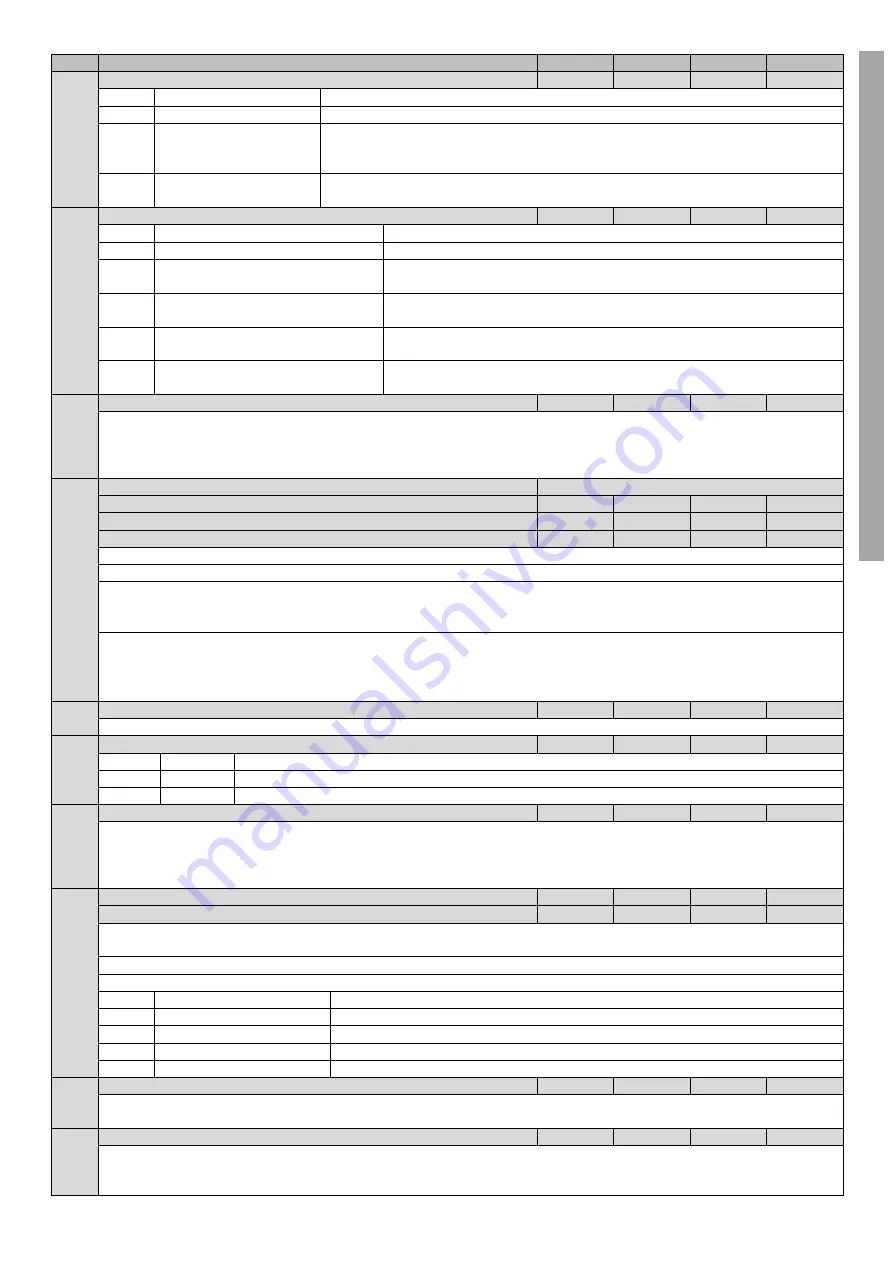
Optidrive E3 Advanced Technical Manual Issue 05.Docx
11 / 69
2
. Opt
id
rive
E3
Par
amet
er
Set Ov
er
vi
ew
Par.
Description
Minimum
Maximum
Default
Units
P-33
Spin Start (S2 & S3 Only) / DC Injection Time On Start (S1 Only)
0
2
0
-
Setting Function
Description
0
Disabled
1
Enabled
When enabled, on start up the drive will attempt to determine if the motor is already
rotating, and will begin to control the motor from its current speed. A short delay may be
observed when starting motors which are not turning.
2
Enabled on Trip, Brown
Out or Coast Stop
Spin start is only activated following the events listed, otherwise it is disabled.
P-34
Brake Chopper Enable (Not Size 1)
0
2
0
-
Setting
Function
Description
0
Disabled
1
Enabled With Software Protection
Enables the internal brake chopper with software protection for a 200W
continuous rated resistor
2
Enabled Without Software Protection
Enables the internal brake chopper without software protection. An external
thermal protection device should be fitted
3
Enabled With Software Protection
As setting 1, however the Brake Chopper is only enabled during a change of the
frequency setpoint, and is disabled during constant speed operation
4
Enabled Without Software Protection
As setting 2, however the Brake Chopper is only enabled during a change of the
frequency setpoint, and is disabled during constant speed operation.
P-35
Analog Input 1 Scaling / Slave Speed Scaling
0.0
2000.0
100.0
%
Analog Input 1 Scaling
. The analog input signal level is multiplied by this factor, e.g. if P-16 is set for a 0 – 10V signal , and the scaling
factor is set to 200.0%, a 5 volt input will result in the drive running at maximum frequency / speed (P-01)
Slave Speed Scaling
. When operating in Slave Mode (P-12 = 9), the operating speed of the drive will be the Master speed multiplied
by this factor, limited by the minimum and maximum speeds.
P-36
Serial Communications Configuration
See Below
Index 1 : Address
0
63
1
-
Index 2 : Baud Rate
9.6
1000
115.2
kbps
Index 3 : Communication loss protection
0
3000
300
ms
This parameter has three sub settings used to configure the Modbus RTU Serial Communications. The Sub Parameters are
Index 1 : Drive Address
: Range : 0 – 63, default : 1
Index 2: Baud Rate & Network type
: Selects the baud rate and network type for the internal RS485 communication port.
For Modbus RTU: Baud rates 9.6, 19.2, 38.4, 57.6, 115.2 kbps are available.
For CAN Open: Baud rates 125, 250, 500 & 1000 kbps are available.
Index 3: Watchdog Timeout
: Defines the time for which the drive will operate without receiving a valid command telegram to
Register 1 (Drive Control Word) after the drive has been enabled. Setting 0 disables the Watchdog timer. Setting a value of 30, 100,
1000, 3000, 10000, 30000 or 60000 defines the time limit in milliseconds for operation. A ‘
’ suffix selects trip on loss of
communication. An ‘
’ suffix means that the drive will coast stop (output immediately disabled) but will not trip.
P-37
Access Code Definition
0
9999
101
-
Defines the access code which must be entered in P-14 to access parameters above P-14
P-38
Parameter Access Lock
0
1
0
-
Setting
Function
Description
0
Unlocked
All parameters can be accessed and changed
1
Locked
Parameter values can be displayed, but cannot be changed except P-38.
P-39
Analog Input 1 Offset
-500.0
500.0
0.0
%
Sets an offset, as a percentage of the full scale range of the input, which is applied to the analog input signal. This parameter
operates in conjunction with P-35, and the resultant value can be displayed in P00-01.
The resultant value is defined as a percentage, according to the following :-
P00-01 = (Applied Signal Level(%) - P-39) x P-35)
P-40
Index 1 : Display Scaling Factor
0.000
16.000
0.000
-
Index 2 : Display Scaling Source
0
3
0
-
Allows the user to program the Optidrive to display an alternative output unit scaled from either output frequency (Hz), Motor
Speed (RPM) or the signal level of PI feedback when operating in PI Mode.
Index 1:
Used to set the scaling multiplier. The chosen source value is multiplied by this factor.
Index 2 :
Defines the scaling source as follows :-
Setting Function
Description
0
Motor Speed
Scaling is applied to the output frequency if P-10 = 0, or motor RPM if P-10 > 0.
1
Motor Current
Scaling is applied to the motor current value (Amps)
2
Analog Input 2 Signal Level
Scaling is applied to analog input 2 signal level, internally represented as 0 – 100.0%
3
PI Feedback
Scaling is applied to the PI feedback selected by P-46, internally represented as 0 – 100.0%
P-41
PI Controller Proportional Gain
0.0
30.0
1.0
-
PI Controller Proportional Gain. Higher values provide a greater change in the drive output frequency in response to small changes
in the feedback signal. Too high a value can cause instability
P-42
PI Controller Integral Time
0.0
30.0
1.0
s
PI Controller Integral Time. Larger values provide a more damped response for systems where the overall process responds slowly