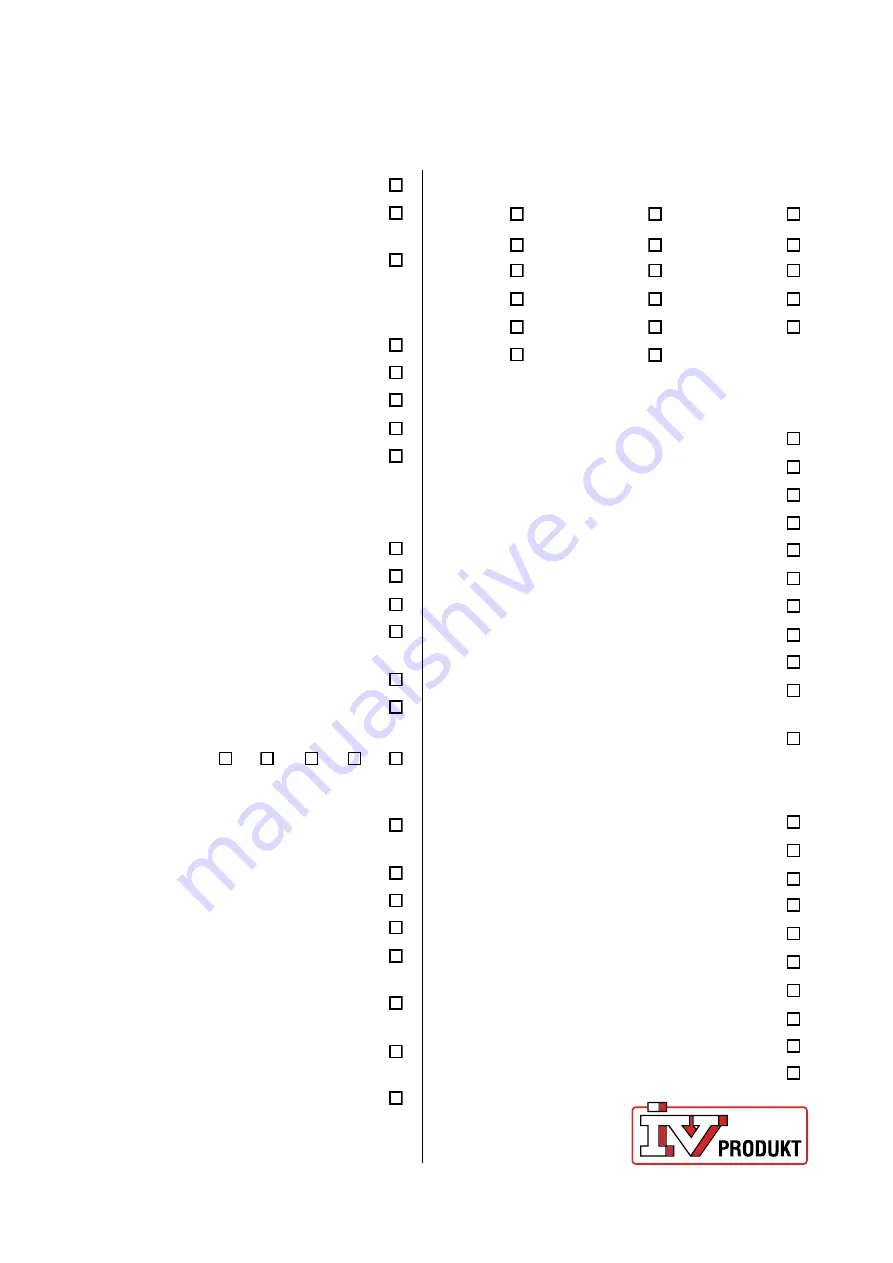
Unit specifications
Size
060 360
980
100 400
1080
150 480
1250
190 600
1280
240 740
1540
300 850
Filter, supply air
Coarse-65% (G4)
ePM10-60% (M5)
ePM2,5-50% (M6)
ePM1-50% (F7)
ePM1-60% (F7)
ePM1-70% (F8)
ePM1-85% (F9)
ePM1-70% (C7)
Aluminium
Excl. filter
Set of filters Black Ridge BR
Filter extract air
Coarse-65% (G4)
ePM10-60% (M5)
ePM2.5-50% (M6)
ePM1-50% (F7)
ePM1-60% (F7)
ePM1-70% (F8)
ePM1-85% (F9)
ePM1-70% (C7)
Aluminium
Excl. filter
Cooling unit ECO, ECX
Reversible heat pump TCH
Home Concept configuration
Control equipment
MX
US
UC
MK
HS
Unit parts and accessories
Plate heat exchanger EXP
Counter-flow exchanger EXM
Rotary heat exchanger EXR
Run-around coil unit EXL
Air heater water EMT-VV, ELEV
ThermoGuard ESET-TV, ELTV
Air heater electric ESET-EV, ELEE
Eff-var
1
2
3
4
5
Air cooler water
ESET-VK, ELBC, ESET-DX, ELBD
Damper ESET-TR, EMT-01
Intake section MIE-IU
Exhaust air section EAU
Recirculating unit EBE
Sound attenuator EMT-02, MIE-KL
Carbon filter section ECF
Filter bypass ENFT-10