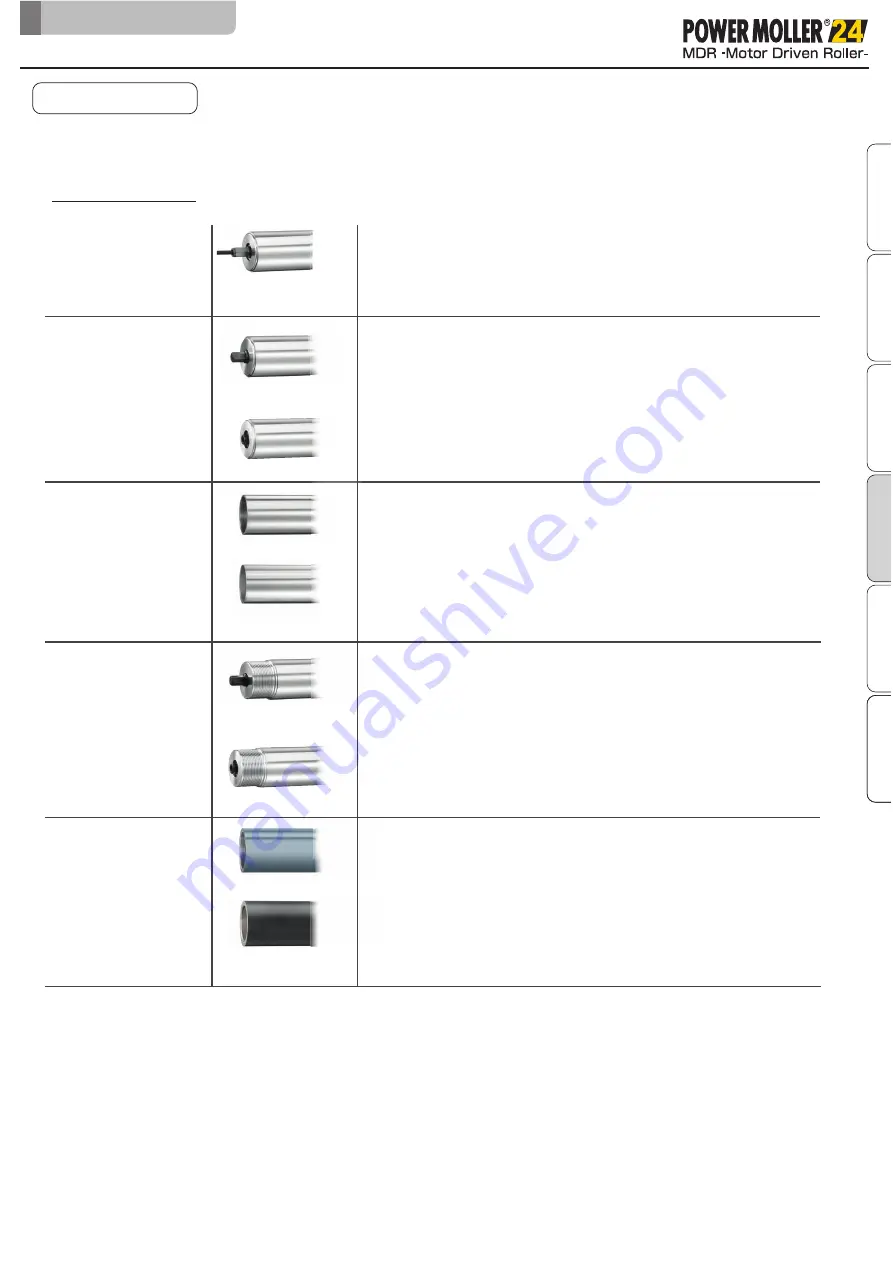
Shaft and flange
motor side :
Shaft and flange
free side :
Tube :
Pulleys :
Lagging :
Plain hexagonal
Polyurethane
Natural rubber / nitrile
Hexagonal spring loaded
Stainless steel
Zinc plated steel
Ribbed with hexagonal
spring loaded
PM605KT/PM605KT-B Technical documentation
21
6. Installation
Original notice - A1.1
6.
Installation
Mechanical option
• Plain hexagonal 13,5mm
• Heat-treated and phosphated steel shaft
• Heat-treated flange
• Plain hexagonal 13,5mm with spring or Ø 15mm x 8mm,
13mm flat M10 threaded (not avalaible for brake version)
• Heat-treated and phosphated steel shaft
• Heat-treated flange
• Polymerized polyurethane coating, thickness 4,75 mm, 90
ShA, grey
• Natural hot vulcanized rubber coating, thickness 4,75 mm,
60~65 ShA
• Tube in precision cold drawn steel, STKM12 quality,
outer diam. 60,5mm
• Zinc plated steel or stainless steel (304L)
6-1.
Set screw
Ribbed with M10 threaded
Safety precautions
Preparation Before Installation
Check product
Installation
Maintenance
Appendix
Pulleys for :
• Ribbed belt 12 teeth, zinc plated steel
• Plain hexagonal 13,5mm with spring
or M10 threaded (not avalaible for brake version)