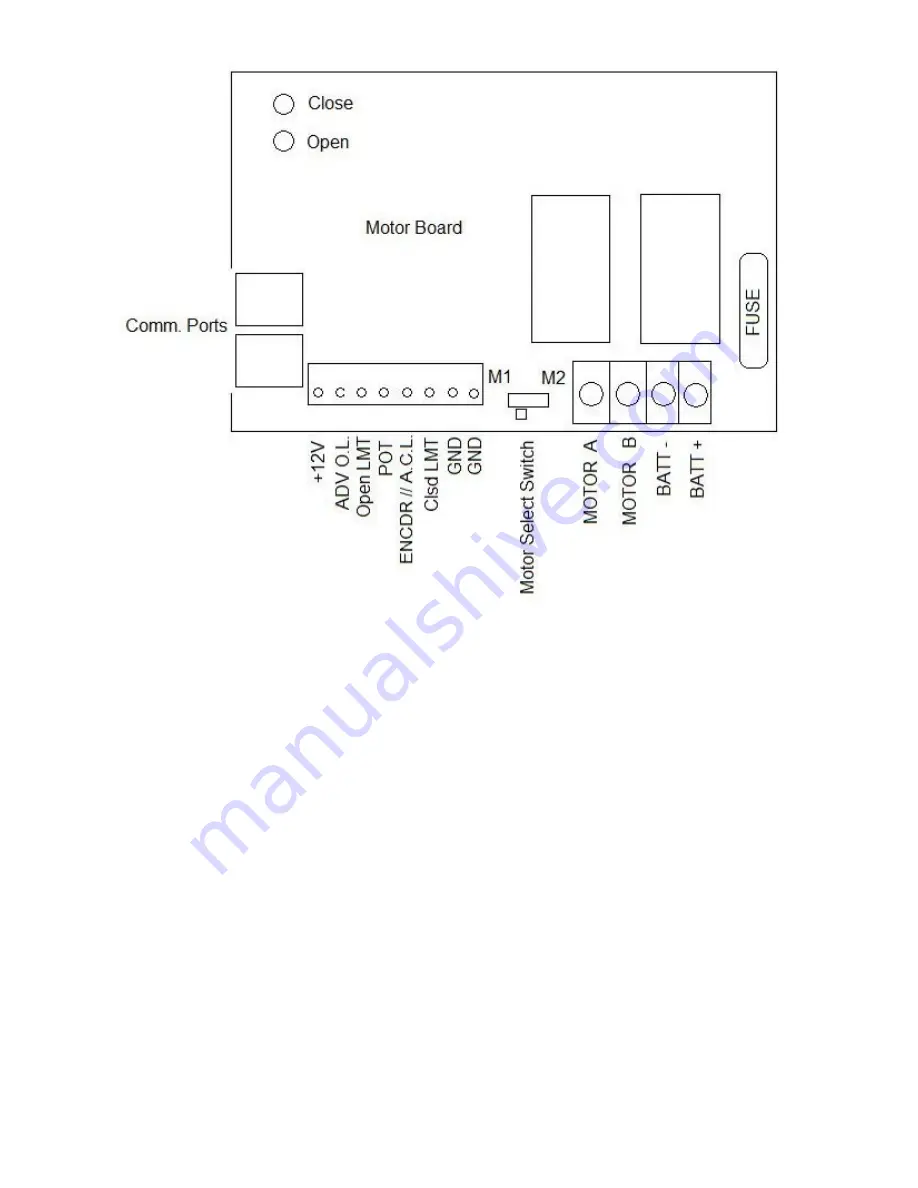
13
The following instructions reference the addition and
The following instructions reference the addition and
The following instructions reference the addition and
The following instructions reference the addition and programming of the on board 433
programming of the on board 433
programming of the on board 433
programming of the on board 433
MHz dual channel receiver
MHz dual channel receiver
MHz dual channel receiver
MHz dual channel receiver
A coaxial cable antenna kit is required for optimum range and reliability of the on board radio receiver
The on board 433mhz dual channel receiver has a set of four dip switches that can be changed to alter the function
of the corresponding channel. Using dip switch 1, channel 1 can be programmed to function as an open only, or a “Radio”
command open, stop, close function; or by turning dip switch 2 on (push to the right), it will allow channel 1 to take the
action that is programmed in the auxiliary input terminal of the “Auxiliary Settings Menu”.
Channel 2 of the receiver is designed to be used as the reversing input channel. Dip switch 3 can be set to reverse
the gate from closing when set as the “SAFE” option, or it can be switched to the “EDGE” option which will reverse the
gate in either direction. When dip switch 4 is turned on, channel 2 will take the action of the auxiliary input terminal that is
programmed in the “Auxiliary Settings Menu”.
The following is how to program a 433 MHz transmitter into the on board receiver:
1.
Push and hold the desired channel “Learn” button (1 or 2) for approximately 2 seconds or until the Green
LED DS27 come on and stays on.
2.
Next, push and hold the button on the remote transmitter until the Green LED blinks twice (about 4 sec).
At this point the remote should be programmed. Test the operation of the remote. Press the system reset button if
the remote doesn’t respond. If the transmitter doesn’t operate gate, repeat steps 1 and 2.
To delete the programmed transmitters in channel 1, push and hold the “LEARN” button until the LED goes out
(approximately 12 seconds)
Transmitter operational range and functionality can and will differ depending on the site of installation and other nearby
obstacles (power lines, electric motors, satellite receivers, fiber optic lines, wireless routers, and other radio frequencies).
No guarantee of operational range should be expected or assumed.