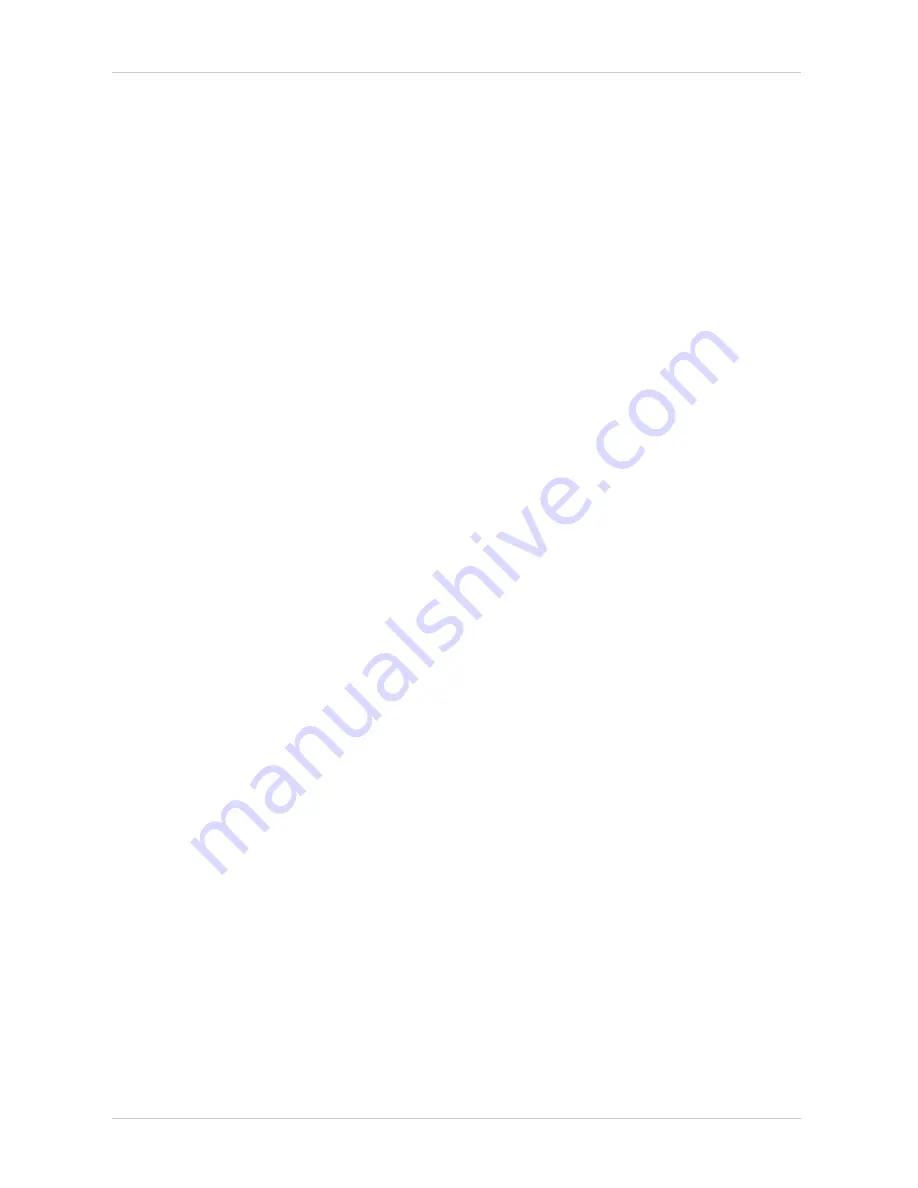
SERVICE MANUAL
Invacare
®
- Kite
58
•
Loosen both Phillips screws (1).
•
Detach the headlight from its holding bracket.
•
Replace the headlight.
Installing headlights:
•
Assemble all parts again in reverse order.
•
Install the cables carefully and secure them with cable ties.
•
Tighten the screws hand-tight.
•
Check all vehicle functions.
•
Perform an approximate adjustment of the headlight using the ratchet plate as a guide. The
final adjustment can be performed by the user according to the instructions found in the User
Guide.