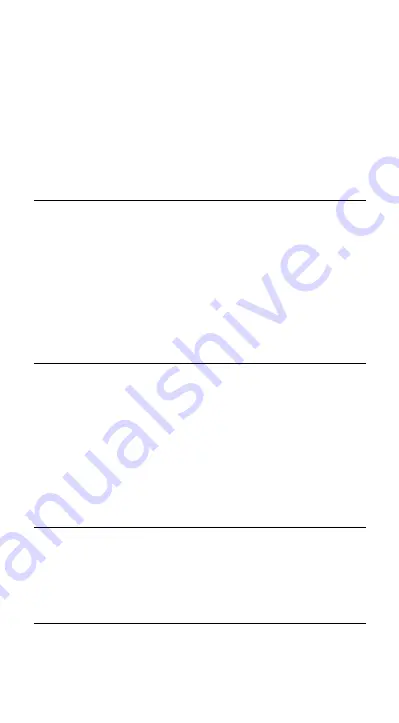
Electromagnetic Compatibility
Where
applicable,
this
equipment
is
designed
to
comply
with
International
Electromagnetic
Compatibility
(EMC)
standards.
To
ensure
reproduction
of
this
EMC
performance,
connect
this
equipment
to
a
low
impedance
ground
connection.
Typical
suitable
connections
are
a
ground
spike
or
the
steel
frame
of
a
building.
Proprietary Rights Notice
This
document
and
the
information
that
it
contains
are
the
property
of
Illinois
Tool
Works
Inc.
(ITW).
Rights
to
duplicate
or
otherwise
copy
this
document
and
rights
to
disclose
the
document
and
the
information
that
it
contains
to
others
and
the
right
to
use
the
information
contained
therein
may
be
acquired
only
by
written
permission
signed
by
a
duly
authorized
officer
of
ITW.
Trademarks
Instron®
is
a
registered
trademark
of
Illinois
Tool
Works
Inc.
(ITW).
Other
names,
logos,
icons
and
marks
identifying
Instron
products
and
services
referenced
herein
are
trademarks
of
ITW
and
may
not
be
used
without
the
prior
written
permission
of
ITW.
Other
product
and
company
names
used
herein
are
trademarks
or
trade
names
of
their
respective
companies.
© Copyright 2012 Illinois Tool Works Inc.
All rights reserved.
All of the specifications shown in this document
are subject to change without notice.
Original language
Product Support: www.instron.com