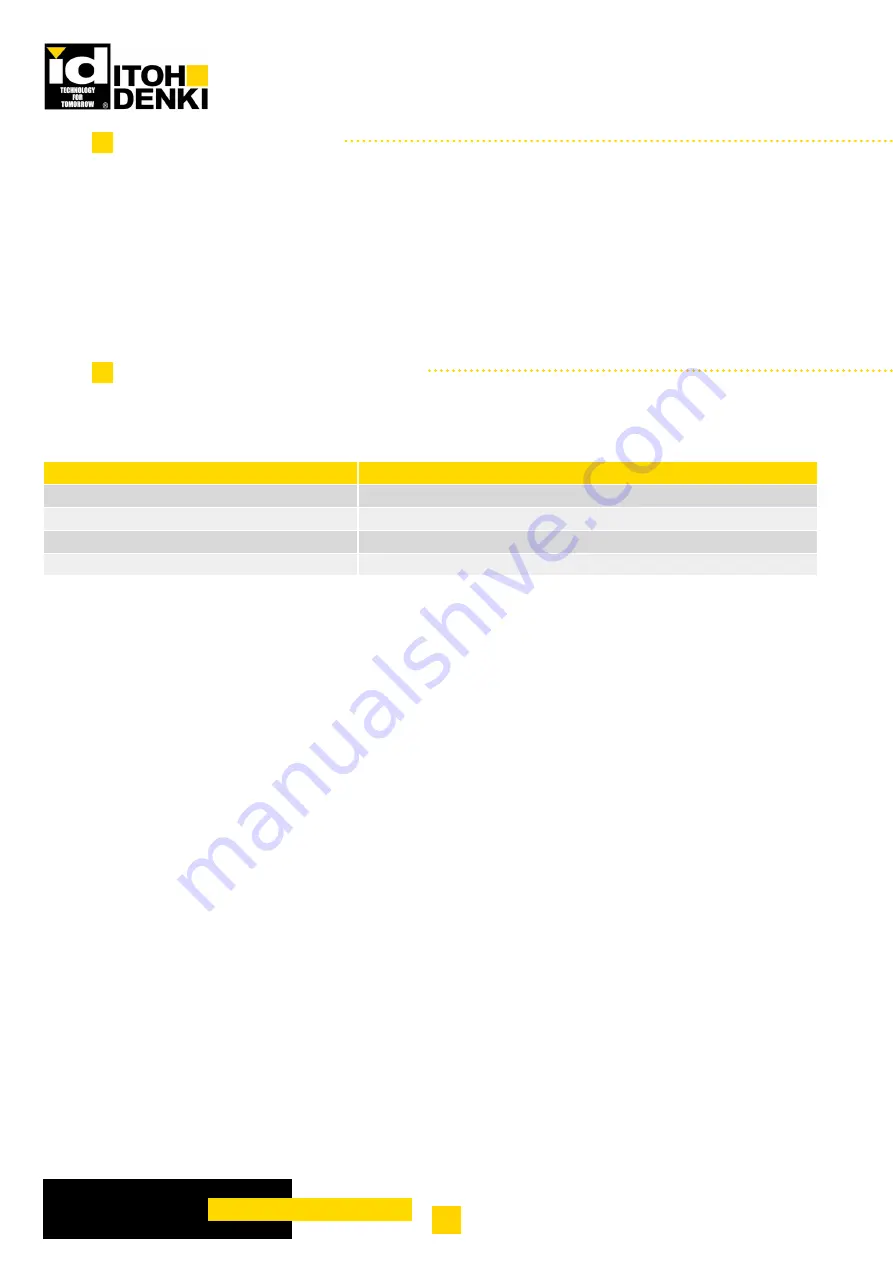
6
IB-P03
T
echnical
documenTaTion
Original notice - T1.10
3.4 - a
PPlicaBle
moTors
The models shown below are available. Contact us for other models.
- Serie PM500VE
- Serie PM605VE
• The driver card can be used for two VE rollers with different tube diameters.
• Cable type: M8-5pin connector cable
• Mechanical brake option is not available for these models.
3.5 - r
ecommended
Power
suPPly
Contents
Conditions
Output voltage
24[V] (within ±10[%])
Rated output current
8[A] or over
Ambient temperature
0°C~40°C
Relative humidity
≤ 90[%RH] (no condensation)
• Switching power supply (24VDC)
• Rectified power (With a rectifying capacitor, ripple rate 10% or below)
A switch power supply is recommended as the DC power supply (24VDC±10%) for controllers. Use a
stabilized power supply which has enough capacity and does not fluctuate due to load variation.
• The power supply shall have a capacity larger than the rated value of MDR*.
• A transformer type power supply cannot be used.
• Secure a voltage of 24VDC±10% at the power supply terminal of the controller.
• If the capacity of the power supply is less than the total rated power of connected MDRs, it may cause the
supply voltage to drop, which leads to a malfunction or to a damage on MDR and/or driver card. Be sure to use
a power supply with a capacity larger than the total rated power of connected MDRs.
• The power supply protection should not be activated with peak current.
Wiring between power supply and IB
• Voltage could drop when the wiring between the power supply and IB gets longer, which might cause
malfunctions or damages.
Separation of power control and power motor
• The power supply for control power and motor power should be different.
• Ensure that all 0v terminals of all power supplies are grounded to the main earth terminal inside the control
cabinet.
*MDR = motorized roller