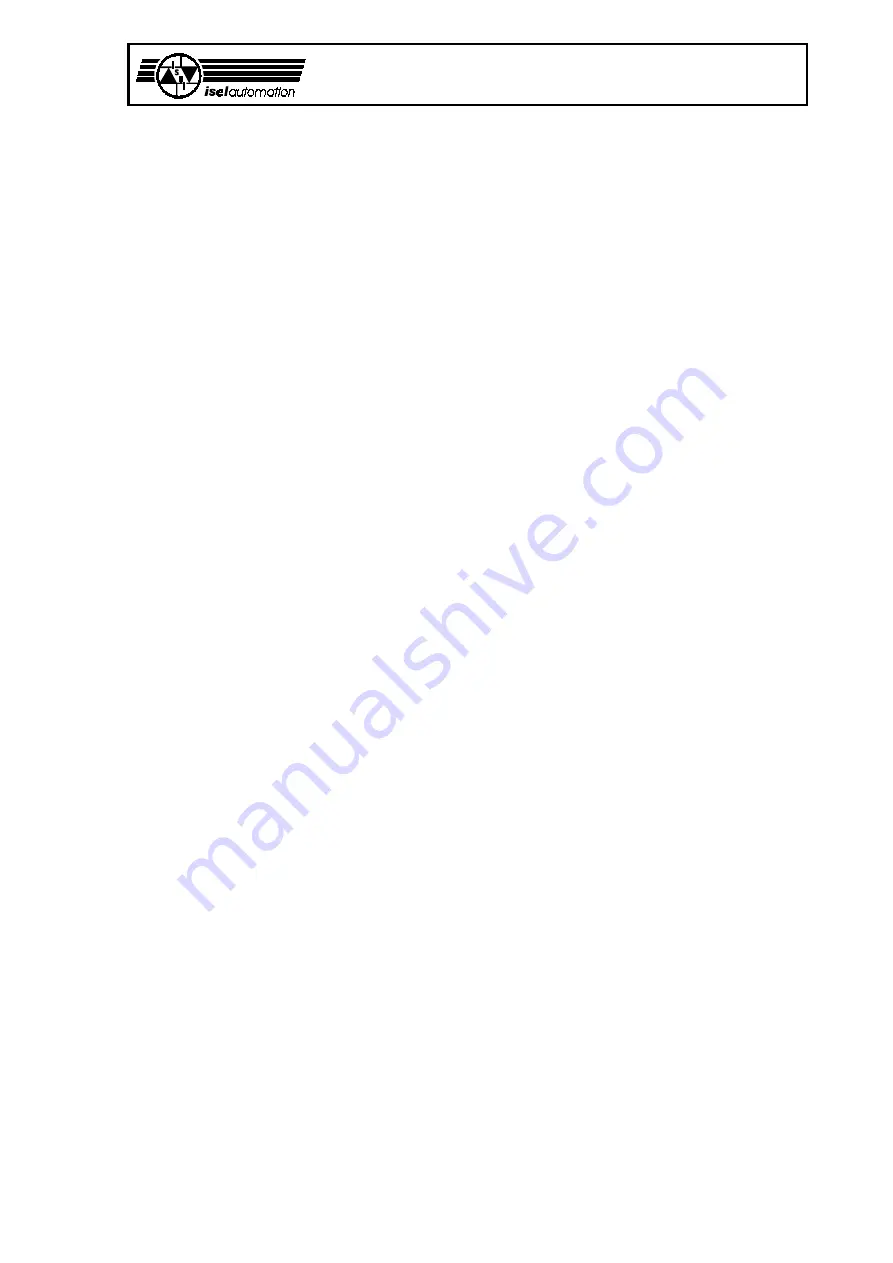
3
isel-
CNC Compact Equipment CPM
This manual includes the instructions for all machines of the CPM type.
The CPM is provided in three different system configurations.
The CPM as a compact equipment
The complete installation (mechanics, electronics, tooling machine and software
(ISY-CAM + REMOTE, I5DRV)) is immediately ready after commissioning.
At every expansion level, the CPM is a compact machine that offers an abundance of
possibilities for processing work pieces.
As a prerequisite for your work with the CPM and depending on the implementation, you
require basic knowledge in CNC engineering and PC application, a computer, a mains
socket, and some creativity.
Please, consider these short instructions to
• properly commission the equipment,
• fast, safely, and effectively work,
• keep away dangers of persons,
• and thus exploit the full potential.
We wish you a lot of success. Enjoy your future working with the CPM.