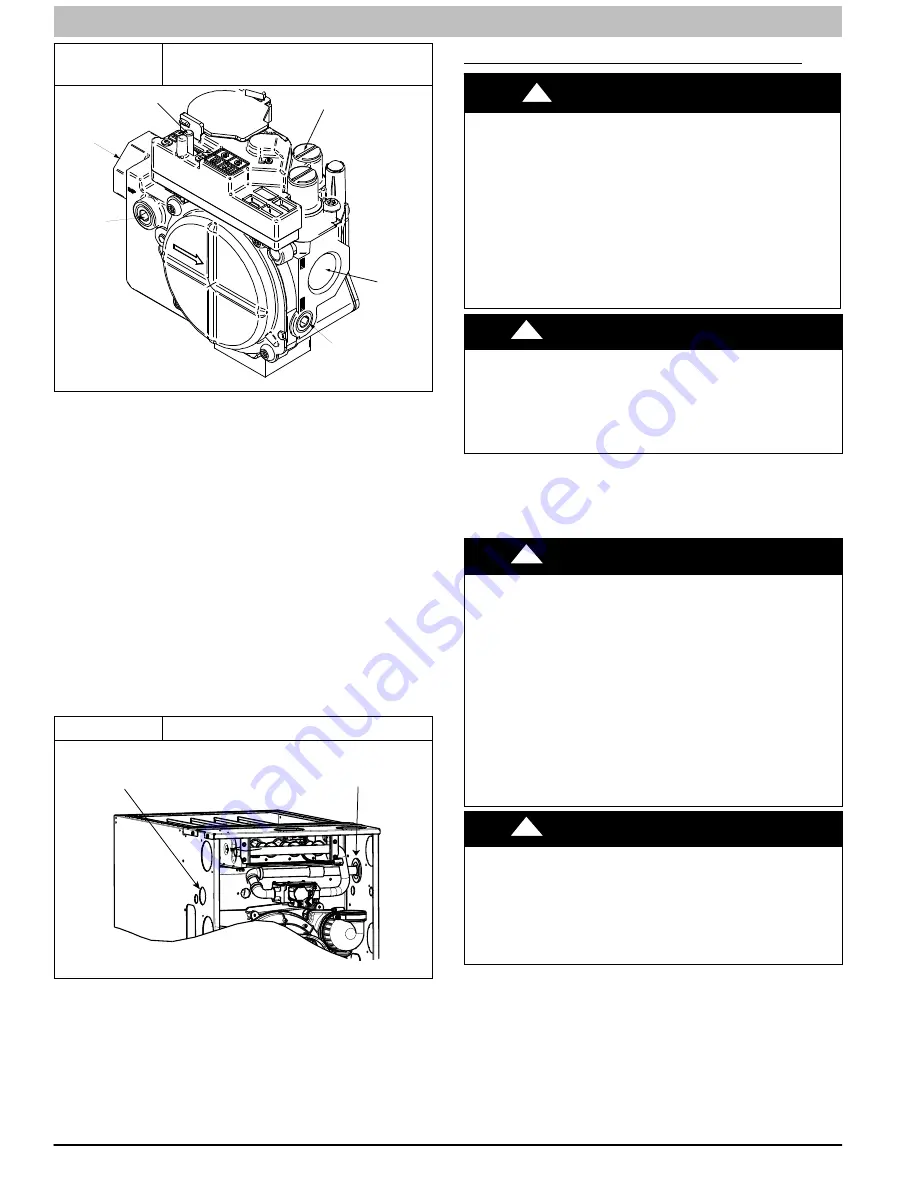
INSTALLATION INSTRUCTIONS
Gas Furnace: (F/G)9MVE
30
440 01 4400 03
Specifications subject to change without notice.
Figure 33
Redundant Automatic Gas Valve
(Two
−
Stage)
ON/OFF Switch
Regulator Seal Cap
Regulator Adjustment
Regulator Seal Cap under Cap
1/2” NPT Outlet
1/8” NPT Manifold
Pressure Tap
1/8” NPT Inlet
Pressure Tap
1/2” NPT Inlet
A11152
If pressure exceeds 0.5 psig (14
−
in. w.c.), gas supply pipe must
be
disconnected from furnace and capped before and during
supply
pipe pressure test. If test pressure is equal to or less
than 0.5 psig
(14
−
in. w.c.), turn off electric shutoff switch
located on furnace gas control valve and accessible manual
equipment shutoff valve before and during supply pipe
pressure test. After all connections have been made, purge
lines and check for leakage at furnace prior to operating
furnace.
The gas supply pressure shall be within the maximum and
minimum inlet supply pressures marked on the rating plate with
the furnace burners ON and OFF.
Some installations require gas entry on right side of furnace (as
viewed in upflow). (See
)
Gas Pipe Grommet
For direct vent (2-pipe) applications, the knockout for the gas
pipe must be sealed to prevent air leakage. Remove the
knockout, install the grommet in the knockout, then insert the
gas pipe. The grommet is included in the loose parts bag. (See
Figure 34
Gas Entry
Gas Pipe Grommet Required
For Direct Vent Applications
Left Side Gas Entry. Gas Pipe
Grommet Required For Direct
Vent Applications.
A11338
ELECTRICAL CONNECTIONS
ELECTRICAL SHOCK, FIRE OR EXPLOSION
HAZARD
Failure to follow safety warnings could result in
dangerous operation, serious injury, death or property
damage.
Improper servicing could result in dangerous
operation, serious injury, death or property damage.
Before servicing, disconnect all electrical
power to furnace.
When servicing controls, label all wires prior
to disconnecting. Reconnect wires correctly.
Verify proper operation after servicing.
!
WARNING
WARNING
!
ELECTRICAL SHOCK HAZARD
Failure to follow this warning could result in personal injury
or death.
Blower door switch opens 115
−
v power to control. No
component operation can occur. Do not bypass or close
switch with blower door removed.
See
for field wiring diagram showing typical field
115
−
v wiring. Check all factory and field electrical connections
for tightness.
Field
−
supplied wiring shall conform with the limitations of 63
°
F
(33
°
C) rise.
WARNING
!
ELECTRICAL SHOCK AND FIRE HAZARD
Failure to follow this warning could result in personal
injury, death, or property damage.
The cabinet MUST have an uninterrupted or unbroken
ground according to NEC ANSI/NFPA 70
−
2011 or local
codes to minimize personal injury if an electrical fault
should occur. In Canada, refer to Canadian Electrical
Code CSA C22.1. This may consist of electrical wire,
conduit approved for electrical ground or a listed,
grounded power cord (where permitted by local code)
when installed in accordance with existing electrical
codes. Refer to the power cord manufacturer’s ratings
for proper wire gauge.
Do not use gas piping as an electrical ground.
CAUTION
!
FURNACE MAY NOT OPERATE HAZARD
Failure to follow this caution may result in intermittent
furnace operation.
Furnace control must be grounded for proper operation
or else control will lock out. Control must remain
grounded through green/yellow wire routed to gas
valve and manifold bracket screw.
115
−
V Wiring
Furnace must have a 115-v power supply properly connected
and grounded.
NOTE
: Proper polarity must be maintained for 115-v wiring. If
polarity is incorrect, control status indicator light flashes rapidly
and furnace does
NOT
operate.
Verify that the voltage, frequency, and phase correspond to that
specified on unit rating plate. Also, check to be sure that
service provided by utility is sufficient to handle load imposed