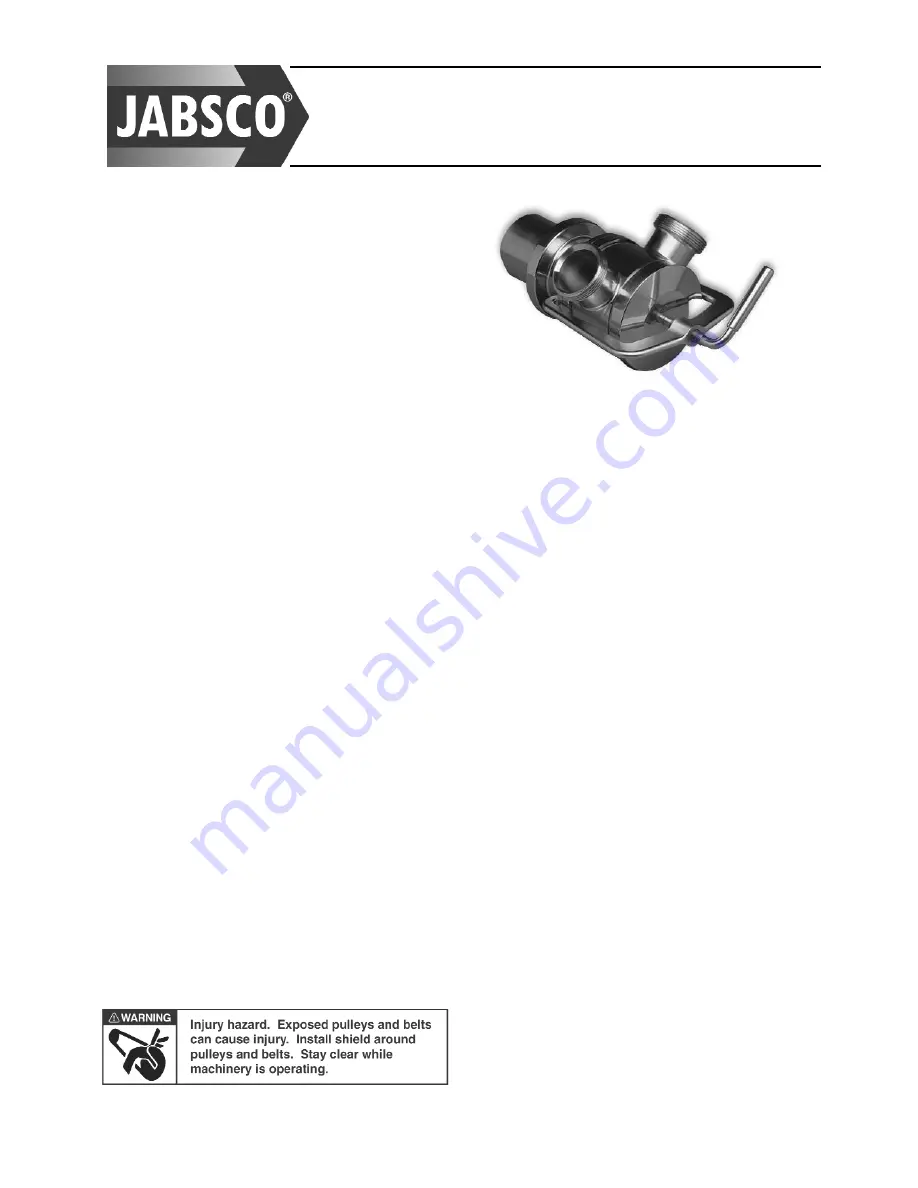
Model 22060-
7125 (C)
SANITARY PUMP
Standard Pressure Impeller
SMS
Ports
FEATURES
Body:
Type 316 Stainless Steel
Impeller:
Jabsco Sanitary Neoprene Compound
Seal:
Sanitary Mechanical
Bearings:
Ball/Roller Bearings
Shaft:
Type 316 Stainless Steel
Ports:
SMS 1145
Threads
Weight:
50 lb (23 kg) Approx.
APPLICATION
This product is specifically designed for farm pick-up
milk tanker trucks. Jabsco pumps are also available as
pedestal mounted or close-coupled units with capacities
to 100 GPM for other sanitary applications. Contact
factory for details.
OPERATING INSTRUCTIONS
1.
INSTALLATION – Pump may be mounted in any
position. The rotation of the pump shaft determines
the location of the pump’s intake and discharge
ports. Refer to dimensional drawing. Pump is
normally assembled at factory for clockwise rotation
looking at end cover. If counterclockwise rotation is
desired, follow steps 1 and 2 of disassembly and
step 9 of assembly instructions to change direction
of impeller blade deflection under cam.
2.
DRIVE – Belt or direct with flexible coupling. Belt
Drive: Overtight belt load will reduce pump bearing
life. Direct Drive: Clearance should be left between
drive shaft and pump shaft when installing coupling.
Always mount and align pump and drive shaft before
tightening the coupling set screw. If pulley or
coupling must be pressed on shaft, remove end
cover and impeller to support shaft from impeller end
during press operation. Do not hammer pulley or
coupling on shaft; this may damage bearing or seal.
Capacitor start motor is required to overcome
starting torque of impeller.
3.
SPEEDS – 100 RPM to the maximum shown in the
performance curves. For longer pump life, operate
at lowest possible speeds. Lower speeds are
required for viscous liquids, consult the factory for
proper speeds and horsepower requirements.
4.
SELF-PRIMING – Primes at low or high speeds. For
vertical dry suction lift of 10 feet, a minimum of 800
RPM is required. Pump will produce suction lift up to
22 feet when wet. BE SURE SUCTION LINES ARE
AIRTIGHT OR PUMP WILL NOT SELF-PRIME.
5.
DISCHARGE - When transferring liquids further
than 25 feet, use 3" discharge line.
6.
RUNNING DRY – Unit depends on liquid pumped
for lubrication. DO NOT RUN DRY for more than 30
seconds. Lack of liquid will damage the impeller.
7.
PUMPAGE COMPATIBILITY – When corrosive
cleaning fluids are handled, pump life will be
prolonged if pump is flushed with a neutralizing
solution after each use or after each work day. A
Tungsten Carbide Seal variation is available for
pumping liquids that contain abrasives or are highly
corrosive.
8.
PRESSURES – Consult Performance Curves for
maximum recommended pressures for pump in
continuous operation. If pressures exceed those
shown, consult the factory.
9.
TEMPERATURES – The operating temperature limits
of the pump: 45° to 150° F (7° to 65° C).
N.B.
3A option to include Elastomers : EPDM and
Neoprene. Ports : Tri-Clamp, IDF, 3A and DIN11851.