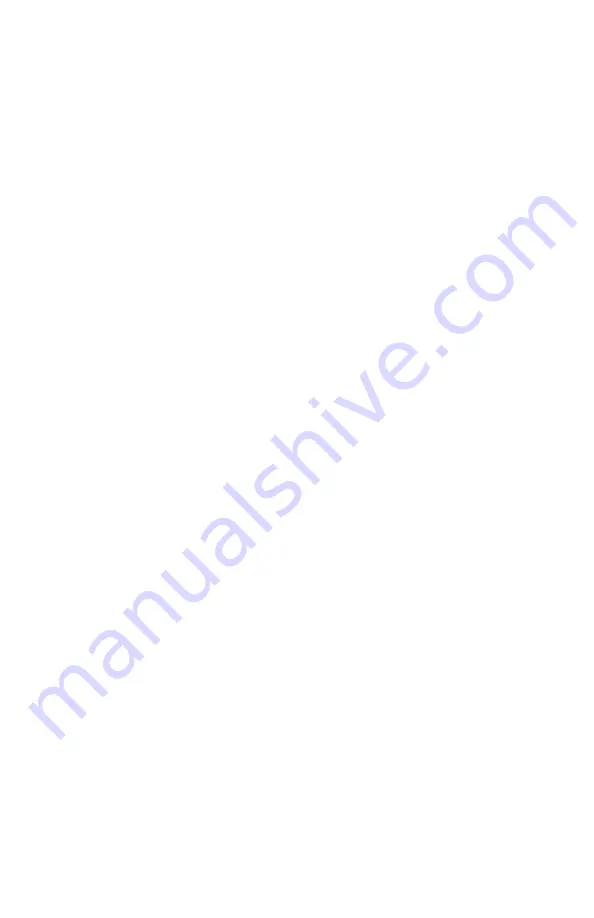
7
2.
Locate a vacuum source on the intake manifold, after the throttle
body and connect it to the hose barb on the sensor. Use the
provided “T” and hose to make this connection if needed. To secure
the hose use tie-wraps or hose clamps.
3.
With the engine idling, confirm that you do not have any air/vacuum
leaks.
2.5
Wideband Oxygen Sensor Setup
2.5.1
Oxygen Sensor Placement
Optimum bung placement will vary from application to application, but using
the guidelines below will ensure the longest sensor life with the most
accurate readings. Using a bung is the preferred method for mounting the
oxygen sensor in all applications.
Weld the bung at least
24 inches
after the turbocharger.
Using a clock as reference, mount the bung between the
9:00
o’clock and 3:00 o’clock position
. Welding the bung in the lower
section of the exhaust pipe can result in sensor damage caused by
condensation making contact with the sensor’s internal heating
element.
A
1” bung
(provided in the kit) will best protect the sensor. When
fully threaded, the sensor’s tip will sit flush with the inside of the
exhaust piping, this does
not
adversely effect the readings.
The bung should always be welded before the Catalytic Converter.
Welding the bung after the catalytic converter will skew the readings
toward lean. The skew in readings will vary with engine load and the
efficiency of the catalytic converter.
Leaded fuel and two stroke applications will reduce the sensor’s life.
There are many other factors that dictate the sensor’s lifespan so it is
impossible to predict total sensor longevity.
Exhaust leaks, camshaft overlap, and open (shorty) exhausts will
cause false lean readings at light engine loads. Typically, once the
engine is under load and the exhaust gas volume increases, you will
see accurate readings.