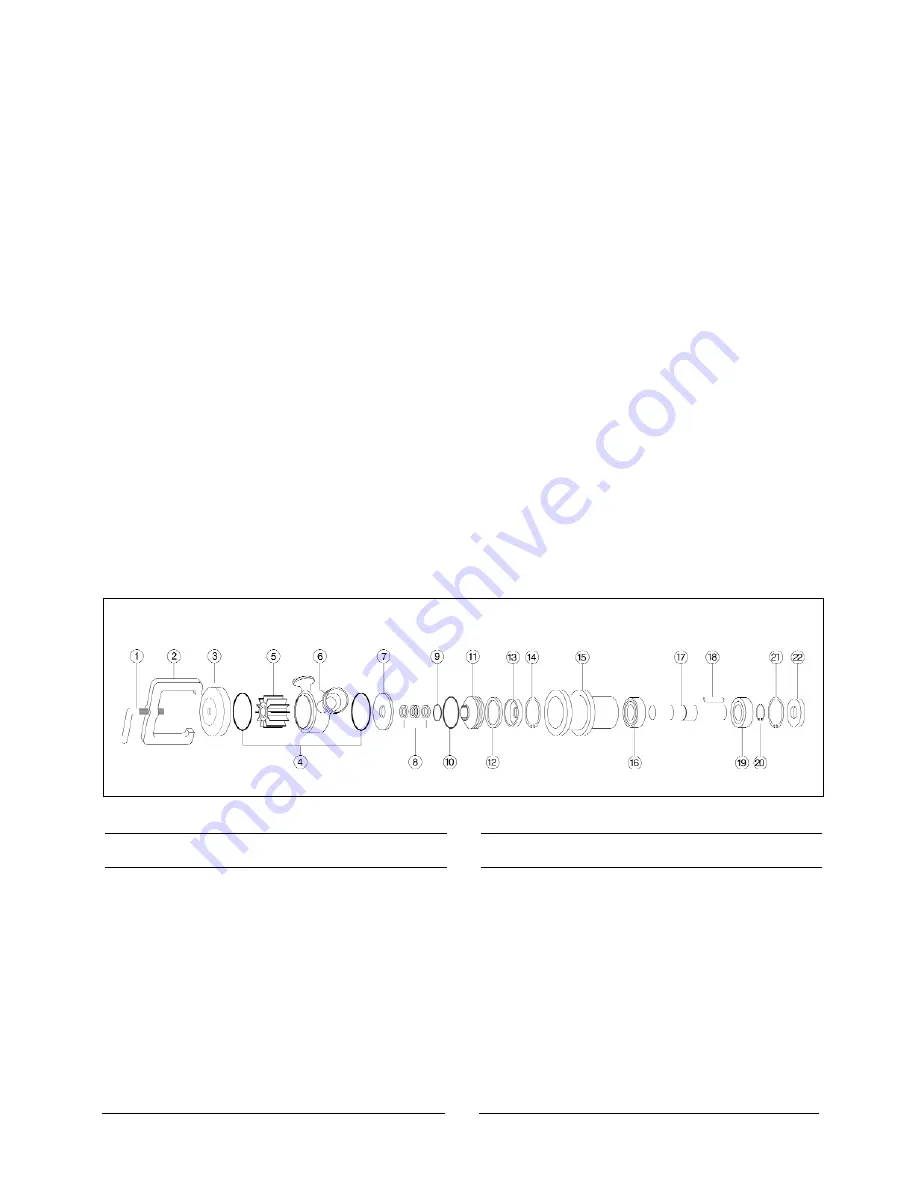
EXPLODED VIEW
SPARE PARTS LIST
Part
Key
Description
Qty.
Number
1
Clamp Screw
1
21908-0001
2
Clamp Frame
1
21909-0000
2 Clamp Frame CIP 1 286420000
3
End Cover
1
22007-0000
3 End Cover CIP 1 287120000
4
O-ring
2
92000-1213
5
Impeller
1
218990005B
6
Body
1
28704-
7
000
7
Wearplate
1
21937-0000
8
Seal Kit
1 226448000B
9
V-Ring
1
X5280-015
10
O-ring
1
X4020-379A
* Oring CIP 1 X4020424A
11
Seal Housing
1
23933-0000
Part
Key
Description
Qty.
Number
12
Lip Seal
1
X5280-011
13
Lip Seal Kit
1
92701-0880
14
Retaining Ring (Hsg)
2
91701-4391
15
Bearing Hsg
1
22064-0100
16
Roller Bearing (front)
1
92601-0460
17
Shaft
1
219780000
18
Key
1
91402-0270
19
Ball Bearing (rear)
1
92601-0450
20
Retaining ring (shaft)
1
91700-2870
*
By-Pass Endcover Kit
1
2870-000
0
*22 Clamp Screw CIP 1 287140000
*24 End Cover Piston CIP 1 287110000
* Handle Assy CIP End Cover 1 287180000
*
Not Shown
SERVICE INSTRUCTIONS
DISASSEMBLY
1.
Remove end cover clamp. Remove end cover and
O-ring.
2.
Slide body, complete with impeller and wearplate,
from shaft assembly. Remove impeller from body.
3.
Remove mechanical seal from shaft. Use extreme
care not to mar shaft surface. Remove seal seat and
O-ring from recess in wearplate.
4.
From the drive end of the bearing housing, pry out
bearing seal by inserting a screwdriver blade
between OD of the seal and housing. Remove
retaining ring. Very carefully withdraw shaft and
bearing assembly.
5.
Remove inner bearing seal and retaining ring.
6.
To remove bearings from shaft an arbor press is
required. If an arbor press is not available then a
bearing extractor may be used. Supporting inner
race of bearing, apply a steady pressure on shaft
until bearing slides free. Repeat this procedure to
remove second bearing.
ASSEMBLY
1.
To replace bearing on shaft. Support bearing on its
inner race and locate shaft onto bearing. Apply a
steady pressure to the shaft until bearing locates
against shoulder on shaft. Repeat for second bearing.
2.
Fit retaining ring and bearing seal into impeller end
of bearing housing. Spring on bearing seal to face
outwards.
3.
Apply bearing grease around and between bearings,
filling cavity between bearings two thirds full. Smear
grease on shaft where bearing seal locates. Push
shaft and bearing assembly into bearing housing.
4.
Replace the two retaining rings and outer bearing
seal, with spring facing outwards, on drive end of
bearing housing.
5.
Replace mechanical seal by sliding positioning
washer onto shaft up to locating shoulder, then
smear shaft with light lubricating oil. Push on seal
gently until it engages with washer. Fit O-ring and
seal seat into wearplate.
6.
Insert impeller in pump body. Fit O-ring on each end
of the pump body. Fit wearplate to body.
7.
Slide wearplate and body assembly over shaft,
positioning wearplate in housing.
8.
Fit end cover and end cover clamp. Clamp should
be hand tightened. Do not use wrench or hammer.
9.
Changing Pump Rotation (looking at end cover):
Clockwise Rotation:
Insert impeller into pump
body with blades bending counterclockwise.
Counter-clockwise Rotation:
Insert impeller into
pump body with blades bending clockwise.