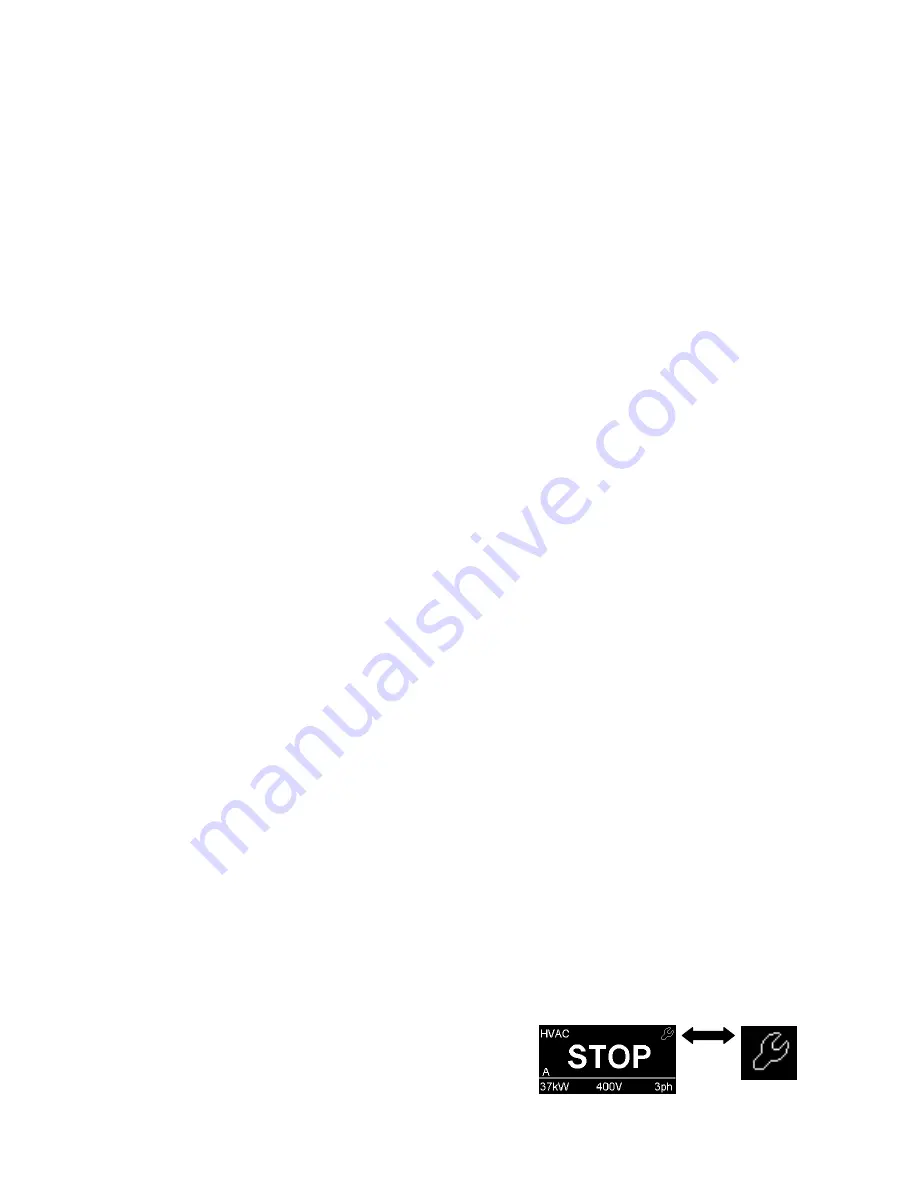
Optidrive
ODV
‐
2
User
Guide
Revision
1.00
www.invertek.co.uk
40
In
addition,
the
value
of
P8
‐
15
on
the
network
master,
‘Pump
staging
DOL
pump
availability’
must
be
set
with
the
number
of
additional
drives
available
in
the
system
(slave
drives),
excluding
the
master
(set
to
a
value
other
than
0).
The
master
drive
must
be
set
to
drive
address
1
(default),
with
the
addresses
of
the
slave
drives
set
in
sequence
to
subsequent
addresses
(2.
3.
4.
5...).
Addresses
are
set
within
P5
‐
01.
When
the
system
is
enabled
the
master
drive
will
check
the
run
time
clocks
for
all
drives
in
the
network
which
are
stored
and
maintained
within
menu
0
of
the
master
drive.
The
first
available
drive
with
the
lowest
run
time
is
automatically
run
first.
At
a
predefined
level
additional
drives
/
pumps
are
brought
on
‐
line
in
sequence
to
assist
the
running
pumps.
Switch
on
sequence
is
always
defined
by
the
pump
run
time
clocks
of
the
available
drives
(monitored
and
maintained
by
the
master
drive)
with
the
least
run
time
pump
switched
in
first.
A
pre
‐
defined
settle
time
(Set
in
P8
‐
19)
is
observed
before
any
further
pumps
are
switched
in
or
out
of
the
system.
This
allows
the
system
to
reach
a
steady
operating
state
before
additional
pump
requirements
are
assessed.
Pump
switch
off
is
done
at
a
predefined
level
in
the
sequence
of
least
run
time.
Maximum
and
minimum
speed
and
Ramp
times
for
each
drive
in
the
network
are
determined
by
the
individual
setting
on
each
drive
(P1
‐
01
to
P1
‐
04).
The
maximum
difference
in
run
time
between
drives
/
pumps
can
be
limited
by
setting
the
‘Pump
Staging
Duty
Switch
Over
Time’
parameter
(P8
‐
16).
When
a
value
is
entered
into
P8
‐
16
the
network
master
drive
will
automatically
switch
off
the
drive
/
pump
with
the
longest
run
time
and
switch
in
the
drive
/
pump
with
the
shortest
run
time
once
the
difference
in
run
times
set
in
P8
‐
16
is
exceeded.
When
P8
‐
16
is
set
to
0
pump
switch
‐
over
based
on
run
time
is
disabled
and
switch
over
is
determined
only
by
the
threshold
limits
(demand
based).
Duty
run
time
clocks
are
available
to
view
in
P0
‐
12
of
the
network
master
drive.
Clocks
are
reset
by
setting
parameter
P8
‐
20
‘Pump
Staging
Master
Clock
Reset’
to
1
(reset)
on
the
network
master
drive.
The
Network
Master
will
assume
that
any
drive
not
responding
to
network
messaging
is
currently
unavailable
(powered
off
/
RS485
disconnected).
The
Network
master
will
continue
to
poll
drives
that
are
offline
but
will
not
attempt
to
run
the
drive
until
communication
is
re
‐
established.
When
any
drive,
including
the
network
master,
enters
into
a
trip
condition
it
will
be
temporarily
suspended
from
operation
and
the
system
will
maintain
operation
with
the
remaining
available
drives.
When
a
drive
is
reset
from
a
trip
condition
it
will
automatically
become
available
for
selection
by
the
network
master.
The
enable
input
(T1
–
T2)
to
the
network
master
is
deemed
to
be
the
enable
for
the
complete
system
and
causes
system
operation
to
start
or
stop.
Individual
enable
inputs
(T1
–
T2)
on
the
network
slave
drives
provide
an
inhibit
input
that
prevent
operation
of
that
particular
drive.
Quick
Setup
Overview:
On
all
HVAC
Drives
•
Set
Basic
parameters
P1
‐
01
to
P1
‐
10
on
all
drives
in
the
system.
Energy
Optimiser
P1
‐
06
must
remain
disabled.
•
Set
Parameter
P1
‐
14=
101
to
allow
access
to
extended
parameters
On
the
Network
Master
•
In
Menu
3,
Configure
parameters
for
the
PID
Control
•
Ensure
the
network
serial
address
in
P5
‐
01
is
left
as
default
(1)
•
Set
parameter
P8
‐
14=2
to
enable
the
Pump
staging
–
Multiple
Drive
Cascade
function
•
Set
the
number
of
network
slave
pumps
available
in
the
system
(not
including
Network
Master
VFD)
in
P8
‐
15
•
Set
Optidrive
HVAC
operating
speed
limits
used
to
activate
/
deactivate
network
slave
pumps
as
follows:
o
P8
‐
17:
Pump
Staging
Assist
Switch
In
Speed
–
Threshold
to
bring
in
assist
pump
o
P8
‐
18:
Pump
Staging
Assist
Switch
Out
Speed
–
Threshold
to
switch
out
assist
pump
•
Set
a
pump
staging
settle
time
(minimum
10
seconds)
in
P8
‐
19.
The
time
entered
in
P8
‐
19
must
be
sufficient
for
the
PID
feedback
signal
from
the
system
output
sensor
to
settle
to
a
steady
level.
•
If
the
duty
run
times
between
all
available
drives
/
pumps
are
to
be
balanced
then
the
maximum
permissible
difference
in
hours
should
be
entered
in
P8
‐
16.
On
the
Network
Slaves
•
Set
the
drives
to
network
slaves
by
setting
P1
‐
12
=
5
•
Set
the
network
serial
address
in
P5
‐
01
to
unique
addresses
is
sequence,
starting
at
address
2
(2,
3,
4,
5...)
13.3.
Maintenance
Interval
Set
‐
up
and
Reset
The
Optidrive
HVAC
has
a
maintenance
interval
timer
function
with
visible
display
indication
and
configurable
output
points
to
allow
the
programmer
to
set
‐
up
routine
maintenance
schedules
/
intervals
for
the
machine
/
system
and
to
indicate
maintenance
due
to
the
machine
operator.
The
maintenance
interval
is
calculated
from
the
‘Drive
hours
run
clock’
and
is
hence
an
indication
of
the
operational
use
of
the
drive
system
rather
than
a
basic
calendar
based
timer
function.
Operational
Overview:
The
maintenance
interval
is
enabled
and
configured
by
parameter
P6
‐
24,
Service
Interval
Timer.
When
P6
‐
24
is
set
to
0
the
maintenance
interval
timer
is
disabled.
The
maintenance
interval
(P6
‐
24)
is
set
in
hours
between
1
and
60000
(default
5000
hours).
Access
to
parameter
menu
6
is
permitted
only
when
the
advanced
security
level
password
is
entered
into
P1
‐
14
(default
password
201).
The
maintenance
interval
timer
is
initiated
when
a
valid
value
is
entered
into
P6
‐
24.
The
time
remaining
until
maintenance
becomes
due
is
stored
and
displayed
in
parameter
P0
‐
22
(Time
Left
to
Next
service).
When
the
maintenance
interval
expires
(P0
‐
22
reaches
0)
the
Optidrive
HVAC
can
indicate
maintenance
due
on
the
machine
in
the
following
ways:
•
The
maintenance
symbol
is
automatically
displayed
on
the
OLED
display
(alternating
with
drive
communications
address
in
top
right
corner.
•
One
of
the
drive
relay
outputs
can
be
configured
for
indication
of
maintenance
due,
•
A
warning
bit
in
the
drive
communications
status
words
is
set
(see
associated
communications
guide).
Summary of Contents for Optidrive HVAC Series
Page 1: ......